Elevating Turnaround Success: The Critical Role of Quality Management
The 2010 US Tesoro Refinery explosion — resulting in seven fatalities — remains a powerful industry wake-up call. Despite meeting operational timelines, the failure stemmed from poor maintenance and critical lapses in inspection — a stark reminder that schedule and budget mean little without quality assurance.
In today’s complex operating environments, quality is not a support function — it is a strategic driver of asset reliability, operational integrity, and long-term performance. Overlooking it invites rework, production losses, and unmitigated risk.
True turnaround success demands more than speed and cost control — it requires embedding quality at every phase. From upfront planning through execution, it must be treated as a non-negotiable pillar of performance.
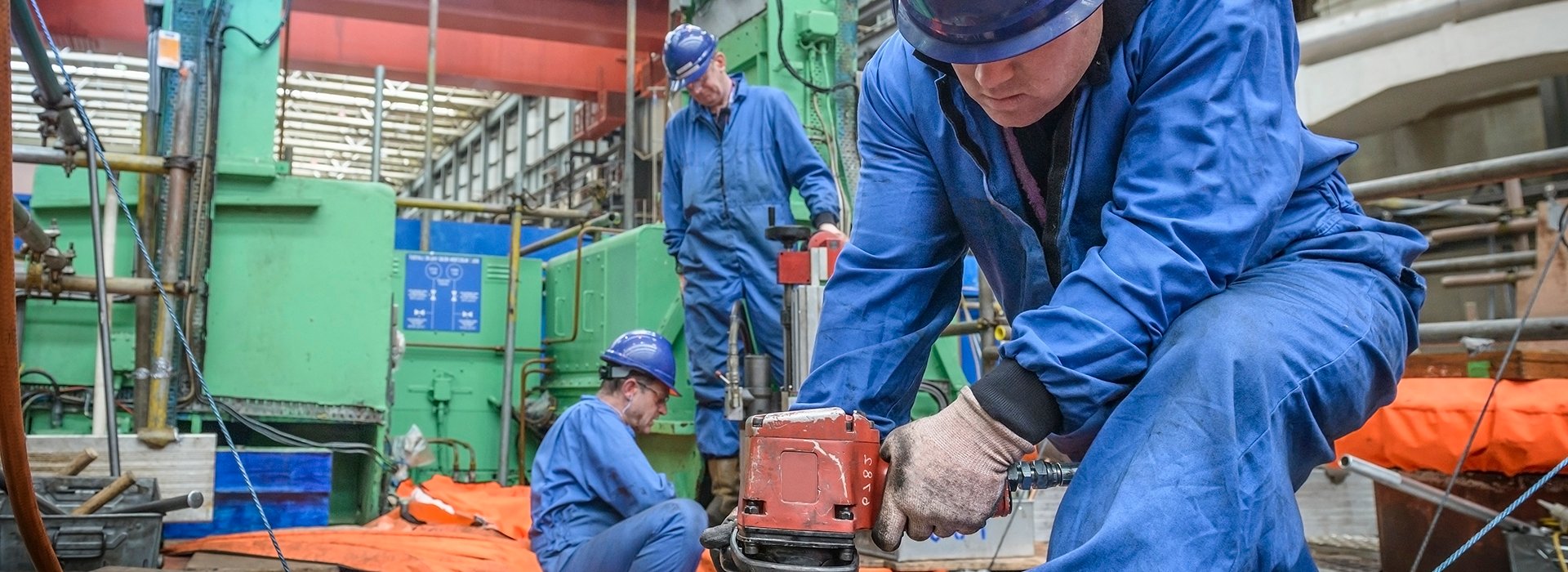
Introduction
Turnaround success is usually measured by safe performance, on-time delivery, and on-budget completion; however quality is equally crucial. A key question arises, how do we ensure quality during such time-sensitive turnarounds
The 2010 Tesoro Petroleum Refinery explosion in the United States, which resulted in seven fatalities due to equipment failure and poor maintenance highlight this urgency. Investigations revealed critical lapses in inspections, emphasising the need for a strong quality focus.
While not all oversights lead to disasters, they can harm an organisation’s financial and operational health, causing rework, delays, and production losses. Therefore, prioritising quality in turnaround planning and execution is vital for long-term operational viability.
Conclusion
To ensure safe, reliable, and successful turnarounds, quality management must be embedded in every stage — safeguarding the plant’s operational integrity and efficiency. Integrating quality at all phases mitigates risks and prevents costly oversights. Past industry incidents highlight the need for rigorous practices.
Embedding industry-leading best practices, structured rituals, and targeted coaching across departments cultivates a culture of continuous improvement and drives cross-functional synergies in Quality Management. By aligning teams around shared objectives and fostering robust capabilities, organisations can deliver sustainable quality performance throughout the turnaround lifecycle. This integrated approach not only enhances operational efficiency but also strengthens the organisation’s ability to proactively address complex challenges, ensuring that safety and reliability are uncompromised at every stage.
Tools like Inspection Test Plans (ITPs) and Daily Quality Reports promote accountability and improvement. Visual boards and contingency plans help meet standards and prepare teams for challenges, driving effective execution.
Overall, quality management is a strategic advantage that enhances turnaround performance and is vital for operational excellence.
Contacts
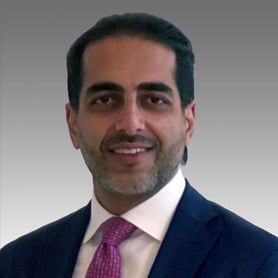
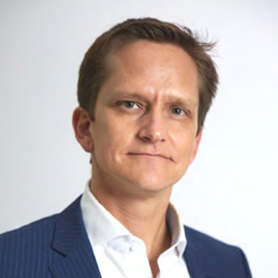
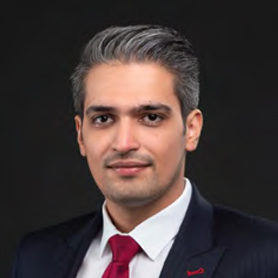
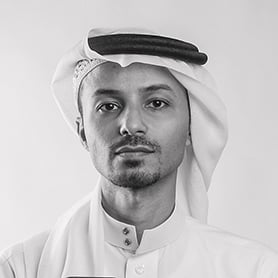