Global Expansion Benefits from Safety and Risk Organisation
Organisations throughout Asia are expanding their footprints not just within their countries but around the world, either by setting up new facilities or acquiring existing companies. However, many do not have clarity around managing safety and risk in unfamiliar jurisdictions, leading to costly mistakes as they learn by trial and error.
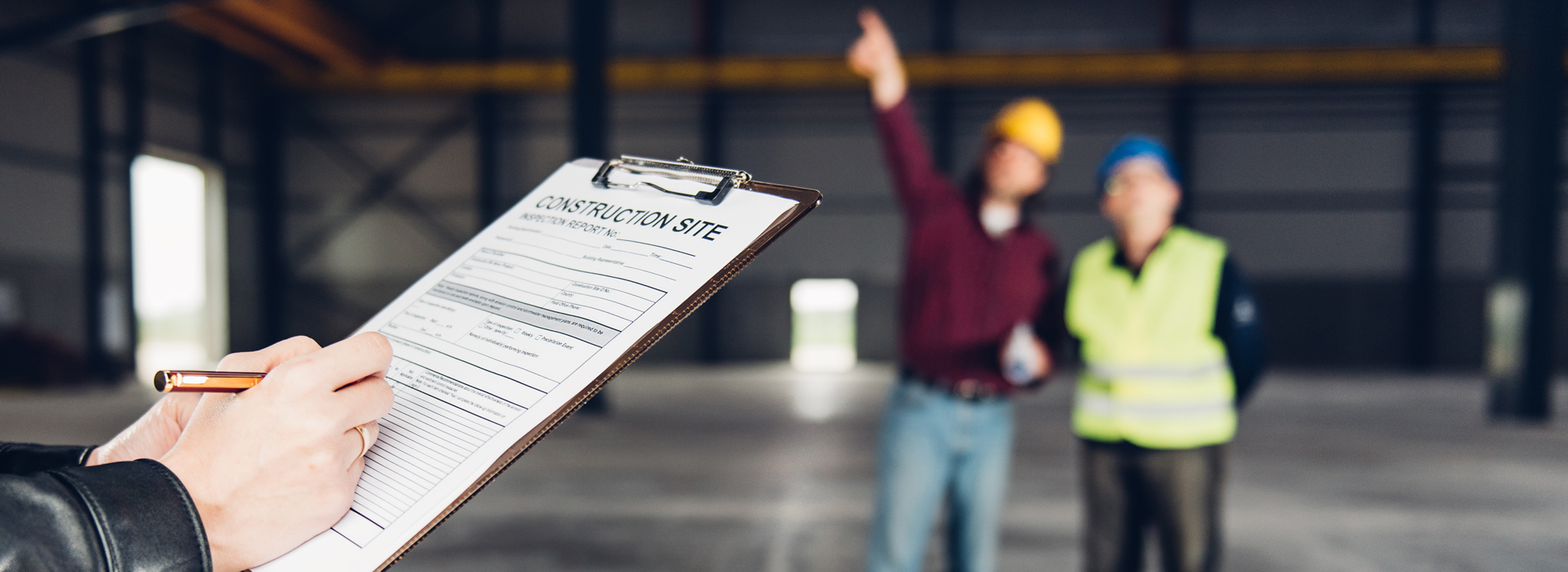
In any new acquisition, especially regarding a foreign company, there is likely to be a lack of knowledge of safety standards and legal requirements. It can be difficult for internal resources to take on oversight of international expansion while managing current operations, especially since there is no single common framework for measuring performance, making meaningful comparisons, developing capabilities or integrating operations from one country to the next. Add differences in language and culture, and this becomes an exceedingly complex undertaking.
Drawn from extensive experience in aligning global organisations around safety and risk, the following direction can help any company institute a corporate safety culture that extends across countries and businesses. And, while this paper doesn’t specifically address occupational health or environmental components, the same process can be applied.
Pre-acquisition Due Diligence
Acquisitions can unfold in a variety of ways, often hindering due diligence around safety systems. While financial, legal and even logistics due diligence are generally front and centre—and sustainability is gaining ground thanks to attention on ESG— involvement by quality, safety and development teams continues to lag.
If, for example, a buyer wants to keep a potential acquisition confidential, the manufacturing group may not be involved at all. This is often the case in the fast-moving consumer goods sector, where the focus is on the value of the brand rather than where or how it is made. However, due to the risk of reputational damage or business interruption in the aftermath of an incident, we need to reconsider this approach.
Where time and resources are available for safety and risk due diligence, a detailed study of plant conditions, performance metrics, current operating standards, and the safety climate and culture should be performed. The cost of bringing plants up to standard—as well as past incidents, penalties paid and pending safety-related legal issues—can have a big impact on financial calculations.
Post-acquisition Integration Plan, Starting Day 1
The day after a deal is finalised, risks and liabilities are on the new owner’s books. Therefore, as the deal is getting close, a clear plan must be established for day 1 through full integration, which can reasonably be expected within about 24 months.
Developed by a dedicated SHE leader and their team—an independent corporate safety organisation—the integration plan should outline processes for the first week, first month and so on, including reviews and recommendations for:
- SHE performance
- Legal compliance
- Current standards and gaps
- Robustness of plant infrastructure and processes
- Digital technologies in use
- Quality of plant leadership and safety professionals
"The risk of not assuring compliance and consistent safety standards is too high—incidents and noncompliance can damage a corporate reputation overnight."
Specifically, the following must be immediately addressed within the organisation that has been acquired:
- Assessing the organisation’s leaders’ safety mindset and safety stewardship. Leadership should have the ability to communicate, engage with the people on the ground and have an ownership mentality. If they are found lacking, it is better to quickly replace them with strong leaders from the parent organisation.
- Setting clear safety expectations for leadership and the organization going forward.
The Key to Unified Safety: The Corporate SHE Organisation
Any company with multiple facilities or businesses should introduce an independent corporate safety SHE organisation that crosses business units and national borders. The risk of not assuring compliance and consistent safety standards is too high— incidents and noncompliance can damage a corporate reputation overnight.
In addition, we know that good safety is always good business. Instilling a strong safety culture and systems has been proven to impact operations in a variety of ways— from employee morale and the quality of service delivery to higher yield, greater uptime and reduced waste.
What’s more, a holistic management system allows comparisons to be made from one operation to the next, so you can accurately gauge performance and identify areas that require attention.
"Instilling a strong safety culture and systems has been proven to impact operations in a variety of ways—from employee morale and the quality of service delivery to higher yield, greater uptime and reduced waste"
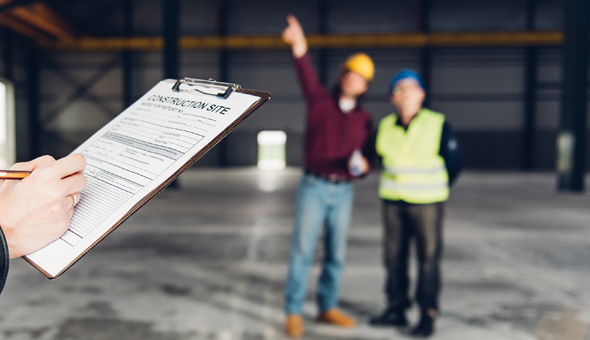
Establishing Your Corporate SHE Organisation
A thoughtfully structured council with a leader who reports directly to the CEO is fundamental to sowing a safety mindset and culture that permeates all sites and countries. Independence is essential to ensure transparency and prevent outside agendas from creeping into performance measurement.
Principal considerations include:
Safety leadership: The choice of a safety leader is of primary importance. Rather than a safety professional, this position should be held by someone who has a real passion for safety—who can influence stakeholders, inspire frontline workers, and work closely with executives and the board. The right candidate should have some process knowledge and, preferably, experience in integration of new teams as well as multicultural understanding and sensitivity, but they are more likely to come out of operations rather than safety management. What’s more, this should be an esteemed, time-limited role that is seen as a launching pad to bigger things.
Information systems: It’s important to gain a quick understanding of an acquired organisation’s information systems, how they perform on leading and lagging safety indicators, and how to integrate those systems with the mother system. Any misstep can be very costly.
Internal and external competencies: There is no right or wrong way to address the division of labour, but determining which competencies should be maintained internally or contracted from outside providers must be deliberate. For example, a petrochemical company would likely want to keep process safety in-house, while a company that outsources manufacturing might be more focussed on strong contractor safety management. Ultimately, leadership needs to look closely at the business and determine what internal competencies are required—and to what level employees should be trained—as well as those that can be more efficiently sourced from consultants.
It’s important to use consultants in a smart way to speed up integration, but the company must learn to stand on its own without relying too much on outside support. In addition, internal members should drive reporting strategies to ensure that relevant metrics are rated and shared with the board.
Roles and responsibilities: A detailed RACI matrix can clarify who is to be responsible, accountable, consulted or informed for all processes—from setting goals and developing guidelines to implementing each specific program. Delineating ownership between the corporate safety organisation, individual site leaders and line management assures that appropriate actions and involvement cascade from corporate to the line level and guides the selection of the right people to lead each competency.
Safety should never be an afterthought. Crafting a clear plan for consistent safety standards and practices, as well as assuring compliance from the moment a new acquisition is under your authority, can help prevent major incidents, protect your corporate reputation, and save significant expense and effort. An independent corporate safety organisation is well worth involving at the earliest stages of any deal.
Business Insiders
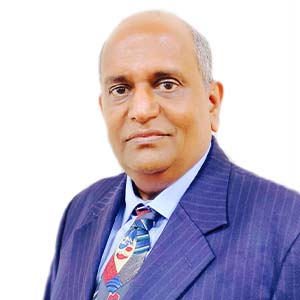
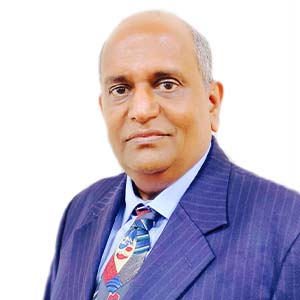