Stop Overlooking Quality: The dss+ 6 Key Phases of Quality Management for Successful Turnarounds
The 2010 US Tesoro Refinery explosion serves as a stark reminder: neglecting quality can have catastrophic consequences. In the rush to meet deadlines and budgets, quality often gets sidelined — but this is a dangerous oversight.
At dss+, we’ve developed a proven approach to ensure quality is never compromised during turnarounds. By integrating quality management into every phase, from planning through execution, we help organszations minimise risk, prevent rework, and achieve flawless performance.
The result? Zero trips, zero leaks, and turnarounds that deliver on safety, efficiency, and long-term reliability.
Discover the dss+ 6 Key Phases of Quality Management for Successful Turnarounds.
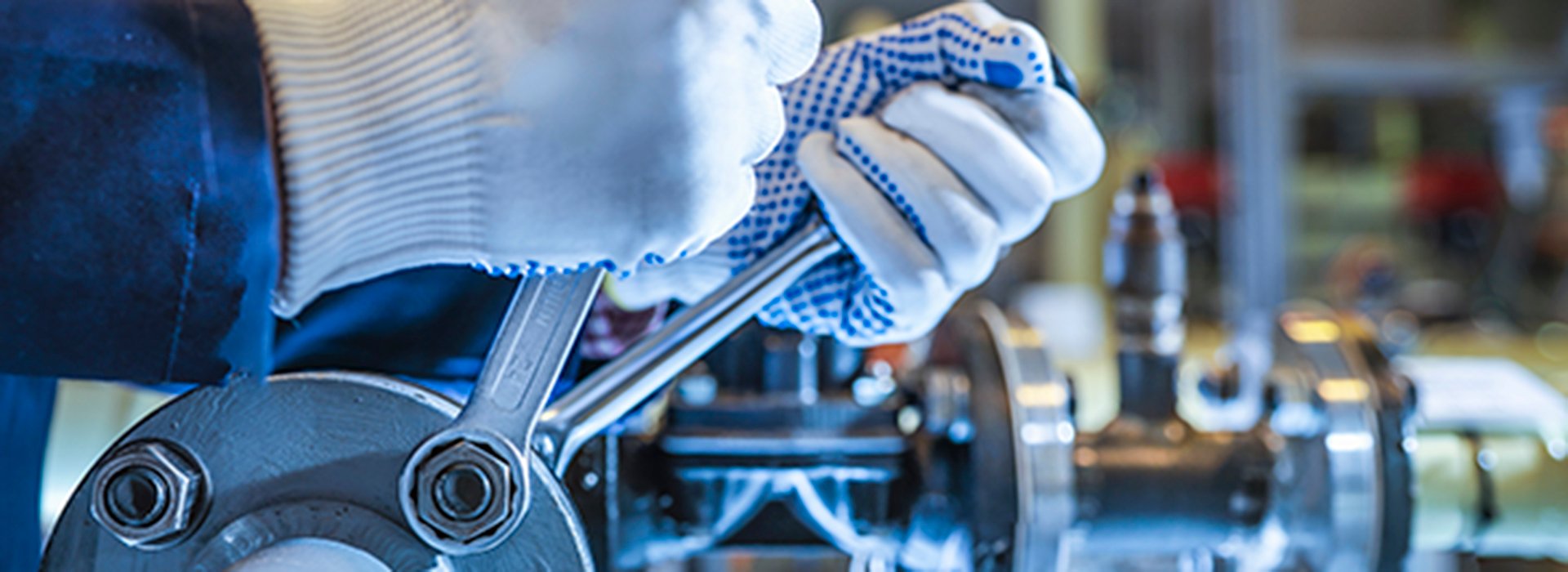
Introduction
The success of turnarounds is typically measured by the ability to complete them safely, on time, and within budget. However, quality goals are as crucial as safety, delivery, and cost considerations. Given the inherently time-sensitive nature of turnarounds, this raises a vital question: how can we ensure that quality is never compromised in our pursuit of timely, safe and budget-conscious delivery?
In April 2010, an explosion at the Tesoro Petroleum Refinery in Anacortes, Washington, United States, tragically claimed the lives of seven workers due to equipment failure and insufficient maintenance practices. A critical finding was the lack of proper inspections on a heat exchanger, representing a significant quality breach that played a major role in this catastrophic incident.
While challenges arise during turnarounds, incidents like the April 2010 Tesoro explosion in the United States, highlight crucial lessons. Investigations revealed that critical equipment inspections had been overlooked, underscoring the urgent need for a strong focus on quality.
Although not every quality lapse leads to a major incident, it can significantly impact an organisation’s financial and operational health. Poorly executed jobs often surface during or after a turnaround, resulting in excessive rework, startup delays, and plant trips that lead to production losses. These issues can significantly extend the duration of turnarounds and cause further production disruptions.
The solution is clear: in addition to safety, organisations must prioritise quality throughout all turnaround planning and preparation phases. Emphasising quality is essential for the longterm viability of operations and fosters a culture of continuous improvement.
Integrating quality into every phase of turnaround management is crucial to effectively navigating the complexities of turnarounds.
This requires meticulous planning, rigorous monitoring, and robust verification processes, all contributing to successful outcomes and operational excellence. By prioritising quality at every stage, organisations can prevent potential crises and lay the groundwork for sustained operational success.
Figure 1: Quality in various stages of turnaround
Conclusion
Quality management is essential for successful turnaround projects, serving as a foundational pillar that ensures safety, timeliness, and operational reliability.
Embedding industry-leading best practices, structured rituals, and targeted coaching across departments cultivates a culture of continuous improvement and drives cross-functional synergies in Quality Management.
By aligning teams around shared objectives and fostering robust capabilities, organisations can deliver sustainable quality performance throughout the turnaround lifecycle. This integrated approach not only enhances operational efficiency but also strengthens the organisation’s ability to proactively address complex challenges, ensuring that safety and reliability are uncompromised at every stage.
Lessons from past incidents, such as the Tesoro Petroleum Refinery explosion, emphasise the necessity of rigorous quality assurance practices. Implementing structured tools like Inspection Test Plans (ITPs), Daily Quality Reports, and comprehensive material inspection protocols foster accountability and continuous improvement, allowing teams to address potential issues proactively.
Utilising various quality management tools ensures that standards are met throughout the turnaround lifecycle. For instance, visual boards for tracking hold points and quality audits provide real-time insights, while contingency planning frameworks prepare teams for unexpected challenges. These tools contribute to a cohesive strategy that drives effective execution and minimises disruptions.
In summary, integrating quality management into turnaround projects is not only a necessity but a strategic advantage.
Organisations that adopt this approach will improve immediate project performance and establish a resilient foundation for future endeavours. As the industry evolves, a steadfast commitment to quality will remain crucial for sustainable success and operational excellence.
Contacts
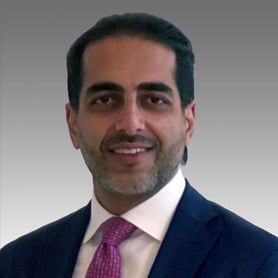
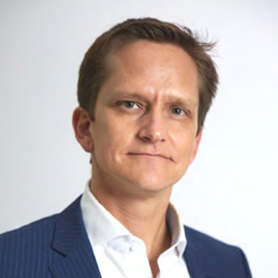
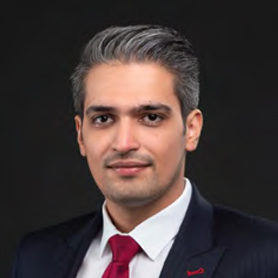
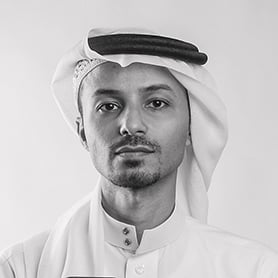