Safety as a Building Block for Success
Ask Rain Carbon Inc., global carbon-based raw materials company, about its investments to achieve safety excellence, and you are likely to get an answer like the one given by Massimiliano Martino, Rain Carbon’s Vice President Global Safety, Health and Environment: "To be successful, Rain Carbon has to be a world-class performer in safety. We cannot compromise when it comes to safety and to move forward, we can only go as fast as our progress in our safety programs and activities. Our Total Recordable Injury Rate is currently below 0.4, which is a great achievement, but we can only be satisfied with zero incidents. For that, we have put in place stringent programs and KPIs (key performance indicators) to monitor and reduce all types of incidents. We need to do our best to safeguard communities, employees and the environment to be able to deliver on our commitments as a responsible company. Safety is one of our building blocks for success, and it will allow us to increase our productivity, operational discipline and add value to reach a true organic growth."
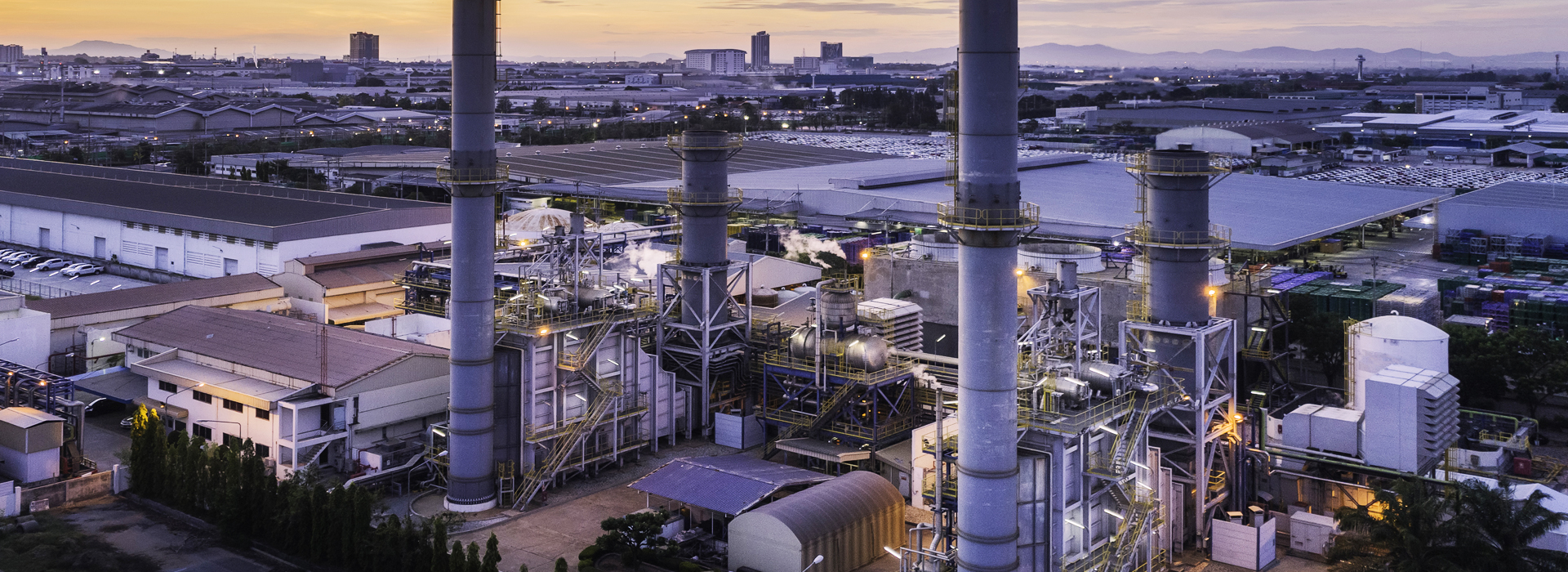
A transformation in safety culture at Rain Carbon starting in Germany
Under the direction of Dr. Günther Weymans, Executive Vice President Carbon Distillation, and Advanced Materials, Rain Carbon determined in 2016 that its facilities around the world needed to build a more mature and sustainable safety culture. The company sought assistance from a safety and operations management consultancy with significant experience in the chemical industry: dss+. This article describes the beginning of Rain Carbon’s journey to becoming an incident-free organization.
Rain Carbon began the cultural transformation project at its largest site, the distillation and advanced materials production facility in Castrop-Rauxel, Germany. Here, the Total Recordable Incident Rate had been caught in a cycle where the number of incidents would gradually decrease, creep up again, then decline once more without ever completely flattening out. "It was clear from the beginning that Rain Carbon was looking for a partner who is competent in dealing with and understanding what is needed for the chemical industry. This is what they found with dss+. All of our colleagues are experienced, knowledgeable, and motivated to share their expertise." says Holger Grimm, dss+ Project Manager at that time.
"It became more and more obvious that our culture did not promote independent safe decision-making," recalls then-Site Manager Elke Helck, who now is Rain Carbon’s Vice President of Calcining Operations. "Instead of deciding on a risk-free course of action for themselves, employees relied on rules and regulations to keep safe. Management and employees had widely diverging views of safety. It was clear something had to change, but what?"
Taking ownership An initial assessment of the status quo at the plant by dss+ confirmed what Rain Carbon had suspected. The prevailing safety culture was highly dependent on discipline, controls and monitoring to prevent incidents, whereas Rain Carbon needed its entire workforce and management to have a more independent mindset if it wanted to achieve a sustainable change in safety performance. Only personal engagement, increased accountability for each employee’s area of responsibility and a change in attitude toward one’s own safety would move the plant-forward and closer to its goal of zero accidents.
"What we didn’t realise," Helck admits, "is that you don’t just buy a consulting service and they do everything for you. You have to do things yourself and change."
"It was incredibly helpful to walk across the site with a dss+ consultant to help us spot unsafe activities and learn how to address them in a positive way. The dss+ consultant would ask really simple questions."
ELKE HELCK, FORMER SITE MANAGER AT RAIN CARBON’S CASTROP-RAUXEL PLANT.
That was quite a hard lesson to learn. But we would never have managed it on our own. We learned that managers have to leave their offices and go out into the production halls where the biggest risks are. It was incredibly helpful to walk across the site with a dss+ consultant to help us spot unsafe activities and learn how to address them in a positive way. The dss+ consultant would ask really simple questions.
"Initially, employees would react by saying 'I have to check if there is a rule for that,'" Helck continues. “dss+ gently nudged them to start thinking for themselves. This approach allowed us to 'reclaim' our plant. At first, employees were rather perplexed and skeptical. They naturally want to produce more, to be proud of what they achieved, and receive praise. It took time for them to understand that we were not checking up on them and that we mean it when we say 'Safety First'. We've had so many safety campaigns in the past that employees were a bit weary and wary of them. But we've sent strong signals that we’re serious about safety – such as stopping production for safety reasons and investing in training – and I continue to push managers out into the plant, as that is the only way to get everyone involved in safety."
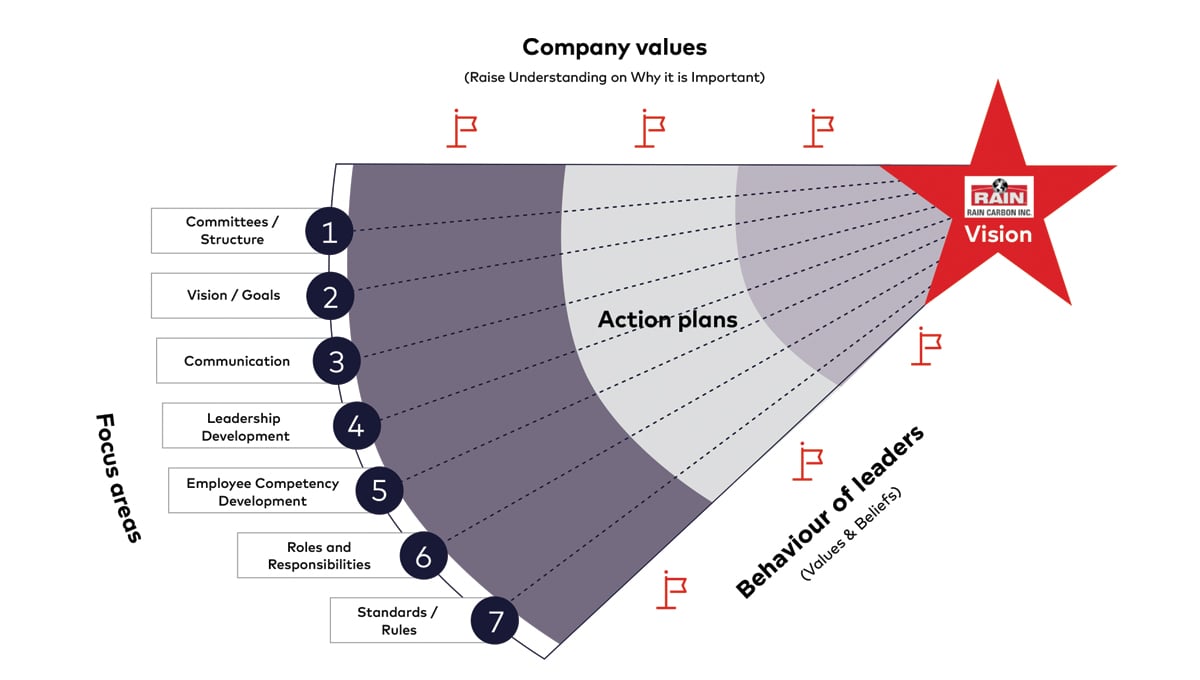
Structural changes
In addition to the initial assessment, which included a survey of employees'perception of safety and help with safety observation training (STOP™), Rain Carbon along with dss+ developed a two-year implementation plan with prioritised short- and medium-term goals and identified a number of quick wins. Planning the transformation of the site culture took place in a joint strategy workshop that analysed such issues as what had to change and when who had to change and how and a clear delineation of responsibilities. This led to an action plan developed collaboratively by Rain Carbon and dss+, which considered the site's starting point and ultimate objective. dss+ helped Rain Carbon to determine the necessary actions to move the site from one to the other and ensure the company had a realistic view of the plant's readiness for change. To enable the implementation of the action plan, a safety steering committee and a support structure were established. dss+ furthermore assisted with coaching for senior management and workshops to develop management and employee capabilities.
Insights
Management at the site has noticed a great change since work with dss+ began in 2016. Thomas Tulkens, former Global Safety Manager at Rain Carbon, says that lagging indicators and housekeeping have improved, and levels of engagement and involvement in safety are higher, as is visible management commitment. "The culture is much more open, and people are more willing to discuss behaviour," he says. "That wasn't the case three years ago."Carsten Grabosch has been Site Manager in CastropRauxel only since May 2018, but he too has seen a difference in behaviour. "I wear glasses. If I forget to change my normal glasses for safety glasses, someone will mention that to me. That's a noticeable change in safety attitudes." he says. "We've still got a long way to go, though, and are not yet where we want to be. But we have definitely made some progress."
Change has not only affected production at the CastropRauxel site; the impact can be seen in the administrative offices, as well. Recently retired Vice President of Corporate Accounting & Tax Thomas Müchler says he initially didn't understand what safety had to do with administration. Nor did many of the 80-90 employees who took part in the workshop for administrative staff. But after the workshop, he got only positive feedback. "We have come to realise that safety has many different aspects, and I think we've all become far more proactive," he says. He cites initiatives that employees in his department have organised, such as safety training for drivers of company cars and activities to improve safety on the way to work.
Yet, changes at the management level have sometimes been slow to reach the shop floor. Employee Representative and member of the Works Council Jeannine Bittner says, "Many of the employees in Castrop-Rauxel stay with the company from apprenticeship through to retirement. It's difficult for them to understand why they should suddenly do something differently. Communication is really important to explain why that is necessary. The plant walk-throughs help, but we still need more and better communication. The site has made a good start on this project, and we do believe the changes will last. But safety officers need to be integrated more, so there is still room for improvement."
Martino, Rain Carbon's Vice President of Global SHE, is clear-eyed about this issue. "We come from a top-down culture. Our mindset is still conservative, but we are introducing digitalisation and steering committees to communicate, think and act quicker in all aspects of safety. We need agility because timing is critical with 24/7 operations across different continents and time zones. I am very ambitious and want faster and bigger changes for the success of the company, but if we shake people up too much, they vibrate. Since we started working with dss+, changes have been positive and progress has been fast. Perhaps even more important, the impact is sustainable at all levels of the organisation, and that is a true added value. With dss+, our safety culture has improved to become more active. However, we are not yet proactive enough. I believe that we need to continue accelerating with maximum energy to create the highest momentum possible to achieve excellence in safety. We will then see a reduction of all incidents globally with stronger organic growth for Rain Carbon."
"The culture is much more open, and people are more willing to discuss behaviour. That wasn’t the case three years ago."
THOMAS TULKENS, FORMER GLOBAL SAFETY MANAGER AT RAIN CARBON
Conclusion
That is a clear signal to Rain Carbon senior management that change is here to stay. Today, leadership at the Castrop- Rauxel site not only tracks safety performance in a different way than before with a wider range of KPIs; it also shares what is happening at the German plant with employees at other Rain Carbon production facilities and offices around the world so they too can benefit from the lessons learned during the Castrop-Rauxel pilot project. What was originally a theoretical push concept has taken on a new dynamic. As Rain Carbon President Gerry Sweeney puts it, "I look forward to the day when every Rain Carbon employee believes that 'zero incidents' is a choice rather than a dream, and when everyone follows safety rules not because they have to, but because they want to. By working together as One Rain Carbon to change our safety culture, that day is inevitable."
"I look forward to the day when every employee follows safety rules not because they have to, but because they want to. By working together as One Rain Carbon to change our safety culture, that day is inevitable."
GERRY SWEENEY, RAIN CARBON PRESIDENT