How to win in times of crisis
With optimistic signs that we are nearing the end stages of the global pandemic, is now the time for organizations to put their foot on the accelerator? Certainly, while there is some understandable near term caution until the full extent of the damage to businesses and global economies has been digested and uncertainty in Europe over the outcome of Brexit is resolved, good news on vaccine efficacy and a more settled political landscape in the US is a cause for optimism.
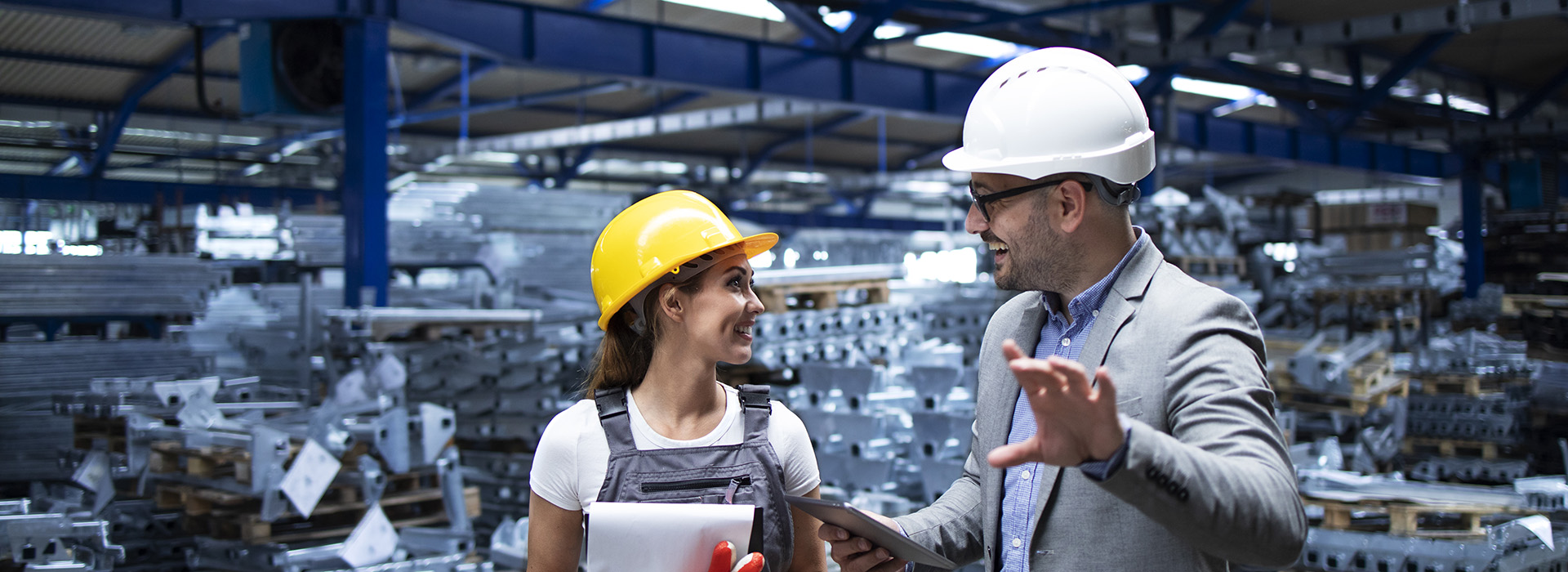
So what actions should business leaders take to ensure they adapt rapidly and sustainably, taking into account the business uncertainties that they face? As a first response the majority of companies downsize their investment programs and prepare savings plans. But such actions may further exacerbate the pain without a parallel focus on long term growth plans.
Instead, by overhauling production models and creating an inclusive, agile culture among their employees, companies are likely to rebound and recover much faster and more effectively. It is on this last point that DuPont managed to make a difference in response to the 2008 crisis.
Replicating the quick recovery and agility of DuPont in 2008
As with most companies during the 2008 financial crisis, stock prices plummeted and DuPont was no exception. Through the crisis, DuPont’s stock declined over 60% from its approximate pre-crisis peak. This marked a decline slightly higher than the broader S&P, which fell by as much as 51%.1 Despite this, in the first quarter of 2009 DuPont introduced 500 new products, almost double the number introduced in the same period of 2008.2
It’s a strategy that, along with a focus on pricing, squeezing value, maximizing working capital, and reducing costs to help the company ride through the crisis, involved some big bets on long term projects. This focus on both the short and the long term was a key factor in DuPont’s success at the time.
It was an approach that, without knowing the severity of the subsequent recession, paid off. DuPont’s stock rose by over 86% between March 2009 and January 2010. This compared with S&P growth of 48% over the same period.2
While DuPont’s speedy and successful recovery in the 2008 crisis was not solely as a result of its newly developed Dupont Production System (DPS), it certainly helped DuPont squeeze the accelerator at the right time and under the right conditions.
With ever shorter business cycles and more than 200 locations of various sizes around the world, DPS provided DuPont industrial sites with the mechanisms to accelerate reaction times, in response to abnormal fluctuation in demand, by 30-40%. These mechanisms were all the more effective because the portfolio of assets was reviewed to optimize flexibility.
Within DPS, the response to an abnormal and potentially lasting drop in demand is for the site to adjust its cost base in line with its production forecasts. When there is a significant recovery in demand, each product generates a higher margin because it fully benefits from the cost adjustments made. The maximum production potential is then utilized, and the necessary costs incurred to capture opportunities and respond effectively to demand.
Additional challenges of putting the right mechanisms in place
Some people will say that there is nothing new in the key principles of Production Excellence (PX). They are right. This is largely common sense. But variations in approach can trigger a range of different outcomes. In particular, taking a more holistic approach to the implementation of both hard and soft mechanisms that assess the impact of leadership, culture and safety can enrich the process.
In addition to this, many companies are faced with implementation challenges that make their level of agility insufficient, and even more so in times of crisis. Pushing development to lower levels of organization and involvement of personnel in these activities makes the difference.
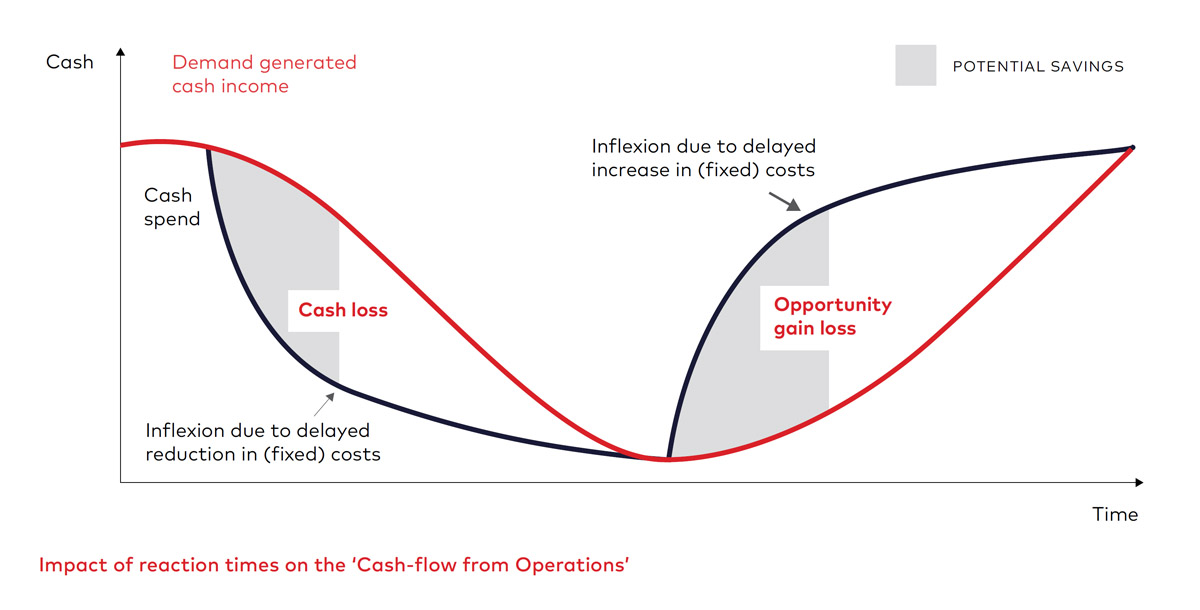
“The accelerated deployment of the DuPont Production System has enabled us to end the crisis quickly and sustainably, with an unexpected positive impact on our results and our cash flow”.
Impact and results at DuPont
The decision to deploy DPS was based on a strategy of sustainable development and strengthening corporate resilience that was fully supported by the entire Executive Committee. In 5 years, the deployment of DPS generated more than USD 5.5 billion in net profit and more than USD 3 billion in CFO (Cash Flow from Operations).
Involving a deep, rapid and lasting change of mindset at all levels of the organization, DPS aims to move forward by seeking the “80/20” in solutions and impact rather than looking for perfection which often takes too long to define and implement.
This change of mindset was based on a clear understanding of first, what a successful outcome would look like and, second, what operational steps to get there would be. This experience showed that there is no need to over-plan, as it is generally impossible to fully and precisely define all the actions necessary to achieve the result. The conception and planning must be done progressively supported by a priority management system based on the impact and the probability of achievement.
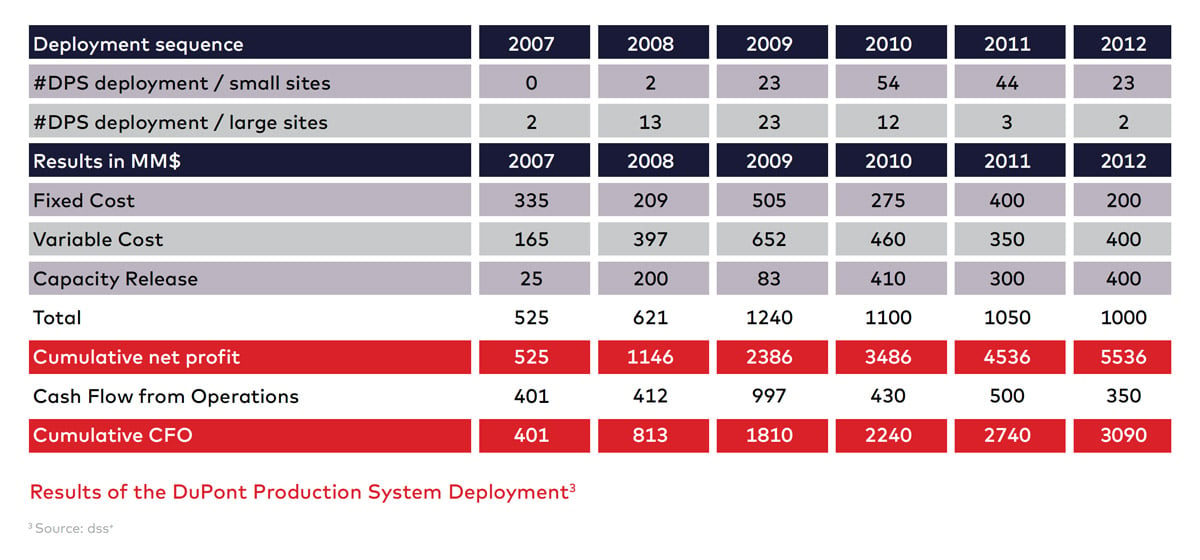
Hard and Soft Crisis-Exit Mechanisms
Hard
- Reduce costs combining long term with short term goals
- Improve capital buffer / working capital
- Optimise pricing
- Forecasting production performance
- Use integrated activity planning to optimize resources and activities
- Fix production losses
Soft
- Ensure leadership behaviour is aligned throughout the company: one voice
- Allow employees to own change
- Be customer focused
- Place safety & performance as a core pillar of change
- Integrate flexibility and agility
A burning platform for change
Interview with Marc Doyle, former business director at DuPont
What did DuPont do differently during the 2008 financial crisis that saw them recover much more quickly than other companies? Marc Doyle, who was a business director at DuPont during the time of the crisis and eventually became CEO 10 years later, talks through some of the decisions made at the time and how they impacted DuPont’s recovery.
With the crisis presenting the burning platform for change, significant restructuring was needed to progress these short- and long-term initiatives. The deployment of the recently developed DuPont Production System (DPS) was a factor in the company’s agile response to the crisis and restructuring plans. Marc Doyle notes: “There was recognition that DPS could be rolled out to support building
these initiatives internally.” Designed to train employees on standard tools and techniques to solve problems, eliminate waste and measure progress, by the end of 2009 DPS was deployed at more than 60 DuPont plant sites globally, with a presence in all four of the company’s regions. In 2010, DuPont was working to successfully implement DPS at an additional 66 sites worldwide.4
Transforming company culture While Doyle points out that not all DuPont plants used DPS to the same extent, those that implemented it saw significant benefits. Hit hard by the 2008 economic crisis, leadership at the DuPont Uentrop facility in Germany adopted DPS to maximize skills and resources, rather than cut jobs. Through increased efficiency and improved execution, maintenance costs were reduced by more than 28%.5
The ability to transform company culture is a further benefit of DPS and one that was particularly successful at DuPont’s Maydown site in Northern Ireland, which Doyle holds up as a keystone site. “At Maydown you can see an empowered, hands on and proactive approach where people from the top to the bottom can speak about the objectives of the business; the objectives of the plant; and where they fit into it. It’s an environment where you can see the benefits of continuous improvement processes and good ideation.”
The link between a change of mindset following employee engagement and empowerment not only benefits operational excellence but also improves safety levels. In the six-year period following the roll out in 2009 of DPS at the Maydown plant site, there were zero safety incidents and record quality performance. In addition, performance productivity improved by 20% and an annual contribution of $1.5m made through quicker transitions.6 More recently in July 2019, Maydown celebrated 1,000 days without an injury at the plant.7
The ideal crisis playbook
Implementing improvements is one thing, but sustaining that improvement is often where companies show a lack of resilience. In the case of DPS, line-led transformation is key. Once the deployment team is in place, allowing site personnel to take full ownership at roll-out helps maintain a continuous improvement (CI) focus. Such resilience often hinges on leadership to constantly challenge their ability to improve and do better; transforming behaviours to create more of a high performance culture.
DuPont most recently has referred to this transformation as its culture MAP. Doyle explains it as follows: “M is making an impact, which is about personal empowerment. A is act like owners; so we want employees to have more of an ownership mentality. And P is partner with customers, which is all about the external orientation,” explains Doyle.
As Doyle concludes “For DuPont, culture changes are always a work in progress.” But there is little doubt that looking back at the 2008 crisis, big bets on mega trends, reassessing performance criteria and the adoption of new production systems marked out DuPont as the ideal crisis playbook.
In the 6 year period following the roll out of DPS at the Maydown plant site, there were: 0 safety incidents 6
Performance productivity improved by 20% 6
An annual contribution of $1.5m made through quicker transitions.6
In July 2019, Maydown celebrated 1,000 days without an injury at the plant.7
“At Maydown you can see an empowered, hands on and proactive approach where people from the top to the bottom can speak about the objectives of the business; the objectives of the plant; and where they fit into it.”
SOURCES:
- https://www.forbes.com/sites/greatspeculations/2020/03/24/dupont-down-40-over-the-last-one-month-will-it-continue-to-underperform/?sh=70314b15bd88
- https://www.icis.com/explore/resources/news/2009/06/23/9226997/insight-dupont-innovating-a-way-out-of-the-crisis/
- dss+
- 2009 DuPont Annual Review
- https://www.consultdss.com/content/dam/dupont/products-and-services/consulting-services-and-process-technologies-redesign/consulting-services-andprocesstechnologies- landing/documents/Stronger-After-Storm.pdf
- https://www.slideshare.net/TRACCiiS/the-dupont-production-system-creating-a-culture-for-sustainable-integrative-improvement
- https://lovebelfast.co.uk/dupont-maydown/
Business Leader
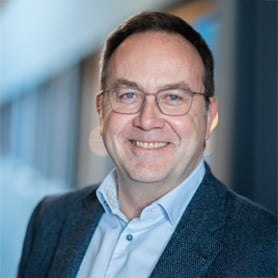
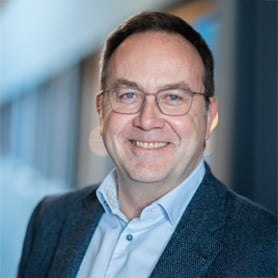