Making the Italian Food & Beverage Industry a Safe Place to Be
Despite multiple disruptions (Brexit, Raw materials, transportation and energy costs, new consumer behaviours…), the Italian Food and Beverage industry performed well in 2020 and is showing positive trends in 2021. The number of injuries decreased by 14% in 2020 compared to 2019 but the number of fatalities rose by more than 30 percent in 2020 (30 fatalities - some of them due to covid situation - vs an average of 20 over the last 5 years)1. In theory, a reduction in minor injuries should also lead to a drop in more severe incidents, but this does not appear to be happening in the Italian food and beverage industry.
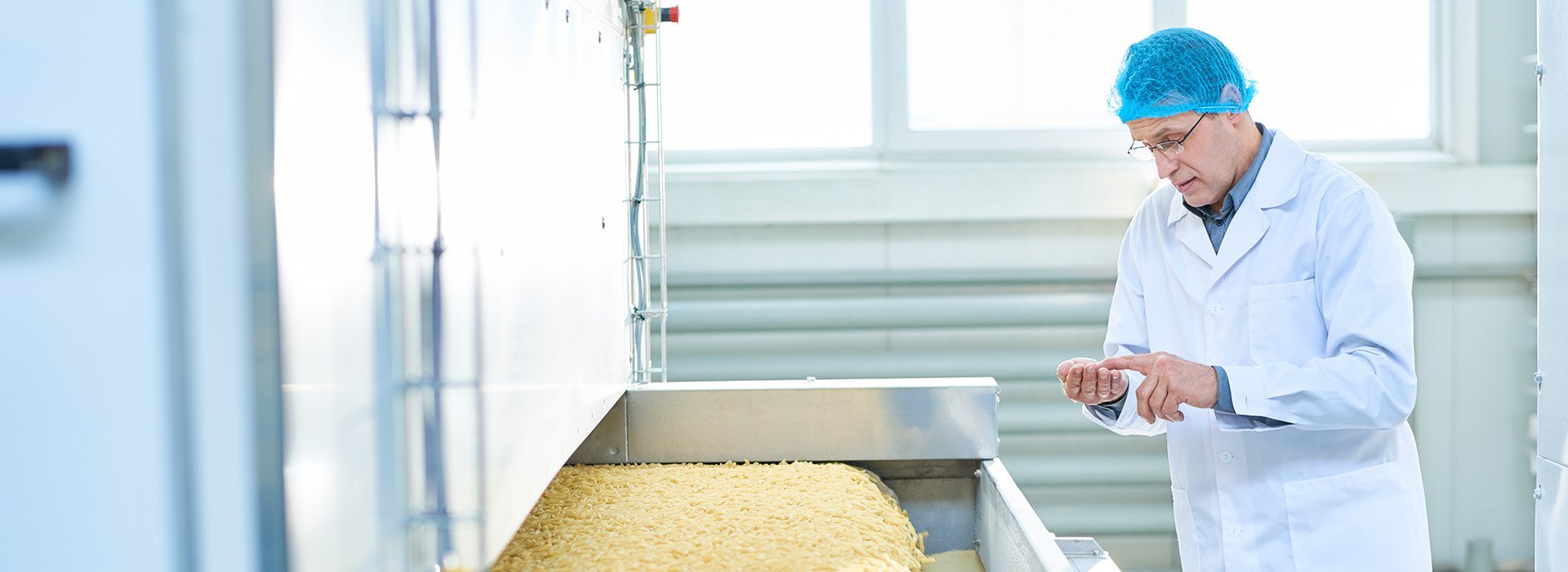
An increase in on-the-job fatalities since 2020, despite falling injury rates, demands greater focus on risk awareness in the sector.
An analysis of SIFs (Severe Injuries and Fatalities) in Food manufacturing companies revealed that a focus centred only on lowering the incident frequency index may also mean top risks are neglected.
What are the main factors that contribute to this situation in Italy? What actions should safety managers consider to move towards the net zero incidents goal?
30%
in 2020.
Based on our global expertise in risk management, industrial safety, and safety culture assessments, and our local experience in the Italian Food & Beverage industry, here are the top 5 key actions to implement:
Make Safety a Value
Priorities change and values last over time. Business leaders who really want to see a reduction in SIFs need to pursue a cultural change in mindset and behaviours, communicating the value of safety through coherent and concrete actions. For example, rigor in applying Life Saving Rules, empowerment of people in implementing a “Stop Work” policy and commitment of Leadership to understanding and solving issues on the ground.
Embed Safety into your operating systems
Even if Health & Safety is a topic on the agenda of leadership, the culture in the food and drinks sector is still primarily focused on preventing issues that could affect production, quality and food safety which are of indisputable importance to consumers. Health & Safety are considered separate and are not integrated into most operating systems. Most of the safety activities are systematically delegated to the Health & Safety function with limited or partial involvement of line management. It is critical to align and engage employees in both the safety and production functions.
Invest in Supervisors leadership skills
Supervisors in the food and drink industry are often overloaded with tasks and are struggling to drive and manage safety issues at the same time. They are also generally reluctant to intervene in correcting unsafe behaviours because they don’t know how to do it and prefer to compromise when they have to meet production targets. Skills and competencies must be developed and continuously enhanced at all levels of the organisation, especially among middle management and supervisors, through the practice of safety routines and use of tools for detecting and preventing those situations that can lead to SIFs.
Positively engage all your employees
Routine work and physical workplace challenges (e.g. noise, humidity, etc.) make complacency among the workforce in this sector an issue. In other words, repetitive tasks tend to lead to employees falling into behavioural patterns. That lowers risk awareness and has an effect on operational discipline. Employees get used to taking shortcuts if line managers fail to point them out for fear of causing conflict. Workforce concerns related to high-risk operations need to be recognised and respected through listening and working to stimulate identification of solutions, by recognising contributions, honouring and awarding ideas and suggestions. In addition, the workforce has to be constantly involved in implementing actions and the implementation of identified improvements must be followed up.
Integrate your contractors as a critical resource
Contractors are seen as a resource in the food and drinks sector but it’s taken for granted that they know what to do, how to do it and have their own safety management system. In other words, it is assumed they will work in line with safety regulations and don’t need to be supervised. The use of seasonal workers during the high season adds complexity and triggers an increase in safety risks. Contractors must be fully integrated and supported when carrying out requested tasks. Responsibilities and processes must be clearly defined and applied to ensure safe operations and avoidance of interferences.
"An effective safety management culture will include all these elements and bring them together to not only reduce operational risks and improve operational excellence, but also to change safety culture for good."
– Pietro Femia, Key Account Leader, Italy & Central Europe
SOURCES:
Business leader
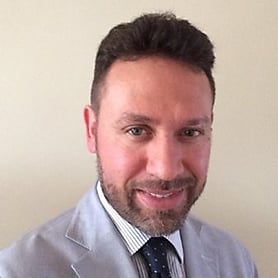
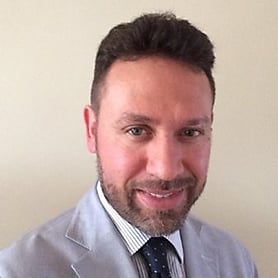