Successfully Restart Operations Following the Crisis
As COVID-19 infection rates around the globe begin to slowly decline, leaders of many nations have begun discussing how and when to relax public safety social distancing efforts and allow businesses not already deemed essential to restart operations. With attention beginning to transition from response to recovery, only those organisations with well-thought-out plans to get their operations up and running again will be able to get ahead of the curve and gain a competitive advantage.
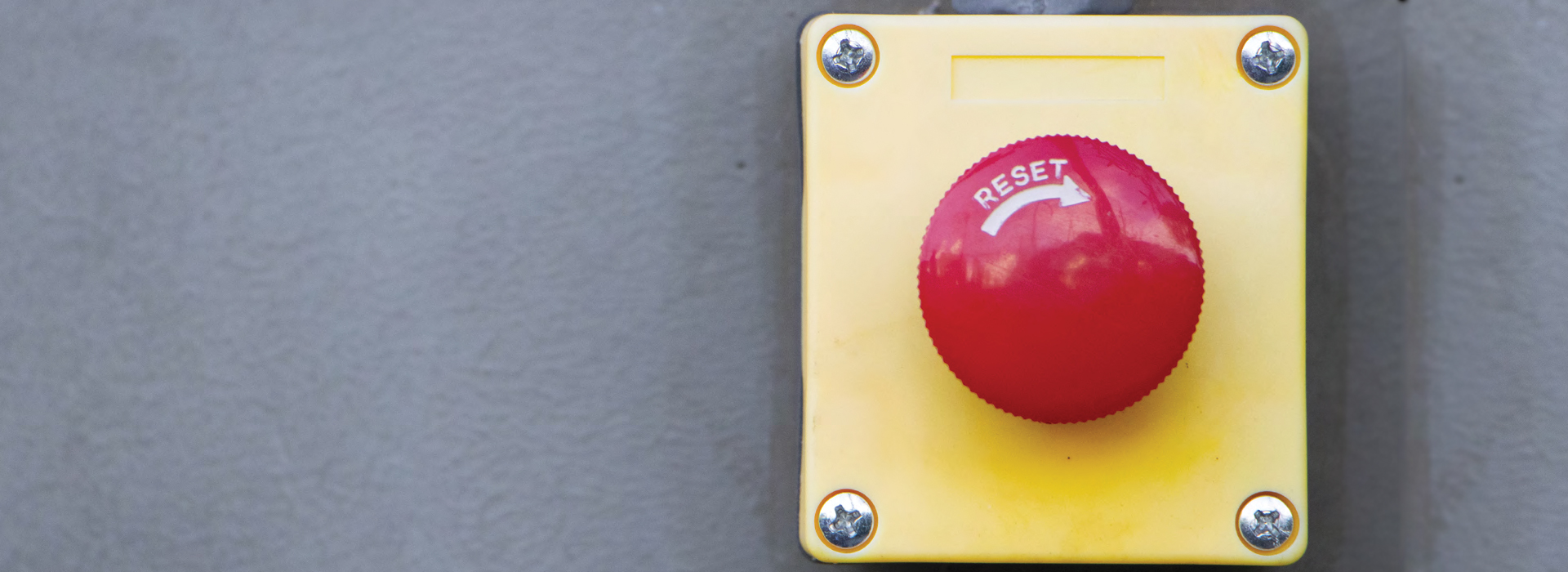
Successfully restarting operations following the COVID-19 crisis
In previous issues of our COVID-19 Response and Recovery Series, dss+ discussed seven key recommendations for business leaders as they start to plan their response during the pandemic, and shared learnings and best practices related to successful business continuity efforts implemented during past crises. In this edition, we discuss important considerations for business leaders and steps they should take to successfully and safely restart operations. Without proper planning (and the regular evaluation of the resulting plan), a restart can actually pull organisational performance backwards. Through the implementation of a thoughtful, rational process, however, companies can successfully restart and ramp up operations while protecting employees.
Another significant and unpredictable challenge to consider is the potential for subsequent COVID-19 infection waves and how governments will respond to them. Preliminary data from China and other Asian countries indicates that subsequent waves of infection is a real possibility. In fact, infection is expected to continue until a vaccine becomes available. The same phenomenon was observed during the Spanish Flu Pandemic in 1918.
Clearly, there is much to take into account to ensure that restarting operations occurs as successfully as possible. While companies may understand the importance of these considerations, the complexity of developing an effective restart plan may nevertheless be overwhelming. Failing to do the necessary planning, however, can lead to a restart that negatively impacts the long-term performance of a company.
Understand Your Current Readiness for a Restart
Before restarting, it’s critical to understand how the pandemic has affected your organisation and assess your organisation’s readiness to return to work. Remember that the inherent risks in your organisation have not disappeared just because of the pandemic. Therefore, when assessing your risk, do not just focus on those that have been brought about by COVID-19, but rather look at all risks your company faces.
Company leaders should have a clear understanding of the implications of the following: employees returning to work, changes to status of equipment and facilities, availability of financial resources, new government regulations stemming from the COVID-19 pandemic, and any changes with suppliers, customers or distribution capabilities, to name just a few. But be mindful of confidence that is unsubstantiated; that is, answers that are based on ‘feeling’ rather than ‘facts’. The emotional desire to recover quickly needs to be supported by the tangible evidence that suggests the organisation is indeed ready for a restart.
Examples of tangible evidence to ensure successful restart include things such as an integrated restart plan that considers all critical activities, alternate plans based on credible scenarios, a crossdepartmental plan for safe return to work, a restart budget and resourcing plan that includes training and backup, validation of customer demands, and the readiness of your supply chain to support a restart. If there is significant tangible evidence, there is a higher likelihood that a company can restart successfully.
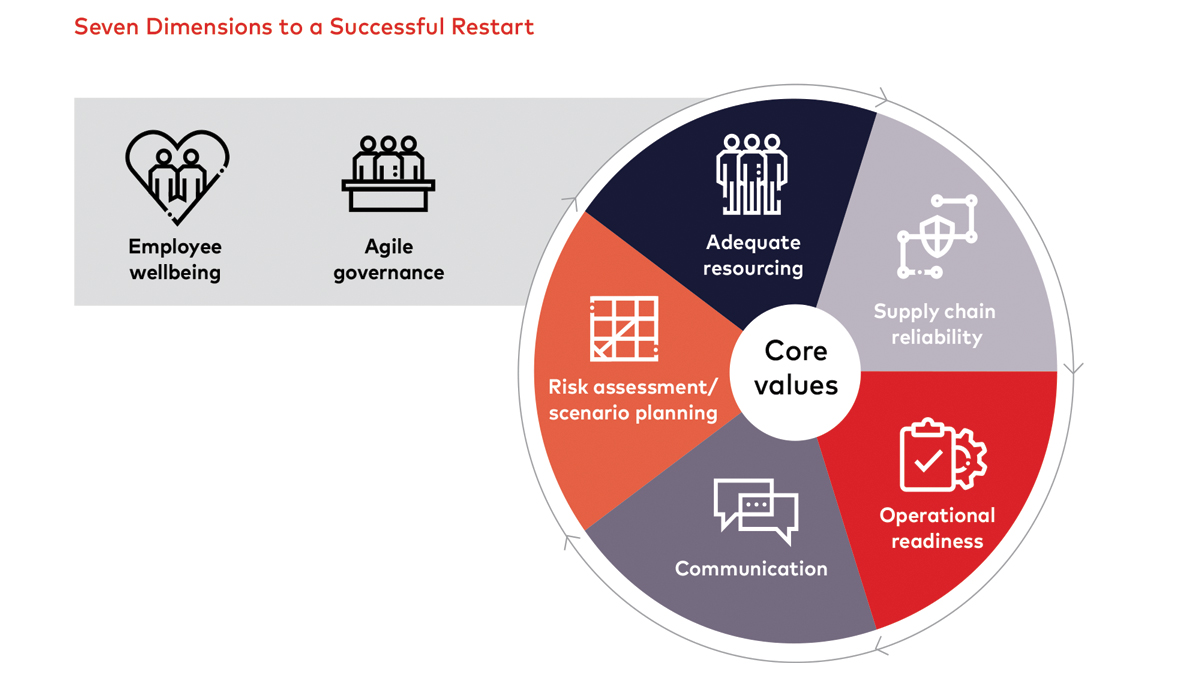
At a minimum, companies can feel confident of their ability to successfully restart by following a pragmatic, rational process that addresses seven dimensions of their current and future business situation. This process allows for an adaptive approach in an ambiguous and potentially dynamic situation, such as one that we are currently facing with COVID-19.
-
Ensure employee well-being: To say that employees are your most important asset during this time is an understatement. They will be concerned about how COVID-19 will change their working environment when they return to their jobs. Many employees will understandably be distracted by ongoing news and developments related to the pandemic. Some will even be personally affected or had family and friends who have suffered the effects of the virus. It will be important to take steps that ensure employees are in the right mindset. Show sensitivity and take steps to address their concerns. Provide them with the necessary tools to enable them to work safely and confidently, and establish a work environment that is supportive and caring. Don't be reluctant to adjust existing policies if necessary. And be sure to check in often with all employees to proactively seek their thoughts and input.
-
Design an agile governance system A working group of company executives and senior leaders that represents all functions across the organisation and is dedicated to the various elements associated with restarting the company is an ideal way to effectively manage the process. Such an Executive Recovery Committee (ERC) can identify business-critical processes, appropriately prioritize restart activities and efficiently make required decisions. The ERC should consider situational constraints, business and operational goals, and input from all risk assessments and scenario planning. It should also ensure that necessary resources (manpower, financial, etc.) are made available and establish performance measures to keep initiatives on track for a successful restart. Finally, it is important to remember that the ERC's responsibilities will not end as soon as restart occurs. It will be vital that the ERC review the progress of the restart and adjust any plans as necessary to ensure its long-term success.
-
Conduct risk assessment and scenario planning Assessing the current situation of the organisation in the midst of the COVID-19 pandemic and considering various credible scenarios that could impact the company are critical to effective restart planning. Again, remember that the inherent risks faced by your organisation still exist. A thorough risk assessment should consider those risks as well as additional risks that have been brought about by COVID-19. Critical before restarting is understanding changes and risks to your customers’ buying habits. Are they still buying in the same quantities and through the same channels as before? How will they react if another pandemic wave returns? It is important to understand these risks to realistically set production targets, build agility for rapid changes in the marketplace and ramp up production in a sustainable way. These and numerous other likely scenarios need to be considered. No stone should be left unturned.
-
Ensure adequate resourcing Human resources could be significantly strained during this time. For example, many companies in the electric utilities industry rely on contractors for remote line maintenance. But today there is a shortage of available line workers among leading contractors, forcing many utility companies to engage a different set of contractors with different levels of training.
It is important that companies determine the critical steps necessary for business recovery and provide at least the minimum amount of resources required to meet these critical needs. Companies should also fully understand the competencies required for needed personnel. As highlighted by the example above, companies should have a firm grasp of the availability of necessary resources and the need for any backup crews, and prepare for the possibility that any resources brought in to supplement the required workforce may not have previous experience or adequate competencies and will require some level of assessment and training. -
Determine supply chain reliability You've ensured a safe and compassionate workplace for employees, assessed potential risks, anticipated likely scenarios that can impact your company, evaluated your workforce needs, and feel nearly ready to restart operations, but that doesn't mean your supply and distribution chains are in the same position. Before being able to say you can restart successfully, you’ll need to assess the readiness of your supply chain and logistics.
Determine the current and longer-term availability of critical supplies and the reliability of their transport mechanism. If the raw materials you need aren't currently shipping, or won't be available for long, you'll need a backup plan. Decide if access to alternate suppliers is available. If not, develop a specification sheet and implement a quality assurance process for input materials from new suppliers you identify. Assess your company's raw materials storage capacity, develop demand projection analyses and subsequently, a production plan. Just like your supply chain, if your distribution logistics including warehouses and distribution centres are impacted by COVID-19 restrictions, you'll need a backup plan for that, too, to ensure the ability to transport your products to end-users. -
Assess operational readiness Before initiating a restart, companies need to make sure all equipment and systems are fully ready to operate. Organisations should conduct a hazard identification and risk assessment on each operating unit to make sure it can restart safely and without incident. Here, companies should be sure to engage operating personnel and seek their input. After all, this personnel working on the shop floor or on-site at facilities are in the best position to be aware of and expose potential or existing hazards.
Organisations should also determine critical controls, assess them for integrity, and inspect and test them for proper functionality. If it is determined that additional controls are necessary, they should be implemented before any restart occurs. At this point, a comprehensive start-up procedure should be developed to guide all restart activities, and it should be reviewed with operating personnel and their feedback and input should be incorporated. Detailed pre-startup checklists should also be prepared for personnel to use.
Managers and appropriate company leaders should be involved and walk the line to participate in all readiness assessments. If deficiencies are identified, they should be addressed, and the assessment should be repeated. Once all operations are determined to be ready for the safe restart, the ERC should be briefed on all readiness efforts and provide its approval to proceed with a start-up. -
Ensure Prompt and Open Communication Because restarting operations and maintaining momentum behind a successful restart is a fluid endeavour with numerous variables to consider, it is very important to build and maintain clear lines of communication, both internally and externally. The company’s recovery plan should be shared among all employees, and communication mechanisms between leadership, managers and front-line workers should be in place to track the progress of the plan and respond to direct input from workers implementing it. Their input should be actively encouraged, and any concerns raised or ideas proposed should be acted upon promptly.
Similarly, it is important to maintain regular and clear communications outside the company. For example, check in frequently with suppliers to make sure there are no potential disturbances to your supplies of raw materials. Manage expectations among customers and shareholders to provide them with a realistic view of your operational capacity and any difficulties you may anticipate in meeting their orders now or in the future.
Conclusion COVID-19 has resulted in a business environment the likes of which few if any, companies have ever experienced. The path ahead contains numerous challenges and additional unforeseen risks for organisations that are eager to resume operations. While it will not be "business as usual," with thoughtful and deliberate planning companies can develop a process for resuming their operations that results in a workforce that is ready, confident and assured of its wellbeing; a safe restart that minimizes disruption and ultimately improves operations; and an organisation that is fully in control of its plan to recover to pre-disruption performance levels despite today's uncertainties.