Risk Reduction
dss+ partnered with a top 5 global petrochemical company on a global transformation at corporate and subsidiary levels to drive risk reduction, sustainable performance improvement, and ensure safe and reliable production across its business portfolio.
In part 1, dss+ summarised the experience from this global transformation project aimed at ensuring that the client was focused on the right priorities and risks at the corporate and subsidiary company asset/site level.
In part 2, dss+ focused on driving a transformation at the subsidiary company site/plant level, by risk reduction, strengthening safety culture, and embedding a sustainable operating rhythm. Sustainable risk reduction and operational performance improvement are two sides of the same coin.
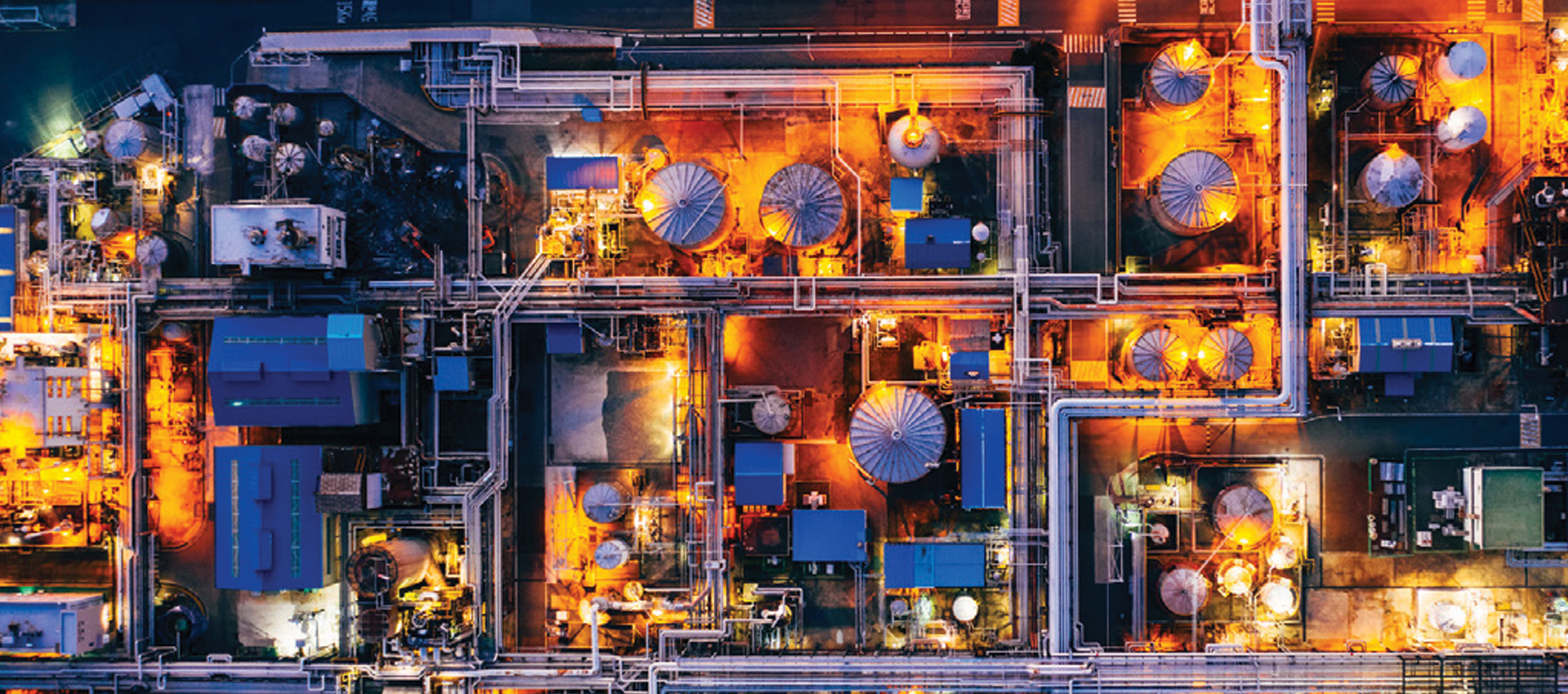
Driving Transformation & Sustainable Performance Improvement at a Leading Top 5 Global Petrochemicals Company
During the Global HSE Transformation project, dss+ had identified top technical operational and cultural risks at one of its key subsidiary companies. To help the client improve operational risk management, performance, and strengthen safety culture, dss+ applied a top-down and bottom-up approach where a specific plant was selected as a pilot for an area transformation. Based on dss+ experience, driving change top-down alone is not sustainable. A structured top-down and bottom up approach is effective to reduce risks and improve performance in a sustainable way.
In the past the client had several experiences at driving culture change and performance improvement, including initiatives, training programs, communication campaigns and observation and intervention programs. While the client had improved safety performance and strengthened systems and capabilities over time, they recognized that they required a different frame of thinking to reach the next performance levels and maturity milestones.
- How to drive sustainable culture and performance improvement?
- What is the desired end state and culture given risk profile and maturity?
- While safety culture improvement is often thought of as a long-term program, are there opportunities to accelerate improvement?
- How to demonstrate value and what are the measures for success?
- How to measure impact and improvements?
- How to promote better teamwork across operations, maintenance and engineering functions?
- How to ensure leadership commitment to demonstrate the desired behaviours amidst a high degree of internal initiatives?
- How to effectively scale up safety culture improvement across the rest of the company to drive performance improvement?
- How to build the right visibility of the top risks in day to day operations?
- How to derive insights from data to enable better riskbased decisions that reduce the risk profile and improve operational performance?
- How to sustain safety culture improvements, moving beyond a program?
- How to ensure sustainability amidst a high degree or organizational change?
- What is the right governance and managing process to drive and embed sustainable results?
A culture transformation and operational performance improvement program is a "marathon" and not a "sprint" and needs to be resilient during organisational changes. Transformation approach and pace of change need to take into account risks, maturity of the organisation, capabilities, and constraints. dss+ designed the project around two dimensions to support the client towards safe and reliable production in a sustainable way. The first was guiding leadership through a structured coaching program to demonstrate changes in mindset, behaviours and actions (top-down). The second was designing and implementing Area Transformation at plant level, working with the frontline to accelerate risk reduction and transformation by embedding a sustainable continual improvement approach and mindset (bottom-up). dss+ adopted a pilot "lighthouse" approach to deliver a proof of concept to inspire change and build internally capabilities to drive sustainable change. Throughout the project, an integrated and structured change management approach was adopted.
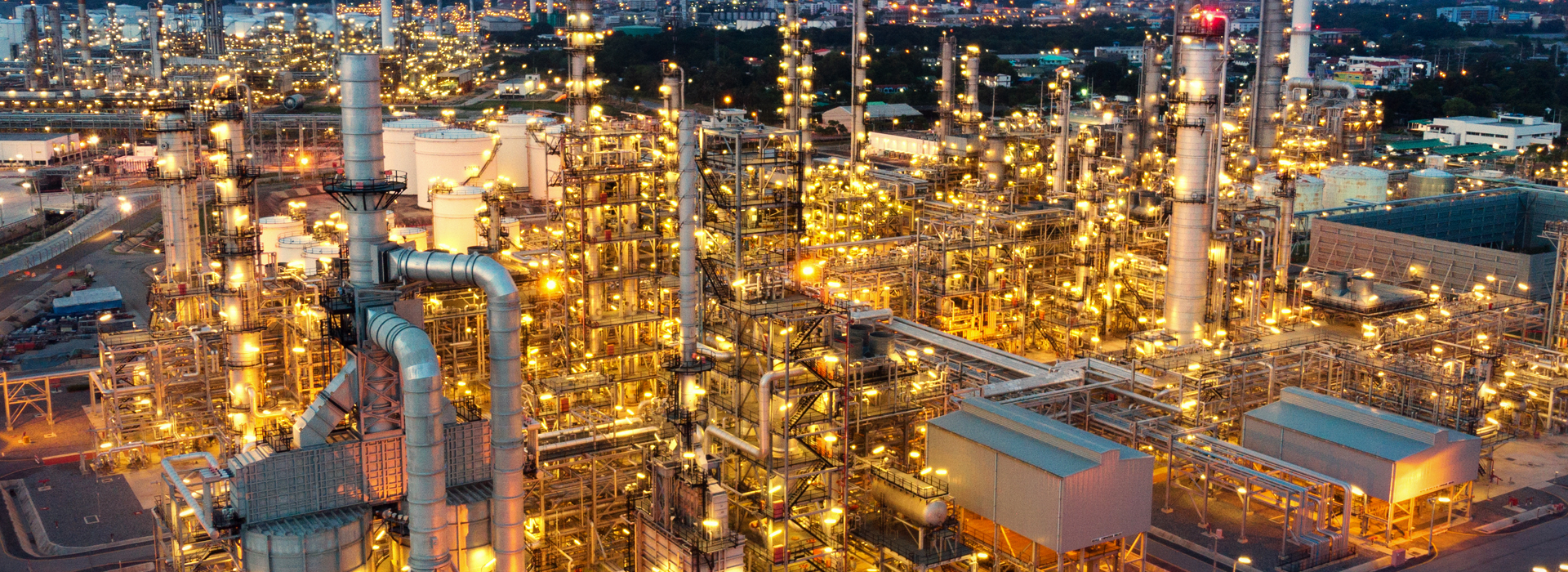
Getting a culture transformation right starts at the top with leadership. Also, an effective governance is required to reduce risks and improve operational performance. dss+ used the proven Visible Felt Leadership program to align client leadership on the case for change and new behaviour's they would need to visibly demonstrate to support a step change in safety culture. Visible Felt Leadership is shifting from leader as a "boss" to leading as a "role model" and "coach" to develop capabilities and drive new mindsets and behaviours. Through a collaborative executive workshop, the leadership was aligned on the Visible Felt Leadership methodology and discussed the following questions:
- What are the top risks and potential blind spots?
- Are these risks indicating common themes?
- What are the top concerns as a leadership team? Do we have a aligned view of reality with our operations teams?
- How did the leadership team enable these risks through actions and inactions?
The risks helped leadership open their eyes to behaviour's that may have contributed to increased risks in the field. dss+ worked jointly with the leadership team to align on a Commitment to Change that they would later share and engage the organization with. Personal action plans were developed and through individual coaching sessions dss+ developed the capabilities of the leadership and guided them to build, embed, and demonstrate changes in their mindset, behaviour's and actions.
Improving Operations & Maintenance Performance Through Area Transformation
Focus on Front Line is critical to translate vision and expectations into day-to- day actions and behaviours across the organization. This requires building critical organizational capabilities and operational discipline at the frontline. Empowerment of front line to address everyday risks enables development of problem-solving skills. Management Operating System routines and aligned individual Leader Standard Work discipline embed habits into operating rhythm. Visual management and performance dialogues at front line support effective day-to-day risk-based decision-making and focus on risk. Developing tangible indicators to measures impact and success are key to ensuring sustainability of improvement efforts.
To drive safety area transformation in operations and maintenance, dss+ focused on risk containment, operating rhythm and mindsets and behaviours. Following the area diagnostic, dss+ also aligned the local plant management team on the case for change. dss+ worked closely with the leadership team to align on measures of success versus the baseline.
dss+ worked jointly across functions and level to adopt new practices and build internal capabilities. To drive sustainability, dss+ trained and coached change practitioners and embedded effective governance tools to monitor performance going forward.
Driving Improved Risk Discovery & Quality Through Risk Containment
The diagnostic helped the team identify the operations plant's top risks. To promote teamwork across functions and accelerate risk mitigation, dss+ formed multidisciplinary risk teams with structured charters and action plans. dss+ also developed capabilities at the frontline to enable improved risk discovery, strengthening communication and embedding new practices in client systems and operating rhythm to identify and mitigate risks and improve operational performance.
Embedding a New Sustainable Operating Rhythm in Operations & Maintenance
dss+ focused on enhancing the operating rhythm to facilitate safe and reliable production in the plant. This was done by integrating risks and key performance metrics into the operating rhythm at a daily, weekly and monthly level, improving the collaboration between operations and maintenance and improving the interface between the plant and support departments. dss+ leveraged strong visual management practices to bring visibility to risks and strengthened meeting efficiency and effectiveness across over 10 key daily and weekly meetings, with a focus on action closure, prioritization and ownership. Most importantly a mindset to "welcome the reds, and challenge the greens" was embedded.
Shifting Mindsets and Behaviours at the Frontline in Operations & Maintenance
dss+ together with the client focused on improving mindsets and behaviours to drive change and sustain performance at the frontline level. The diagnostic revealed a conditional commitment to safety, a lack of accountability and motivation, normalization of deviations, and a lack of trust, among others. By training and coaching the line management, supervisors, engineers, operators and technicians, dss+ reinforced key expectations required for their roles. dss+ adopted Leader Standard Work to help turn new behaviours and practices into habits, focusing on skills such as line walks, delegation, prioritization, coaching and difficult conversations.
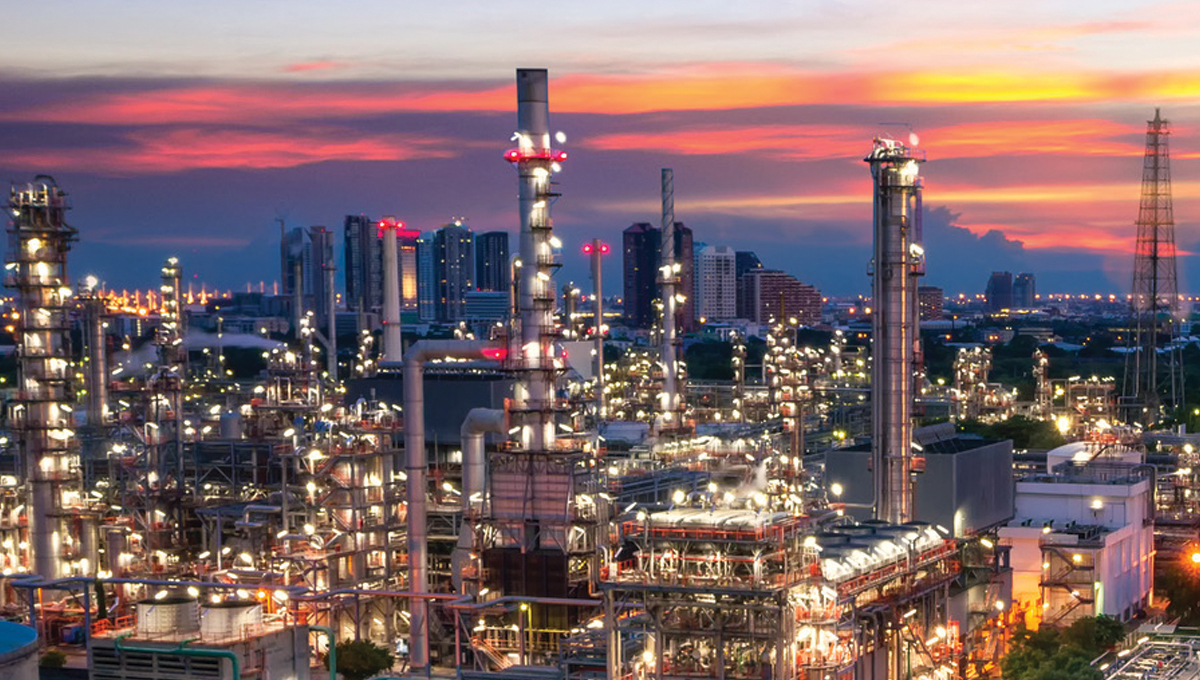
Key Outcomes, Value Delivered & Impact
dss+ delivered significant value and improvements versus the baseline against the measures of success. Quantitative and qualitative feedback, especially the leadership and front line, highlighted strong areas of improvement:
- Visible felt leadership and engagement.
- Transparency (welcome the reds, challenge the greens) and Visual Management.
- Efficient operating rhythm to support safe and reliable production, with HSE effectively integrated in all interactions.
- Increased collaboration and improvements in the interface between operations, maintenance, and support functions.
- Leadership lead by example. Leader Standard Work skills became a part of the routine.
- Improved operational performance along key performance metrics.
- Promoted quality risk discovery – shift from chasing numbers towards promoting risk discovery through improved visibility in the field, teamwork and ensuring a sense of unease and respect for hazards.
- Significant progress made towards the containment of immediate top risks.