Judith Inberg: Viewing Problems as Opportunities
With a lifelong passion for understanding how things physically work, Judith Inberg, CTO for Aalberts Integrated Piping Systems, explains why it's important to embrace transparency and view problems as opportunities.
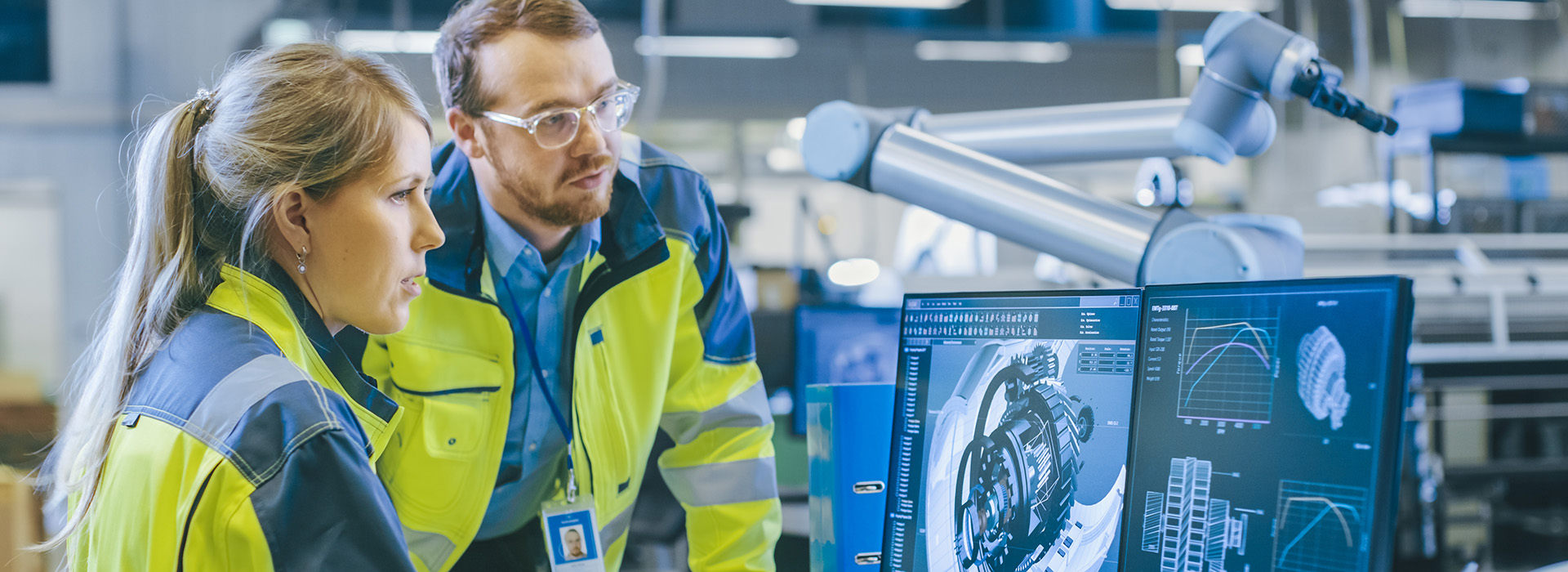
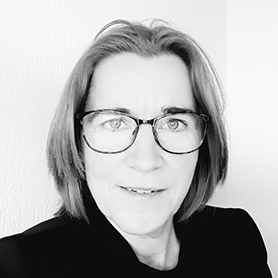
Judith Inberg
Chief Technical Officer, Aalberts Integrated Piping Systems
Q.
What has influenced your journey into operations and what has helped your career progression?
I always knew I'd end up working in industries that make things and my journey so far has completely influenced my current role. As a child I remember wanting to know how things worked and would even take apart my alarm clock and toys. Then at school I enjoyed learning maths and science and so engineering felt an obvious path for me to take. Following my mechanical engineering education at university and a PhD in Polymer Fracture mechanics, I started working in R&D product development. I then expanded my knowledge with business administration, stepping into operational excellence both in industry and consulting, which has been my major focus for the past 20 years. This has taught me so much about end-to-end operational businesses, from purchasing through to R&D, production and supply chain, and how people work in these businesses. This learning has been a fantastic voyage and is vital and very relevant for my current role as CTO, as I understand the impact and dependence on other areas of the business and the challenges they face. Aalberts IPS is a wonderful, technology based, energetic and dynamic company and I am right at the heart of it.
Q.
How important is the role of leadership in the success of any initiative? What are the main attributes of good leadership that you have seen?
I could not agree more with your question. It's not the mechanics of operational excellence that makes or breaks it, it's really the role of leadership at all levels that makes it happen, and it can only happen if leaders understand their own role in it. It goes top to bottom. An important element is a culture where mistakes and deviations are seen as improvement opportunities rather than something to get punished for. You should not feel shy or ashamed to put out where the improvements are, sharing in a supportive or structured way is key to the results in what I have seen. As a leader it's vital to see what can be better and then to work with people to make it better – for that transparency on all levels is necessary. You have to have access to the right data and have a standardised, visible way of working that points out where you deviate and what problems need to be solved. What I personally like, and try to do myself, is the Gemba walk leadership approach, whereby you really go and find out what's going on in different areas, ask questions and learn how people deal with the issues that they face. It's about understanding the problems first-hand, rather than simply reviewing results.
"It's not the mechanics of operational excellence that makes or breaks it, it's really the role of leadership at all levels that makes it happen."
– Judith Inberg, Chief Technical Officer, Aalberts Integrated Piping Systems
Q.
In what capacity do you see technology and innovation improving operational excellence?
The new technology certainly allows us to learn a lot more and bring in the transparency I talked about earlier. For example, the Industry 4.0 move unlocks a whole new chapter in possibilities there. The digital technology of 4.0 allows us to access and process a lot more data, and learn more about what's going on. Eventually it will allow us to get ahead and predict where the deviations will be. I don't think we've understood the full possibilities of what that brings yet. Likewise, when we learn how we can use the data in the virtual environment more and more possibilities will arise, as you can start testing decisions in that environment, whether it is plant layout or equipment set-up or product designs, it allows us to try out different scenarios and then implement them quicker. This will also impact on sustainability because you can try things out in a virtual way before building a machine that doesn't work, or need to move things round, there's a lot to gain. I am sure there's many more possibilities, a new era is coming.
Q.
You mentioned sustainability, what impact do other roles such as safety, risk management and sustainability have on operations?
Risk management and safety are an integral part of everything you do in Ops. They are more established than sustainability, that's much more of an upcoming topic that I'm working much more actively with now. Our discussions are about exploring what we can do, what we have to do and what's inevitable in every area of the business. I think all businesses are in the same position because everyone wants to take sustainability into account. All stakeholders expect us to do this, whether that's our own employees, our shareholders, clients, communities. It increasingly determines my innovation agenda and requires readiness for all parties involved to balance the various components, take the necessary decisions and work with the consequences.
"True OPEX makes you much quicker in your decision making and much more agile in responding to changing conditions, whether that is production set-up or conditions in the market."
– Judith Inberg, Chief Technical Officer, Aalberts Integrated Piping Systems
Q.
Can you expand on how transparency impacts OPEX? What are the other key drivers?
One of the key elements revolves around having the right data and having it transparent so that it's clear to see when you deviate from where you're supposed to go. Then it is about making the improvement steps really visible and make sure people at all levels feel accountable and empowered to point these elements out. Just like safety, point out if there's a deviation from how you've agreed to work, for example if I go into the factory without my safety shoes I really want someone to tell me. True OPEX makes you much quicker in your decision making and much more agile in responding to changing conditions, whether that is production set-up or conditions in the market. This means you can really narrow what you need in terms of resources, from materials to energy and the people you need to do the job. I think resource scarcity is one of the biggest challenges globally, which gives a new impulse for companies looking into their OPEX status. You need this to stay relevant for your own employees, for your customers and other stakeholders, spend your resources wisely, and this desire to grow and stay relevant is inherent to all companies.
Q.
As we celebrate International Women's Day, what would be your key message to other women looking to progress in operational management roles?
In truth I never think of myself as a woman in operations - it is other people that point this out every now and then. It has never been part of my decision making. You determine your own journey, but what has helped me on mine is having people who have given me that extra push and encouragement to reach for more, and my advice would be to all to ensure you find people like this around you. My message to anybody is that it's a vibrant field to work in and not just for those with a technical background. Just trust your senses and opinions and go for it.