Janneco Pothuis: Safety aims and ambitions
Inspirational parents helped kickstart Janneco’s interest in safety. Now working for a dynamic company that is a global pioneer in sustainable water infrastructure, she explains why back to basics, applying a human touch and avoiding Mickey Mouse behaviour are essential to achieve safety excellence.
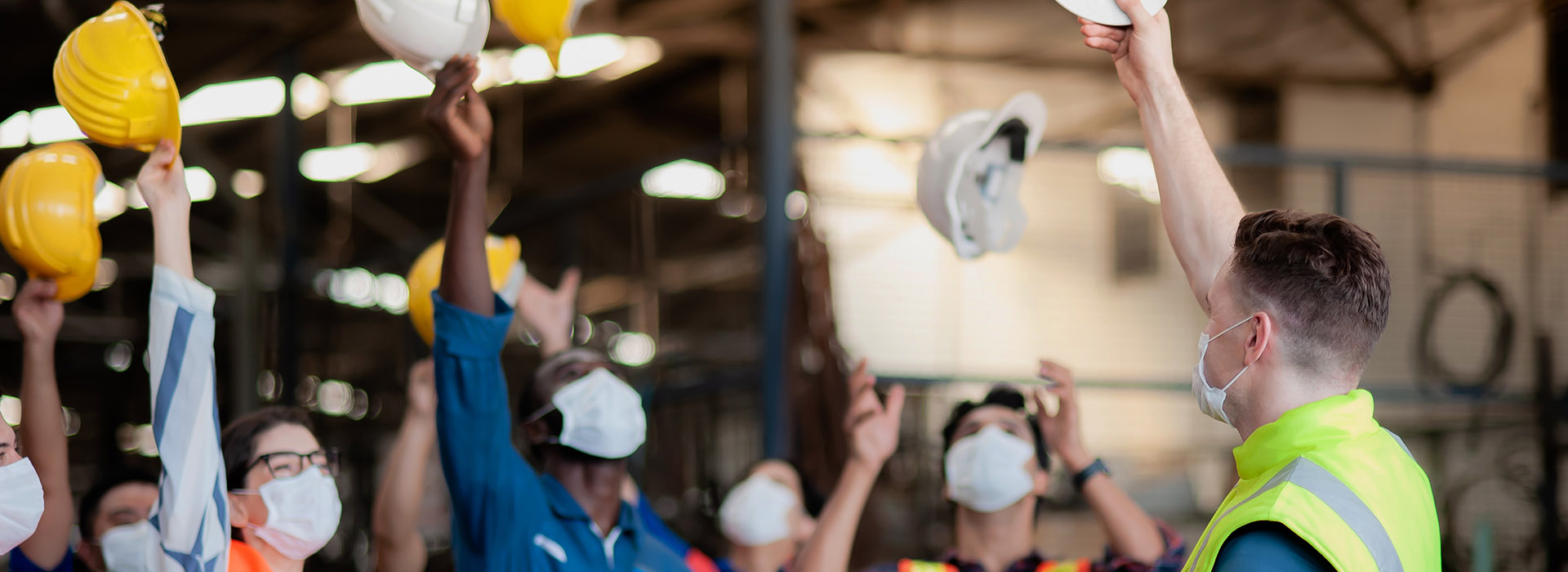
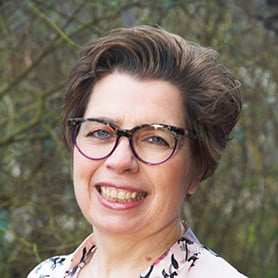
Janneco Pothuis
HSE Cluster Manager, Wavin Nederland B.V.
Q.
Tell us how your parents inspired you to embark on a career in health and safety?
My mother was born at a time when it wasn’t as easy as it is now for females to go to university. As a result, she and my father always treated me, my brother and sister equally and encouraged us to reach our potential in education and chosen career paths. My mother went on to achieve a Masters in her sixties, which is inspiring. Equally, my father was an accident investigator in the insurance industry. So conversations around the dinner table about why explosions were possible even in a powdered milk factory and how things can go terribly wrong without the right approach to safety used to captivate our imagination and attention as children. I went on to study environmental sciences, specialising in the work environment, which eventually got me to where I am today.
Q.
What would you consider to be the biggest drivers of good safety culture?
As the business environment has evolved and companies look to modernise, they have to become much more people-focused, rather than simply developing rules. It’s getting better, but there’s still a long way to go. Still, there are signs that the safety culture is changing, particularly in terms of getting leadership involvement to match safety ambitions more fluently. It’s easy, for example, to yell at people to follow safety rules, but that approach generally does not work. You need your leadership to translate their aims and ambitions on safety into words and actions that resonate. If you don’t get this communication right, you end up with this big safety disconnect across different parts of the company ecosystem.
"You need your leadership to transform your aims and ambitions into words and actions."
– Janneco Pothuis, HSE Cluster Manager, Wavin Nederland B.V.
Q.
Are you a fan of standardised or customised safety communication?
It helps to employ all the communication tools at your disposal. Yes, we use standard communication programs, but it is also important to take into account the different communication needs of specific groups. Executives need a very different type of safety detail than employees on the shopfloor, for example. So the emphasis changes, but the basic message of not wanting anyone to get hurt stays the same for everybody. This is key. Then there are campaigns, posters and training sessions as part of the safety toolbox. But if you don’t continually refresh and modify communication tools, they will lack the relevance and energy needed to keep staff engaged and motivated.
Q.
What do you see as significant challenges in today’s safety role?
Practical application is a considerable challenge. We live in a world where there are some new and exciting ideas on safety, but implementing those ideas is not easy when trying to achieve a standardised approach to safety across regions and cultures. It needs military precision to make it work. It’s often the case that some production locations have a more mature safety culture than others, and we have to take that into account. And of course there are cultural differences too. But it’s never a case of one continent being safer than another. There are often significant differences in safety maturity within the same region, and we need to consider that. For me, it’s more a question of how we adapt communication to convey the same basic safety message. But it’s also about understanding what makes people react differently to safety messages. The arrival of COVID-19 threw all of this into perspective. We saw how challenging it was for people to take on this extra level of stress to get the work done without compromising their health. Covid times gave us a renewed appreciation of just being able to work with people, actually looking them in the eyes and saying “good job”. I think this lack of contact has reduced the impact of safety messages. While we have learned that more actions than we previously thought can be done remotely, the human factor remains a big part of safety success. If you take the human factor entirely out of the equation, you run the risk of weakening safety behaviours.
"It is easy to focus on things going wrong, but we achieve more when actively acknowledging the progress made."
– Janneco Pothuis, HSE Cluster Manager, Wavin Nederland B.V.
Q.
The importance of technology as a safety enabler has undoubtedly been highlighted during the pandemic. How do you see this playing out?
Advances in technology are incredible in terms of what we can employ in the field of health and safety, but I’m wary of its widespread application without thinking through the consequences. Again, it’s going back to basics and ensuring that we are not introducing new safety risks by forgetting to reinforce key safety messages. Sensors, for example, are an excellent innovation for avoiding collisions. Still, if the driver becomes too reliant on the sensor rather than his or her safety behaviours, and the sensor fails, it introduces a new hazard. So technology should support good safety behaviour, not replace it.
Q.
Your approach to safety is very much grounded in human collaboration and clear communication. Are these your go-tos when developing a safety programme?
Yes. Ensuring leadership can communicate the right safety messages and have clear KPIs that help them in the right direction is essential. Equally, you can’t talk about safety or expect employees to follow safety rules when the basics are not in place. Working environments need to be constantly reviewed from a safety aspect; machinery needs to be maintained and equipment kept up to date and in good working order. Also, avoid Mickey Mouse safety. This is what I refer to as safety performance where the emphasis is placed on achieving a certain level of safety performance above all else. In this situation, you create a culture where safety problems start getting pushed under the carpet. Outwardly, it’s like a happy Mickey Mouse cartoon yet underneath, there’s the real world of the shop floor where incidents are no longer reported. People become scared of getting punished for making mistakes and hazards can no longer be dealt with properly. Finally, let’s be positive! It is easy to focus on things going wrong, but we achieve more when actively acknowledging the progress made. Don’t get stuck in a negative safety approach, find room for improvement and go for it!
"If you don’t continually refresh and modify communication tools, they will lack the relevance and energy needed to keep staff engaged and motivated."
– Janneco Pothuis, HSE Cluster Manager, Wavin Nederland B.V.