Mercer International
Large corporations can be big beasts to turn around. Even more so when they include operations in different countries and employees in remote locations. Yet Mercer International, a global forest products company and one of the world’s largest pulp producers, managed to transform its safety culture with the Road to Zero initiative, developed in collaboration with dss+.
With operations in Germany, Canada, and Australia, Mercer’s more than 2,300 employees not only manufacture pulp and timber products, but also produce biomass-based green energy and bio-chemicals. Following its acquisition of Germany’s largest sawmill in 2017, the business is also active in the softwood lumber sector.
Apart from the typical work safety issues such as slips, trips and falls, the industry has to manage its own particular set of risks. Logging, massive weights, sawmill machinery, and mechanical equipment make crushing hazards and laceration injuries very real threats. Chemicals, confined spaces and work at heights present further hazards.
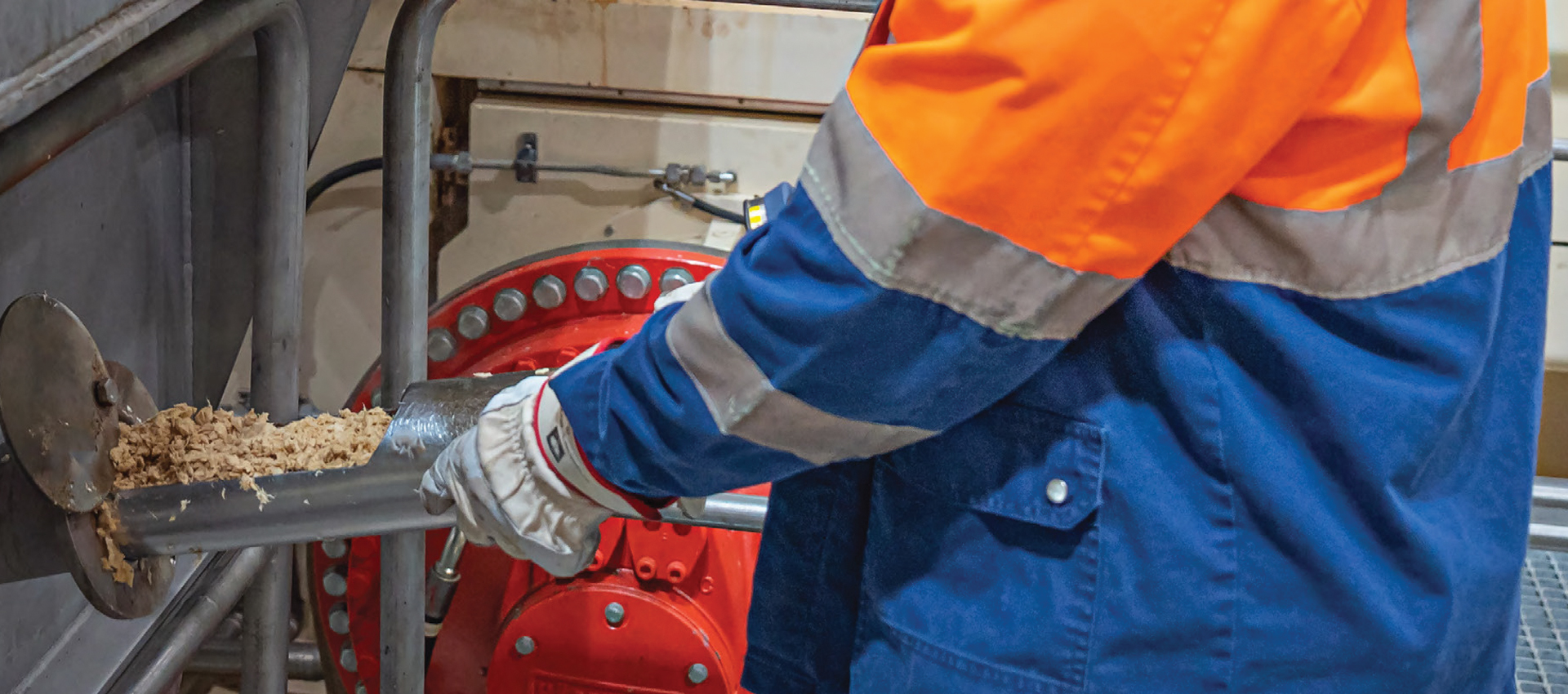
Developing momentum in safety
Why did Mercer choose dss+?
For years, Mercer put a lot of effort into work safety but could not achieve the results it wanted. "We benchmarked our performance in 2015 and weren't where we wanted to be," Mercer President and CEO David Gandossi says. "We began talking to peers and realized many had gotten where they were with external help."Mercer chose one of the top global safety and operations management consultancies, dss+, to help three of its sites in Germany and Canada break through the stubborn safety performance ceiling. "We liked the people we met, the flexibility dss+ demonstrated, and the fact that the programs they developed were additive to existing processes," Mr. Gandossi says.
dss+ were the eyes and ears throughout our organization. They had seen it all before and helped us narrow the experience gap very quickly.
DAVID GANDOSSI, PRESIDENT AND CEO, MERCER
The Mercer experience
After field assessments and an employee survey about safety perception, dss+ convened Mercer top management for a two-day meeting. At this gathering, business leaders and dss+ worked out the bones of a framework for what later became the Road to Zero initiative.
With 2016 came the roll-out of the Mercer Rosenthal pulp mill and Mercer Stendal pulp plant in Germany, and the Mercer Celgar mill in British Columbia. It had been preceded by a lot of behind-the-scenes work with dss+ on the establishment of a governance team, the setting of KPIs, the creation of local Health & Safety Committees, training for all managers and supervisors, and the development of safety standards.
"dss+ were the eyes and ears throughout our organization. They had seen it all before and helped us narrow the experience gap very quickly. We had personal dss+ coaches who helped us understand what we needed to achieve, and we had training on safety walks and how to talk to people about safety," Mr. Gandossi recalls. "It was like going from kindergarten to grade 12 in the space of a few weeks. I realized, I had to be the enabler for safety, to become like a safety manager when I visit a site. All that has made me a better leader."
Workers at the sites noticed a quite remarkable change. At Mercer Celgar, safety and union politics had often been mixed. Jim Johnston, a union rep who has worked in the mill stores for 26 years, has seen many safety initiatives in his time but the general feeling was always that things wouldn't really change. "There was little trust between union members and management, and you just can't be good in safety without trust, integrity and honesty," Mr. Johnston says. He believes that is one reason why incident rates were high. "People in a safety role were not recognized or valued." The Road to Zero initiative genuinely altered that. "The culture change has been quite enormous. I asked to be released two days a week to concentrate on safety. That was agreed and I am now included in decision-making, strategy sessions, safety budgeting and planning," he explains. "We have almost eliminated the mixing of safety with politics."
Chris Wald, the Day Lead in Operations, Pulp Finishing at Mercer Peace River, has had a similar experience, "Before, it was a tough thing to stop production to talk about safety. Now, we feel we have the backup. That's the big difference."
It was like going from kindergarten to grade 12 in the space of a few weeks. I realized, I had to be the enabler for safety, to become like a safety manager when I visit a site. All that has made me a better leader.
DAVID GANDOSSI, PRESIDENT AND CEO, MERCER
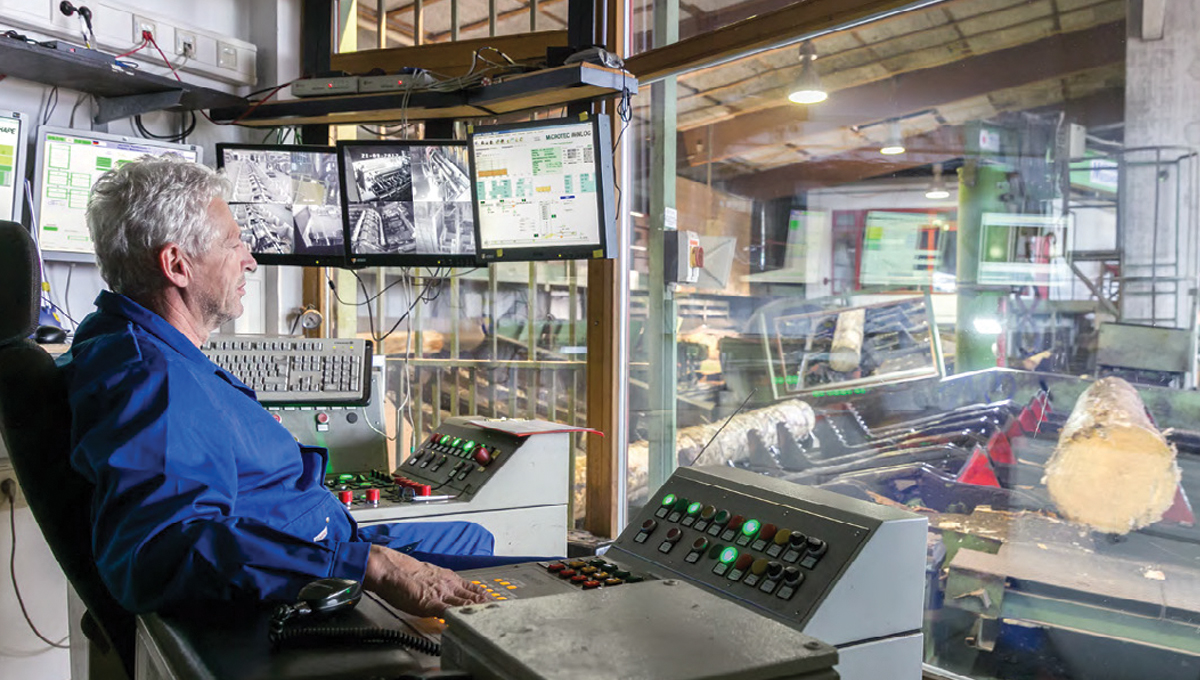
What Mercer learned
The shift in attitudes is partly due to the emphasis dss+ places on visible management commitment. An outward sign of that are the new Safety Day visits by Mercer management and workforce delegates to the different sites. On one such visit to Celgar, David Gandossi was asked about a long-festering problem with lime and wood dust outside a heavy-duty mechanics garage that had repeatedly been reported as a safety concern in addition to other safety deficiencies in the building itself, e.g. inadequate lifting devices, battery storage area and poor ventilation of exhaust fumes. Then and there, the CEO approved the budget to fix the issue. This demonstration of leadership backing for safety reverberated through the site. Another indication of management support for safety was the time invested. The local health and safety committee, safety captains, first aid attendants and shift safety coordinators now number 47 people.
dss+ is also very clear on the need to communicate roles and responsibilities within the organization and to engage people in safety in a positive way. Mark Goebel, corporate Health and Safety Director at Mercer, was instrumental in implementing the Road to Zero initiative at Celgar where he was HSE manager at the time. "We used to have a culture of blame and were very compliance driven. Morale was poor. Safety discussions tended to be argumentative. People controlled safety in the way they thought best and didn't trust supervision. They were very skeptical of the new Road to Zero initiative," he explains. "By including every workgroup in the development of safety standards, by empowering the safety committee and safety captains to support it, and by setting up a regular cadence of safety visits and safety talks, we have not only improved our 20% positive safety culture at the site in 2016 to a 70% positive one, but we have also built a relationship of trust. Today, Mercer Celgar is recognized in the British Columbia pulp and paper industry as leading in safety." Heightened risk perception and awareness is another key component of an effective safety culture according to dss+ and a tenet they have passed on to Mercer. As Mark Goebel says, "In the past, workers wanted to eliminate every hazard. That is not possible, but you can control the risk. That has been a huge cultural shift for us at Mercer. There is a much clearer understanding of roles and responsibilities. Now, when people report a problem, most often they propose a solution with it."
This transformation was replicated at other sites in the Mercer group. First at Stendal and Rosenthal in Germany, but later also at the corporate head office in Vancouver. As Mercer has gone on to acquire more mills, logging operations, and a sandalwood plantation in Australia, the Road to Zero initiative has also been extended to them. Each location brings new challenges, from lone workers out in the forest to large numbers of contractors, but the initiative is flexible enough to adapt to them all.
dss+ was not the first consulting company to try to change our culture, but the deeply designed, multi-layered approach has made sure that this is a long-term change.</em,/span>
BERND SCHÜTTE, STENDAL MILL
What has changed?
Bernd Schütte, who works at the Stendal mill in Germany, became involved in the Road to Zero initiative at the end of 2016 as the link between management and the shop floor. "The program required a fundamental change in the way we analyze root causes of incidents, look at sources for occupational illness, deal with high-risk large equipment, and more. There was a huge mountain of things to implement that we expected to have dumped on us on top of our normal workload. At the time, we thought we'd never manage it, but the dss+ consultant gently but firmly insisted. The way he introduced the changes was very structured and well executed. That meant we saw not just an increase in incident reporting, but the quality of reporting was better. dss+ was not the first consulting company to try to change our culture, but the deeply designed, multi-layered approach has made sure that this is a long-term change. The results we now see are due to the work we put in between 2016 and 2018. The changes have become self-perpetuating." Schütte is now responsible for contractor management in Stendal. "We have lots of different contractors on site, some for longer, some for specific projects. When the Stendal site carried out general maintenance and repairs recently over a period of 8-10 days, there were 1,000 additional contractors of many different nationalities on site. While they may know the risks associated with their everyday tasks such as construction or maintenance, they are not familiar with the risks at Mercer. We must manage that and, on top of that, control the spread of the coronavirus. The measures and systems we had introduced as part of the Road to Zero initiative, helped us with that, as well."
Mercer has introduced weekly reporting on HSE performance and there is a monthly senior safety leadership committee meeting that discusses reports from all sites on milestones achieved, objectives, completion of actions, etc. Mark Goebel, who has 30 years' experience working in HSE in pulp and paper, but also mining, adds: "I have never worked in an environment before where senior leaders – the CEO, COO, Corporate HSE director – take 1.5 hours every month to talk only about safety. That's immensely powerful."
Today, Mercer Celgar is recognized in the British Columbia pulp and paper industry as leading in safety.
MARK GOEBEL, CORPORATE HEALTH AND SAFETY DIRECTOR AT MERCER
Over time, safety has become Mercer's number 1 value. Production is still a priority, but only if it is safe production. Even COVID has not led to a let up in safety management efforts. The target is still zero. Visit a Mercer site today and the signs are all there. Good signage, good housekeeping, good PPE, but best of all, as Mercer President and CEO David Gandossi says, "very engaged people. For me, that is the most exciting thing to see: that people have benefited personally." He admits Mercer has not yet reached its goal. "We will never be finished with our safety efforts," he says, "but we are moving in the right direction towards a more effective, independent, and interdependent safety culture."