Zero Harm Culture
dss+ works with a number of clients across industries to build a Zero Harm Culture to improve safety performance and effectively address risks in day-to-day activities across all levels of the organization. This is especially important in regions experiencing high levels of growth in infrastructure and economic development.
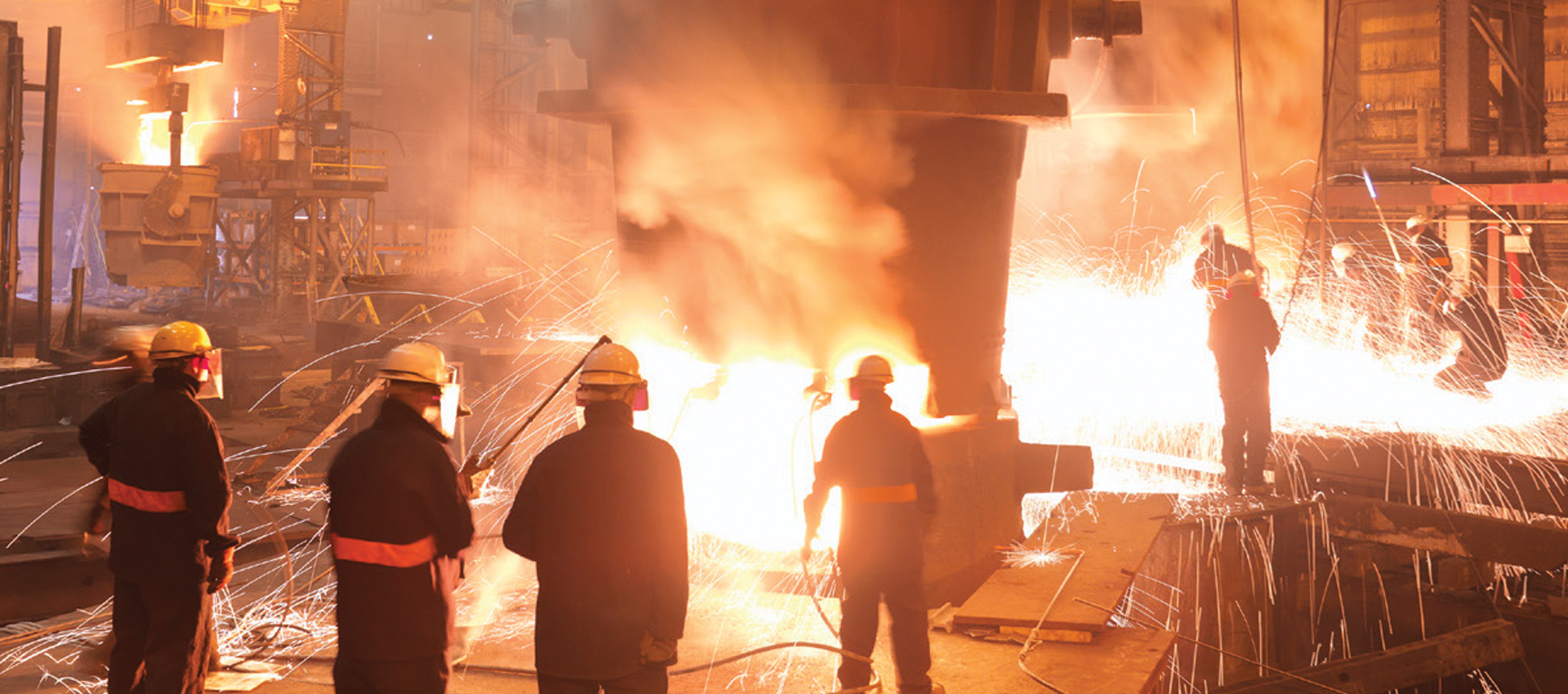
Building a Zero Harm Culture for the Middle East’s steel manufacturing industry
Market Context
In the Middle East, substantial investment into diversifying its economy away from oil and gas has been seen. IQPC Middle East* says the total value of active infrastructure projects in the Middle East has surged to $1.14 trillion.
The region’s infrastructure development is still growing and bringing with it a big demand for construction materials, such as steel, electricity, water and cement, not to mention adoption of new technology and a skilled workforce.
Impact on Operational Risks
With the rapid growth and expansion across the region, dss+ believes that there is real opportunity to help create a world-class safety culture for employees working in steel production. That is why dss+ supported the World Steel Association in establishing Safety Principles for the entire steel industry as well as supported many steel companies with improving their safety performance.
Safety Culture Transformation for a Steel Client in GCC
dss+ partnered with a steel manufacturing client to assist them in developing an effective safety transformation program. This case study explains the challenges, approach, activities and outcomes of the program implemented.
dss+ started by conducting a safety assessment which provided the client with the necessary insights and focus areas needed to create a Zero Harm Culture and to ensure the long term sustainability of such a program. From here, our client was able to execute the project through two distinct phases:
- Phase 1: Contain risks in day-to-day operations.
- Phase 2: Build the systems, and enhance organizational capabilities and safety culture.
PHASE 1 - Summary
The focus of phase 1 was to immediately contain top day-to-day physical risks in the field, while coaching the organization in the process, as well as building foundational success enablers for the program. Phase 1 had four key deliverables:
- Safety Governance: Engage all levels of the organization in a structured way with clear roles and responsibilities to drive and sustain a strong safety culture.
- Field risk mitigation: Identify and mitigate key risks in a joint effort among operations, maintenance, and safety teams.
- Safety leadership development: Drive the cultural transformation through the leadership team by equipping them to be role models in safety.
- Communication: Increase risk awareness and employee engagement through visual and live communication channels to demonstrate the impact and support the transformation.
1. SAFETY GOVERNANCE
To improve and sustain our client's safety performance, dss+ designed a robust governance structure that links top management expectations to the shop-floor priorities in a structured way, with clear reporting lines, mechanisms and supporting leading performance indicators. The main purpose of an effective governance structure is to communicate risks and progress updates bottom-up, as well as cascade decisions top-down. The structure was equipped with digital dashboards at different levels to measure and monitor safety performance in an effective and structured way and in real time.
Key outcome: An integrated safety governance system effectively managing the organization's safety performance with the aid of digital dashboards allowing different stakeholders to monitor a wide range of Key Performance Indicators (KPIs) and help them make informed decisions to reduce risk.
2. FIELD RISK MITIGATION
dss+ experience shows that individuals working in the steel manufacturing industry have a high tolerance to risk due to the hazardous nature of the industry. Hazards are typically accepted as a normal part of doing business, leading to complacency and inadequate understanding of the severity of risks in the field.
The Risk Identification and Mitigation campaign was designed to:
- Form task teams in each department to conduct site visits and identify potential unsafe acts and conditions.
- Ensure the relevant client individuals were included, such as representatives from HSE, maintenance and operations, led by the relevant client department manager. This was critical to break through existing silo thinking and get the organization focused on a common goal of mitigating the correct risks.
- Capture unsafe acts in own areas through photography or video. These were work shopped against various scenarios from which an action plan was developed. This created a standardized process across the various departments and allowed the different teams to become more integrated and aligned when dealing with day-to-day risks.
- Identify the top three risk in each department and develop a detailed mitigation plan with action owners and timelines.
Key outcome: Safety in the plant became a priority for all employees, beyond the HSE department, and each individual was made accountable. Setting the right safety KPIs per department also encouraged a team-work mentality as each department worked towards achieving their safety goals. Coached resources from all departments on implementing a sustainable risk mitigation process to build a continuous improvement culture.
3. SAFETY LEADERSHIP DEVELOPMENT
As one of the most important building blocks for a Zero Harm Culture, the leadership needs to 'walkthe-talk' for employees to enact better safety processes. Through our Safety Transformation Programme, we were able to:
- Engage with top executives and management teams within the organization and introduced several Visible Felt Leadership coaching sessions in the field.
- Introduced a mandatory Management Safety Walk which took the leadership to the field where they were able to identify and mitigate safety risks, as well as interact with the shop-floor on a weekly basis.
Key outcome: The benefit of the activity was two-fold. Employees at shop-floor were able to see and experience management's approach to safety and how they were actively looking for ways to improve. Leadership could demonstrate their commitment to the safety of their employees.
4. COMMUNICATION
In our experience, a common pitfall dss+ experiences when a safety transformation program is implemented, is the lack of communication and alignment on objectives between shop-floor employees and leadership. An intensive communications campaign was launched to raise awareness about what a good PSM program would look like and align expectations of the organization on the need for the change. dss+ achieved this by conducting over 30 town-hall meetings and creating message campaigns across strategically selected areas in the plant.
Key outcome:Employees were able to recognize risks, felt more open to raising concerns about unsafe situations, ask better questions and bring to light issues which may have previously gone ignored. Visibly Felt Leadership enabled division managers, department managers and section heads to demonstrate not only their care for employees but commitment to finding solutions in a respectful manner.
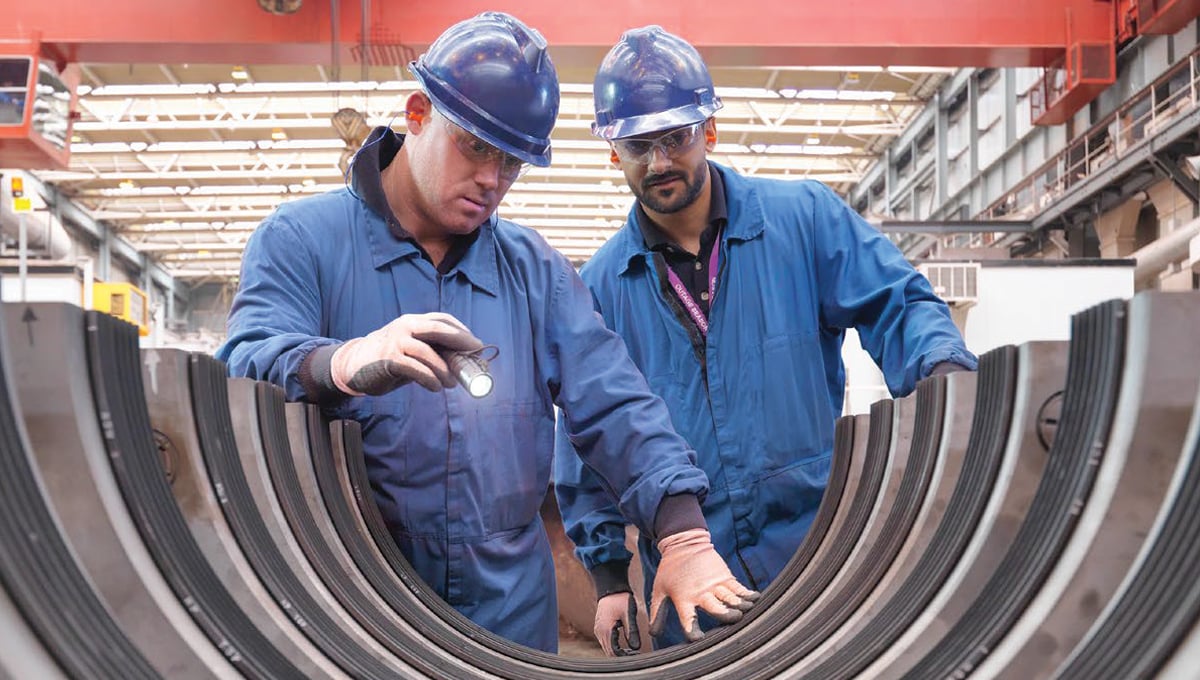
PHASE 2 – SUMMARY
Once the foundations for safety transformation were implemented in phase 1, the teams shifted the focus on building the systems needed to enhance how safety performance is managed and build organizational capabilities which are required to support the cultural transformation. dss+ always advocates for this approach as it ensures long-term sustainability of the safety transformation program and the right foundation is in place to build a Zero Harm Culture. To execute this, dss+ implemented the following:
1. Building the Systems: Developed key missing safety systems, and reinforced existing ones, which was achieved through cross-functional task teams covering all departments while injecting the dss+ best-practices to specific needs. These systems included but were not limited to:
- Permit to Work: dss+ redesigned the Permit to Work system to move from a paper exercise where permits were viewed as a formality needed to start work to a risk based tool facilitating communication of risks and controls between operations and maintenance personnel.
- Lock-Out and Tag-Out (LOTO): We have introduced a Lock-Out and Tag-Out system to ensure positive isolation on all energy sources during maintenance activities, which was not the current practice on site. This was a major breakthrough, thanks to a leadership decision to implement the system regardless of all the challenges, which strongly demonstrates putting employees’ lives and well-being at the top of its priorities.
- Contractor Safety Management: dss+ designed a seven (7) step comprehensive system to manage contractors, not only during job delivery but across the entire contract life-cycle from pre-selection to contract signature, execution and feedback. The system allows the organization to manage the contractor’s safety performance through a structured approach with clear KPIs.
2. Building the Capabilities: Conducted training and coaching sessions on the utilization of all new and revamped systems to build the capabilities and ensure understanding and sustainability of the systems. These include but are not limited to sessions on effective Risk Assessment, Incident Investigation, Contractor Safety Management, Safety Governance, and Permit to Work, Lock-Out & Tag-Out and developing Standard Operating Procedures.
Key outcomes: Revamped systems to support the organization in effectively managing their safety performance. Each system includes KPIs and audit protocols to ensure compliance and continuous improvement.