SIBUR
Fast expansions have their challenges. In order to be competitive in the global market, large companies continually need to improve their performance and productivity. For SIBUR – one of the world's largest petrochemical companies with production sites in the Confederation of Independent States, Central and Eastern Europe – that meant deploying a production system with the help of consultants from dss+. Since starting the process in 2009, the financial value of SIBUR's pipeline of improvement projects has more than doubled. Through 2013, SIBUR estimates the financial benefits from the SIBUR Production System at twenty times its investment with dss+.
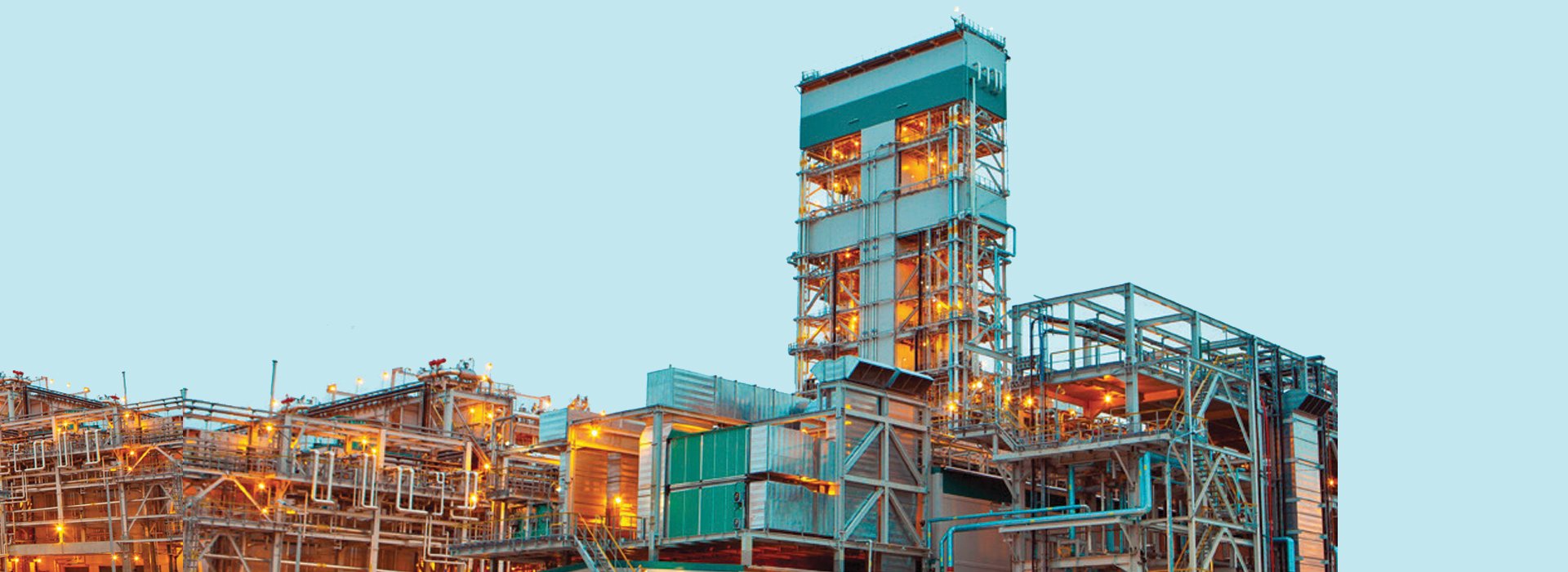
Keeping a Firm Grip on Productivity: Petrochemical Giant SIBUR Introduces a New Production System
Overview
SIBUR is the largest petrochemical company in the Confederation of Independent States, Central and Eastern Europe, with 2013 sales of over $8 billion USD, 27 production locations in Russia, as well as several joint ventures with major international companies in Russia and abroad. Founded in 1995, it rapidly grew into a holding company with numerous largely independent entities through a number of mergers and acquisitions. Yet the company's extremely fast growth has brought its own challenges.
Senior management recognized that there were significant competitive gaps compared to world-class companies outside of the home market. Leaders had concerns about the condition of SIBUR assets and the ability of the organization to improve and sustain its performance. Its fragmented structure had also resulted in a highly disengaged workforce which made operational control challenging.
As Mr. Vladimir Razumov, Deputy Management Board Chairman and Executive Director of SIBUR succinctly puts it: "We knew that it was not necessarily required, to work more, but to work more productively."
SIBUR needed to turn its very large holding company into a single corporation with a cohesive, unifying culture in order to truly engage its workforce and close competitive gaps. With nearly 50,000 employees and 27 production sites achieving this was an enormous task.
Finding the right approach
SIBUR operates across the entire petrochemical process chain including gas processing, the production of monomers and polymers, plastics and rubber. In 2008, the company engaged dss+ to work with it on a safety culture improvement project.
During the course of an executive coaching program intended to demonstrate safety best practices, senior SIBUR managers visited a DuPont plant in Luxembourg in 2009. They noticed a significant difference in the way DuPont operates compared to SIBUR.
The DuPont Production System (DPS) is an integrated system of continuous improvement and leadership practices that focuses on fully developing people and organizational capability in order to utilize assets to maximum effect and eliminate all waste. Deployment begins with a rigorous diagnostic that exposes performance improvement priorities along with opportunities for improving organizational capability and health.
DuPont Production System (DPS) Model is an integrated system to enable sustainable, synergistic and measurable results Upon hearing more about DPS, SIBUR decided to work with dss+ to design and deploy a production system for SIBUR as a means to drive plant-level performance improvement and renovate the operating culture of the company.
Setting priorities
In 2010, dss+ began conducting a series of assessments at three SIBUR sites. The purpose of the assessments was to gain a holistic view of the company and its production capability through senior management interviews, data collection and performance analysis, site visits and direct observations, as well as employee interviews. The dss+ project team was comprised of experts with significant manufacturing and business leadership experience.
The assessment results allowed the project team to identify opportunities for improvement that focused on critical business needs and priorities. For the company-level assessment, the focus was on identifying the essential factors that would make improvement and culture change possible, rather than specific solutions.
SIBUR's strategic goal to become a world-class player drove the company towards a clear set of development priorities:
- Acquiring and constructing new production facilities
- Perfecting its expertise and competencies
- Maximizing returns from its existing portfolio of assets
Assessment findings also pinpointed maintenance as an area for improvement. Although maintenance practices were in place, they were not consistent across the sites and needed substantial improvements. In many locations, maintenance was managed as a cost to be minimized, rather than a value-adding investment.
What next?
The outcomes of the assessments gave SIBUR a clear idea of what they needed to improve. The next step was to agree on "how." Together, dss+ and SIBUR developed a common view of a successful outcome for the engagement:
- A standard Production System design and deployment approach
- Cultural alignment through leadership development
- Development of a continuous improvement culture to sustain progress
- Strong performance management practices using KPIs (Key Performance Indicators) and real-time visibility
Another overarching goal was to build SIBUR's capability to deploy and sustain its own production system independently. To support this goal SIBUR and dss+ set up a Company-level Program Management Office (CPMO) that would provide resources to support site-level deployments and ensure consistency as the effort moved from location to location throughout SIBUR.
It was apparent from the beginning that the key to success lay in tailoring the production system design and deployment process to fit SIBUR's specific situation and current capabilities. In order to test the design and deployment models, site-level deployment of the SIBUR production system (PSS) began at the company's facility near the Siberian city of Tomsk in January 2011. To support the beginning of SIBUR's journey, dss+ fielded a team of consultants from all over the world, including nationals from the U.S.A., Russia, the U.K., Spain, Brazil, the Netherlands, Germany, Portugal, the UAE, Serbia and South Africa.
Long-term success also depended on SIBUR maintaining a balance between actualizing performance improvements, building organizational capability and shaping the culture and work environment.
SIBUR's CEO, Dmitry Konov describes the SIBUR productions system as,
" …not just a project with a beginning or an end. It is a permanent set of tools and a collection of best practices that are widely used by employees and are spread from one plant to another."
Dmitry Konov, SIBUR CEO
To support this, dss+ provided an Opportunity Tracking Tool (OTT) to consolidate, prioritize and monitor the progress and benefits of improvement projects in all three of these areas. Sites and the CPMO use the OTT database to ensure major improvement efforts are properly balanced and delivered as agreed. By early 2012, SIBUR had extended the use of the OTT to all its facilities, including those that had yet to deploy the production system.
Learning by doing
To further the cultural alignment and develop the necessary leadership abilities to promote SIBUR's production system, its design relies heavily on Leader Standard Work (LSW). In simple terms, LSW is the application of certain continuous improvement practices to the work of leaders and managers. LSW ensures that leaders are setting an example and demonstrating their willingness and ability to make personal changes in order to be more effective in their work. This sends a clear message to everyone that "we are all in this together".
Classroom training associated with LSW is very brief as real learning occurs as leaders practice LSW behaviours in the field with the help of a dss+ coach. LSW practices enabled SIBUR's site leaders to provide visible felt leadership by maintaining open dialogue in operating areas and offices, consistently sharing progress on KPIs, and displaying the mindsets and behaviours needed to support and enable continuous improvement.
Jim Frazier, who was a lead on the Operations Workstream at Tomsk, offers one example.
"In the Polyethylene Unit at Tomsk, for example, our coaching with area leaders helped them quickly develop an ability to engage in very effective performance dialogues. Prior to PSS ‘discussions' about KPIs and performance improvements would have centred on problems and included a good deal of dissatisfaction from the team. By shifting their focus to solutions and potential improvements, leaders learned how much their front-line teams have to offer and how willing they are to help. Within a few months, the production output in that unit was at record levels. It was a great demonstration of how visualization, performance dialogues, problem-solving, big improvement projects, small step improvements, feedback and coaching all come together to enable real performance improvement. Of course, once the team begins to have success, the culture shifts in a very visible and permanent way."
During deployment, dss+ also focused on teaching leaders at all levels how to explore and understand underlying mindsets that drive behaviours. Coaching helped managers to identify the different mindsets of employees, and subsequently, develop and support the new "continuous improvement" behaviours. dss+ strongly believes that "learning by doing" with a coach in an environment where it is acceptable to make some mistakes is the fastest and most effective way to build lasting capability. Frazier goes on to say,
"A lot of our coaching with the SIBUR people had to focus on the ‘how', but we were also very deliberate in challenging them to be clear on the ‘why' of what they were doing."
Jim Frazier, lead on the Operations Workstream at Tomsk
SIBUR's sites received strong support from the SIBUR executives, who participated in key events during site deployment. Leaders demonstrated their commitment to improving production efficiency by taking action to implement improvement ideas. Now, feedback and coaching have become standard tools for leaders to encourage effective future behaviours.
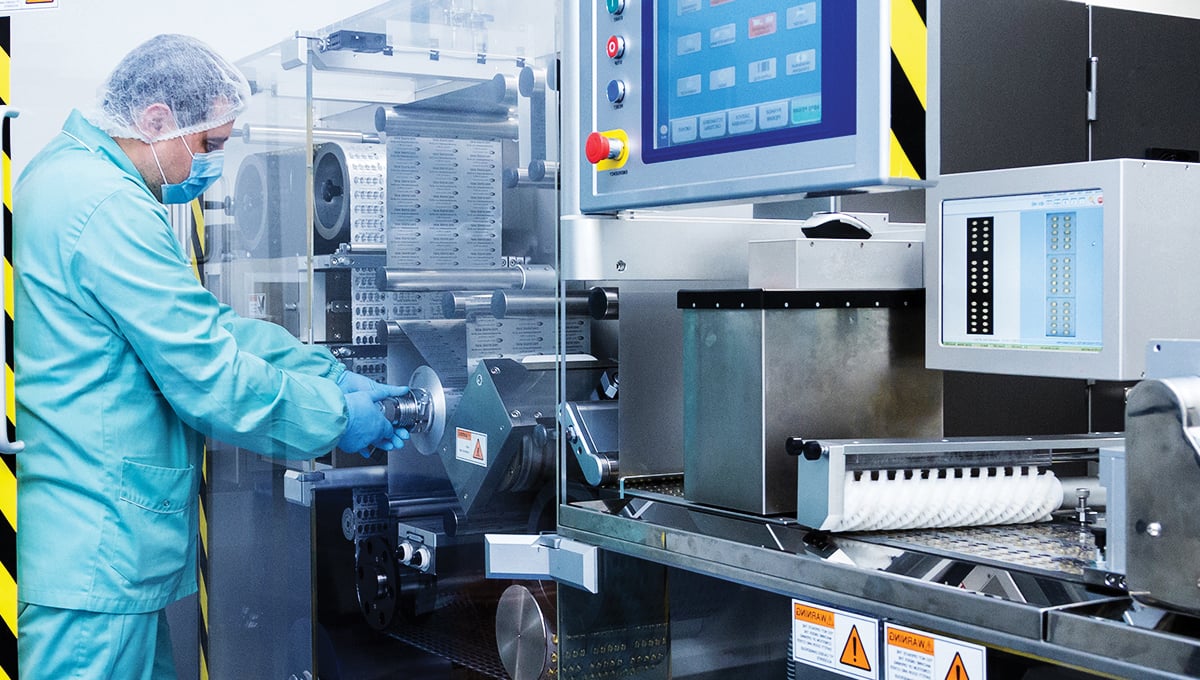
Building and sustaining momentum
For SIBUR, one measure of success was to get all levels of the organization to engage in continuous improvement as part of the daily routine. dss+ worked with SIBUR to develop a Small Step Improvement System, which would allow and encourage all employees to make suggestions and come up with ideas for improvements as part of their everyday work routine. This has resulted in employees coming forward with numerous ideas, such as suggestions for increasing production efficiency.
Vladimir Zamorin, Compression Unit Operator at SIBUR- Khimprom, has seen a big change since the introduction of the new SIBUR production system and offers this example of how small step improvements are helping:
"There were no oil traps at the compressor's run-down boxes. Oil would be spilt and leak down the floor. That presented a potential hazard and negatively affected order in our workplace. We suggested making special oil traps for the compressor's run-down boxes out of fine netting with a special handle for convenient access and maintenance. With the advent of the Small Step System, a number of issues got resolved, relating to the technology and safety of the machinery. People could realize their innovative potential and that raised the production culture in our unit."
Other ideas from the shop floor, motivated by the change in culture and attitudes, included the lowering of the water temperature in the cooling towers for a reactor at the Tobolsk polymer site. That in turn helped to reduce pump pressure and led to an increase in polyethylene production.
SIBUR has also improved the way in which it measures performance. Previously, the finance department only tracked costs and financial growth. Today, SIBUR has a more robust measurement program, which includes uptime, savings, output and cost optimization among other factors.
To ensure the effectiveness of all these changes would be long-lasting and lead to continuous improvement, dss+ also helped SIBUR set up three Centers of Competency (COC). The COCs monitor SIBUR's performance in Energy Management, Maintenance & Reliability and Process Control. They also play a key role in developing technical capability within the plants and take ownership with the PSS CPMO to help the sites develop and propagate good operating and managerial practices.
During this journey, SIBUR has also introduced Six Sigma and has appointed operational excellence champions at each site who support and advance continuous improvement as part of SIBUR's company culture.
The results
SIBUR began to see positive results from the newly introduced system within just a year. As improvements became apparent in safety, maintenance, reliability and energy, the culture of the company began to change.
After the successful implementation of the production system at Tomsk in January 2011, SIBUR rolled out the production system program at four more sites in two "waves" beginning in December 2011 and ending in September 2013.
By the end of 2013, SIBUR had made many improvements in operating performance and efficiency using PSS. Daily production at the respective sites has increased significantly and the value of improvement projects in SIBUR's Opportunity Tracking Tool has more than doubled. Through 2013, SIBUR estimates the financial benefits from PSS at twenty times its investment with dss+. Considering all the internal and external expenses, the program passed the break-even mark in 2013 with five of SIBUR's twelve large sites deployed.
Mr. Razumov believes, "The main thing is done. This project was very important. We need people with different mindsets. And this project does a lot for this."
Together with the safety improvement project, PSS has helped SIBUR reduce lost time injuries by 40 per cent and increase the reporting of minor injuries by ten-fold. Additionally, with each deployment phase, SIBUR's need for dss+ support steadily decreased so that SIBUR was able to begin its fourth "wave" in late 2013 on its own.
The positive change in the culture at SIBUR is clearly visible, from the improvement in the interaction between line management and shop floor employees to a new environment of openness and encouragement. Managers are more open to ideas. They ask their teams for input and look for solutions. Innovation and creativity are valued and rewarded. A continuous dialogue between leaders and shop floor employees helps to reinforce and sustain the cultural change.
Pavel Popov, Finance and KPI workstream leader for the SIBUR production system at the corporate level says, "Site leaders have realized the potential of the organization. Teams have become more united and functional leaders focused more on improving productivity. I myself have changed. From directing and telling people what to do, I now take a much more consensus-based approach. I listen more."
Juan del Rio, dss+ Solutions Architect believes SIBUR will continue its improvement journey.
Juan del Rio, dss+ Solutions Architect
Vasily Nomokonov, Managing Director, sums up the change the company has gone through in three short years: "We have witnessed an amazing transformation in how people treat each other and in the motivation and participation of our front-line workers. That is not an improvement one can easily put a financial figure on, but the positive effect on how we work together definitely has an impact. Output has increased and we have realized significant financial benefits. We are definitely narrowing the competitive gap we set out to close and in the process, are gaining incredible momentum with our people."