Expert view: Process Safety Management in Mining and Metals
We sat down with Alfredo Verna, a Principal in the dss+ global Operational Risk Management practice, to get his perspective on Process Safety Management (PSM) and how it has changed over time, and what lessons mining and metals can learn from Oil & Gas.
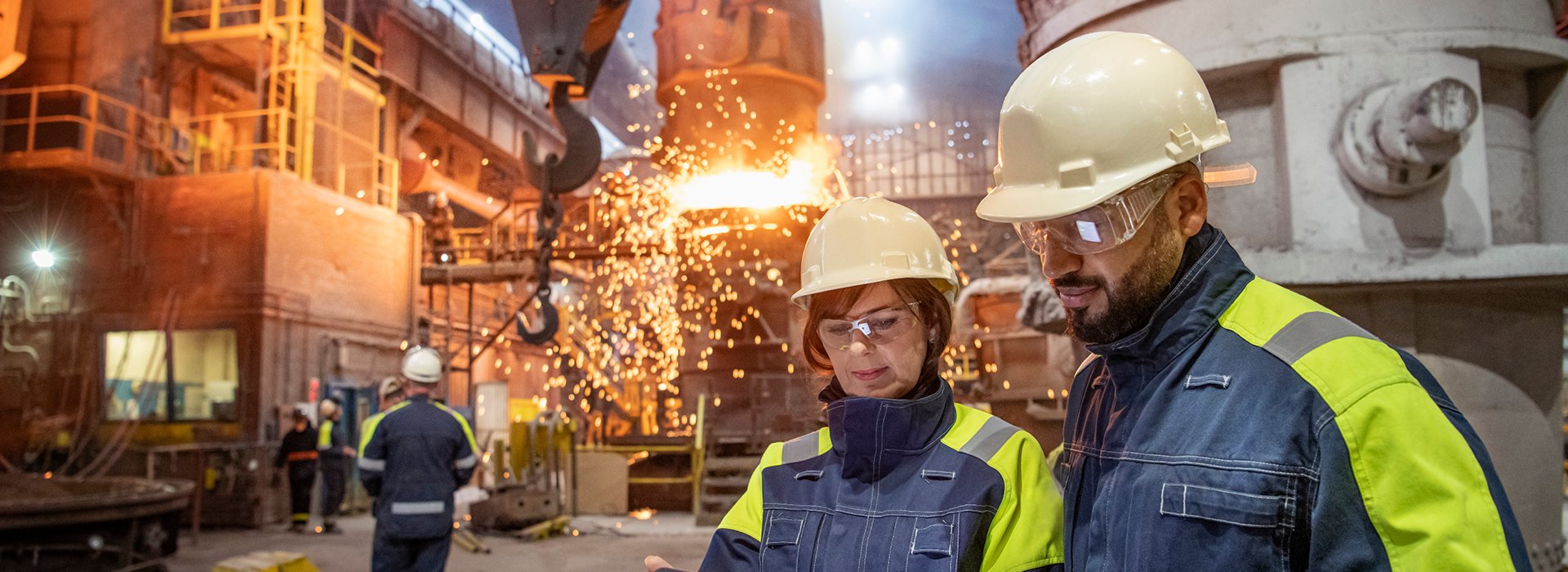
As a seasoned expert, Alfredo Verna has over 35 years of experience in PSM and Operational Risk Management, particularly in oil, gas, mining and other heavy industries. He has managed over 50 PSM and organisational change projects in Europe, Middle East, Africa and South America. He has also led over 50 operational risk diagnostic projects across the oil & gas, chemical, petrochemical, metals, and utilities industries. He holds an MSc in Chemical Engineering and is a Chartered Engineer.
Q.
You have a wealth of experience in Process Safety Management (PSM) and have been in the industry for years. How has the landscape changed since you first started, and what are the trends that you are seeing in the space?
The major change between when I started in the industry until now is mostly awareness - most companies, nowadays, understand that PSM is not just an "add on" or another management system to take care of; indeed, it is an essential aspect of overall asset management. Nevertheless, we continue to see many companies struggling with ineffective implementation of PSM: far too often it is seen as a separate framework for "specialists" and not ingrained in day-to-day operations. In response, some of the specialists that design PSM programmes can do this in such a way that make them complicated and abstract, with the result that people on the ground perceive it as bureaucratic burden, with no or limited added value.
Q.
Why should heavy industry care about something like PSM? What are the payoffs, and do they have broader applications?
PSM is an essential framework to operate and maintain assets more efficiently, safely and with a higher degree of reliability, but some industries struggle to see the relevance. Recently I visited a large Aluminium production site, where leadership were doubtful if process safety could apply to them, since they were not a refinery. These misconceptions derive from a limited understanding of what Process Safety is about. At this particular site they handle a wide range of chemicals and hazardous materials, and use natural gas, if water comes in contact with molten metal it increases in volume by a ratio of approximately 1600:1 creating a deadly pressure wave. Yet, there is still a misconception that Process Safety incidents can only occur in the oil & gas industry.
The reality is that the application of PSM fundamentals does not only reduce risk, but more often than not has a positive operational impact, as processes and control logic are better understood, failure modes of key equipment and the impact on production and safety are more evident and documented and critical assets are maintained to prevent functional failure.
Q.
PSM is something that is mature in industries like oil & gas, but still relatively new in mining and metals. Why do you think that is?
Sadly, PSM has evolved as a result of some catastrophic accidents which have plagued, over the years, not just the oil & gas and chemical industry, but any industry handling processing, storing or manufacturing hazardous materials. In the past, oil & gas and chemical/petrochemical Process Safety accidents were prevalent and the focus was first directed to these Industries. However, it has become evident that these are not the only industrial sectors where uncontrolled releases of hazardous materials and energy can and do occur, sometimes with devastating effects. As a result, over the last few years, many companies in the mining & metal, waste/ wastewater management, pharmaceutical and food & beverage industries, amongst others, have had to start thinking about Process Safety the hard way. I often notice that after a number of years, many people, even when working in a high hazard industry, lose the perception or the "smell" of risk – unless this is triggered or re-awakened by an accident or a high potential near miss.
"The reality is that PSM fundamentals do not only reduce risk, but more often than not have a positive operational impact."
Q.
As the mining and metals sector starts to recognise the importance of robust PSM, what are the lessons you think the industry can learn from oil and gas?
The oil & gas industry as a whole cannot be taken as a beacon in the dark, as far too many catastrophic accidents continue to occur at Upstream, Midstream and Downstream assets. However, the oil & gas industry has learned that Process Safety must be treated like any other business process, it is not just another management system that the Safety Department needs to take care of. Process Safety must be a line management responsibility: solid foundations for a PSM system are built if there is a full understanding of key Process Safety risks, and if each PSM element is tailored to act as a barrier preventing or mitigating them. Several oil & gas companies also invest, through awareness campaigns and the development of adequate competencies and capabilities, to "demystify Process Safety", to make it more understandable and relevant, particularly to Operations and Maintenance personnel. This is how the mining and metals industry can learn from the sector.
"Leaders are responsible for setting the tone at the top and fostering the psychological safety and employee engagement necessary for excellent safety performance"
Q.
What are some of the biggest mistakes that you’ve seen companies making with regards to PSM?
There are still many misconceptions about Process Safety and the benefits that an effective PSM system can bring. These are situations I often face when working with companies in a variety of industrial sectors:
- PSM is seen as a specialised, complex matter which is better left to the "experts". In other words, the inability to see that an effective PSM approach should permeate the entire organisation and everybody on site should have a basic and practical understanding of process safety risks in their area or in the activities they perform.
- The emphasis on the design rather than the effectiveness of a PSM programme. It is disappointing to see that sometimes Process Safety practitioners and auditors are those partially to blame for this mindset. If an audit focuses on “paper”, rather than on how that paper helps to understand and control the unique risks for a particular site or activity, people in the organisation pay more attention to get the paper “looking good” rather than the overall effect that it has.
- The inability to "see" and recognise Process Safety Hazards and observe the degradation of risk controls in the field. Far too often PSM training for operators is academic and removed from tangible examples.
- The desire of some leaders to achieve all KPIs without question. Scrutinising "green" KPIs is important to reducing complacency and staying aware of all risks. For example, KPIs reflecting the effectiveness of critical risk controls and exposure depict a optimistic situation which does not match the reality in the field. When there is a disconnection between the "virtual" risk, as represented in charts, risk matrices, etc. and the "real", higher risk, which reflects the actual level of integrity of critical risk controls, a feeling of complacency can develop and the vulnerability towards serious accidents increases.
- Divergence between safety ambitions and the reality in the field. Ultimately, even the best technical PSM programme is likely to fail without a strong leadership team that embodies the desired safety culture. Leaders are responsible for setting the tone at the top and fostering the psychological safety and employee engagement necessary for excellent safety performance. Everybody in an organisation can easily detect if leaders are credible, if there is a disconnection between what they say and what they do. Once a leader has lost credibility it is very hard to recover it - people become cynical and detached and lack conviction for the stated objectives.
Q.
Is there any advice, after your years of experience, that you would give to the c-suite deciding on investing in PSM transformation?
It’s important for leadership to understand that Process Safety is not rocket science. Having a better understanding and control of key risks and improving safety can be quite simple. It is a matter of "going back to basics", making Process Safety alive by investing in proactive measures for risk management.
Sadly, what we still observe today is that far too often the C-Suite is prepared to invest in Process Safety only after the company has experienced a severe accident. Sometimes we come across cases of, for example, a newly appointed CEO or COO putting Process Safety on their priority agenda after they personally experienced a Process Safety event in their previous company.
This is, to a point, understandable and it is a real challenge for every professional working in Process Safety. How can I convince the leadership team and my colleagues that they need to spend time and effort to erect barriers against potential risks that have rarely or never materialised?
Ultimately, the role of leadership is to gain a full view of all risks that can pose a threat on the value and reputation of the company and understand the level of vulnerability to each of those risks. Among them are the Operational Risks, of which Process Safety Risks are a subset. We can be persuasive with the leadership team - and prompt them to act - if we are able to demonstrate, with compelling examples, that barriers to prevent the occurrence of some risks are built in sand and not in rock, and that weak barriers or, even worse, weak barriers falsely perceived as being strong, significantly increase the vulnerability to catastrophic events.
"The role of leadership is to gain a full view of all risks that can pose a threat on the value and reputation of the company and understand the level of vulnerability to each of those risks."
Finally, we often say to our clients that they need to maintain a sense of unease or of vulnerability, as this mindset helps them avoid complacency and that past good safety performance is not a guarantee of equally good future performance. Those who work in Process Safety also need to maintain this sense of vulnerability and inadequacy, never stopping to question themselves: have we really helped the organisation to unearth their biggest threats? Is what we propose going to be effective? Is it sustainable or just a "quick fix"? Have we learned from our mistakes? Ultimately, are we contributing to lower the risk for the people at the shop floor, those who are exposed to the risks? Have we done enough?