Evelyn Joos: Health and Safety Must-Haves
From a materials engineer in research, Evelyn's move into safety scaled up her science and technical skills to focus on making plants safer and healthier places to work. She explains why leadership, risk management and a go-getting attitude are health and safety must-haves.
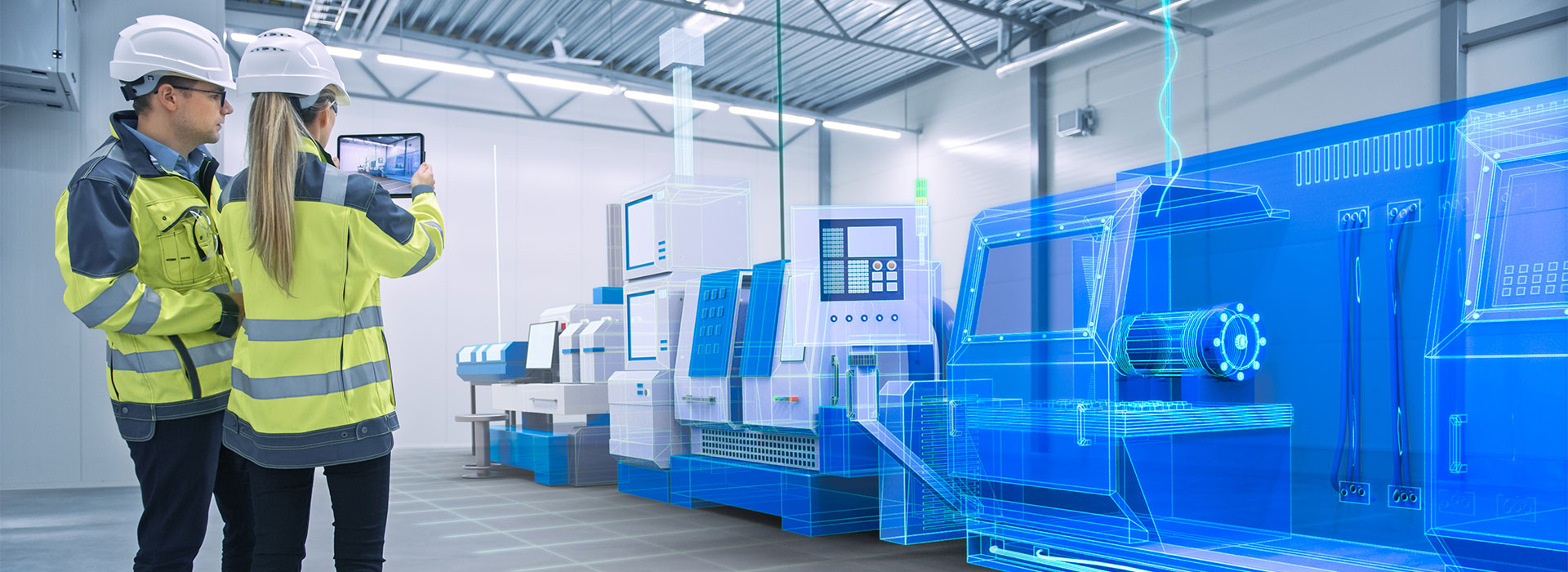
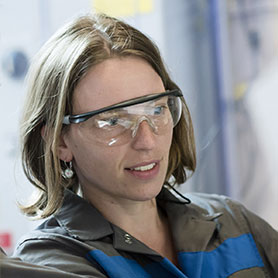
Evelyn Joos
Group Manager Process Safety, Umicore
Q.
When did becoming a safety professional appear on your radar, and what are the main challenges related to your work?
When I started working as a materials engineer, becoming a safety professional was not on my radar. For several years, I was managing process and product development projects in the research department. But I found out that what inspired me most was using my knowledge, science and technology skills for that higher purpose: making plants where people can work in safe and healthy conditions. That led me on the path to becoming a process safety manager. I've since progressed to take on the responsibility of process safety management for all our sites worldwide. In terms of challenges, it's being aware that safety is not an exact science. For example, in thermodynamics and chemistry, you can measure inputs and outputs and establish a clear relationship between both. In safety management, it's more challenging to demonstrate the impact of safety programmes, and clear-cut answers can't always be provided.
"The current health crisis has taught us to be very careful with the "can't happen here attitude" and keep a forward-looking attitude and scenario thinking mindset."
– Evelyn Joos, Group Manager Process Safety, Umicore
Q.
Safety culture is often seen as rigid and applied in a prescriptive, rules-based way. Do you think this culture is changing or needs to change?
In our process safety strategy, technical safeguards play a predominant role. Operational discipline is still essential, but what is even more important are leadership and the organisation's ability to recognise hazards and risks. If you look at case histories of significant process safety incidents, root causes are rarely related to operational discipline alone. This is why safety leadership and hazard and risk management are fundamental pillars of our safety programmes. It enhances an interdependent safety culture. By taking a risk management approach where cross-functional teams are authorised to make collective decisions to manage risks, you'll quickly see the psychological benefits. You expand ownership and involvement allowing leaders to become less prescriptive and freeing them up to coach more.
Q.
What impact has COVID-19 had, and what other emerging operational risks do you see on the horizon?
Producing information about what is changing, how the company is doing and how jobs are affected has been essential in helping people face such a stressful situation. As a lesson, leaders must frequently communicate to reduce uncertainty and foster resilience to meet the challenges that lie ahead. The current COVID-19 pandemic offers a unique opportunity for the process industry to learn and develop continuity plans in the event of other crises. I believe this crisis has, even more, underlined the importance of an organisation's ability to manage risks dynamically. This health crisis has taught us to be very careful with the "can't happen here attitude" and keep a forward-looking attitude and scenario-thinking mindset. Process safety engineers are used to the systematic analysis of potential threats; they take all the various information and then tell a story. When new context and information comes in, we should always use them to reshape our insights and find ways to make things better, safer, more effective and reliable. The crisis has also taught every one of us to look at the curve and make predictions about the next wave in the same way that process control systems monitor critical process parameters. Using advanced trend analytics, we can identify deviating parameters early and make more accurate predictions about possible evolving incident scenarios. It's essential we pursue digitalisation roadmaps and the introduction of trend analytic tools to support safety processes. This approach can help us deal with some of the world's biggest challenges that impact our processes and operations, such as climate change.
"The rise of more sophisticated tools and digitalisation offers a whole new range of perspectives to improve an organisation's safety performance."
– Evelyn Joos, Group Manager Process Safety, Umicore
Q.
We know innovation and technological change can be harnessed to improve safety programmes, but what about implementation considerations?
The rise of more sophisticated tools and digitalisation offers a whole new range of perspectives to improve an organisation's safety performance. From real-time data technologies, and safety apps on mobile devices to 3D visualisation technology, smart wearables, drones, and virtual reality training tools, we are increasingly employing technology. To introduce technology successfully within an organisation's safety programme, getting the human factor right is essential. So it helps to involve employees to create a roadmap for new technology. Importantly, the purpose is not about controlling or monitoring; it's about empowering employees and helping them to make better safety decisions and choices. This will not only benefit safety performance but result in happier and more efficient employees.
Q.
What would you describe as essential elements when building a sustainable safety programme?
It all starts with leadership. We can't avoid the fact that safety leadership is an integral part of building a safety programme. Senior management has to create safe working environments by setting objectives, providing resources, and having dedicated safety personnel. But true safety leadership means you have to be part of it; get involved and understand the safety challenges, so you can inspire others and be a credible and trustworthy part of the process. I think most leaders have the personality and skills to be good safety leaders but dedicated training can really amplify this. Often, it's just about learning simple tips and tricks to engage with co-workers about safety, such as popping up during meetings to ask questions that show a desire to learn and contribute actively. Remember that safety leadership should not be limited to managers or supervisors. It can be anybody who has positive social influence over their peers and an interest in improving safety across the organisation. Dynamic risk assessments are another essential element. This entails updating your risk assessments when you gain new insights. It's about challenging your assumptions on safety, so they reflect the changing world we live in. This way, you continually improve the reliability of plans and safeguards in place. Finally, you have to make safety a positive journey. We need to praise people for good safety behaviours. Many people are working behind the scenes to develop good procedures, build safety systems or follow good practices that encourage others to do so. It often looks so routine that we forget to reward people and allow them to shine. We can also make it more positive by paying attention to terminology. We often focus on accidents or incident prevention in communication, but let's also speak about safety success, safety learnings, and safety wins. If we make it sound more positive, we will begin to see safety as a positive force.
"Jobs in sustainability, health and safety are a team sport. We need lots of different voices and styles to ensure safety programmes have the best chance to succeed."
– Evelyn Joos, Group Manager Process Safety, Umicore
Q.
How would you sum up a career in safety?
Jobs in sustainability, health and safety are a team sport. We need lots of different voices and styles to ensure safety programmes have the best chance to succeed. Diversity of thought and approach is increasingly essential to reflect the safety challenges ahead. Even when you're not sure you can do it, seize the opportunity because that's when you're growing and learning the most. If you are passionate about safety and being a team player, then there's a role for you in safety. Go for it!