Emirates Steel Arkan
dss+ collaborated with Emirates Steel Arkan to implement a safety excellence program (project AMAN – in Arabic it means safety and security), aimed at reducing operational risk and strengthening its safety culture across its operations and touching the hearts and minds of all employees within their respective steel plants.
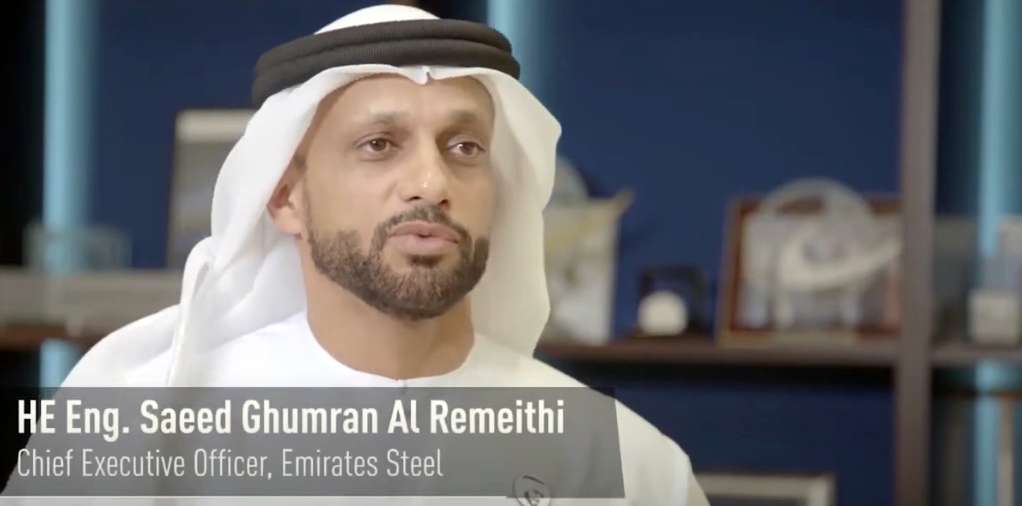
Build a zero harm culture
Cultural transformation to improve safety levels
Established in 1998, Emirates Steel Arkan grew in a relatively short period of time from a re-roller of imported steel billets to a complex integrated manufacturing plant, using modern solutions to tackle traditional industrial problems and generate value for its various stakeholders. Emirates Steel Arkan’s underlying business goal is to be an efficient and competitive producer of finished steel products. To achieve this, the company continually and significantly invests in expansions in the areas of processing, manufacturing and information technology. In addition, these investments help to improve product and service quality, reduce the company’s environmental footprint and increase safety for its workers and customers. Emirates Steel Arkan’s leadership believes in and is committed to safety and brought in a partner, dss+, to assist with developing an effective safety transformation program through an innovative and digitally enabled implementation approach.
The AMAN journey started with a risk-based assessment to identify and mitigate key operational risks and opportunities to strengthen its HSE management system during day-to-day operations. In a joint effort, dss+ and Emirates Steel Arkan launched and executed the AMAN program in order to achieve Emirates Steel Arkan’s safety aspirations and objectives of zero harm. dss+ supported the organisation by embedding a strong and sustainable safety culture across all levels and a managing process to sustain the change in culture.
Diagnostic
The objective of the diagnostic phase, was for dss+ to evaluate Emirates Steel Arkan’s current safety culture and practices using its customised Risk-Based approach (illustrated in figure 1). Several activities were performed, including:
- In addition, the program aimed at raising the level of discipline at the shopfloor to minimise deviations from set standards and focusing on the quality and effectiveness of the safety management system implementation. This coupled with enhanced risk appreciation supported by effective corrective and preventative action execution resulted in significant gains being achieved.
- Reviewing of selected critical documents being used in the current system.
- Interviews with selected key representatives at different levels throughout Emirates Steel Arkan.
- Performed Site visits to observe work practices and behaviours to understand the level of operational discipline, and to review the implementation effectiveness of the safety management system
The findings from the diagnostic and subsequent recommendations were discussed in a mirror-workshop format with Emirates Steel Arkan management, leading to the development of a comprehensive safety culture improvement roadmap, which formed the AMAN program. The AMAN program roll-out plan was structured into three phases:
- Building of safety foundations (establish governance and leadership commitment).
- Enhancing key risk management practices and procedures.
- Address risks and build capabilities in a focused effort(using dss+ Area Transformation approach), with a specific emphasis on the front line and front line supervision.
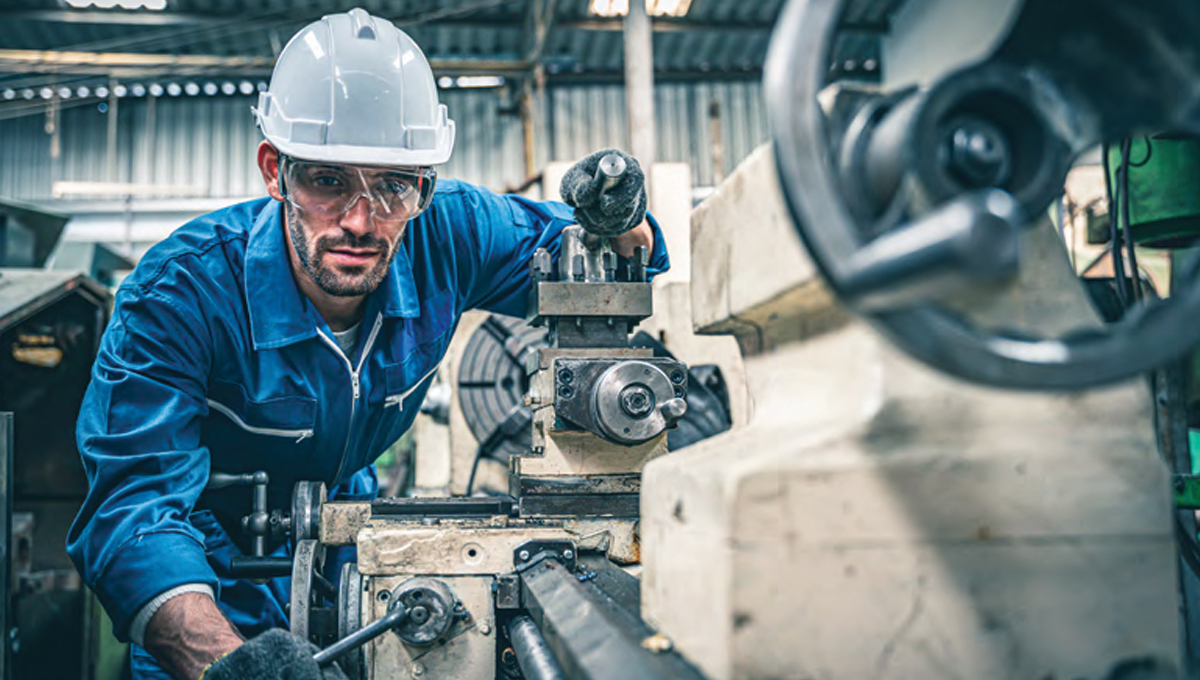
Phase 1:
Build foundations to establish governance and leadership commitment
1.1 Integrated governance model:
Improved and sustained Emirates Steel Arkan’s safety performance by designing an effective governance structure and mechanism at different levels of the organisation. Digital dashboards were used to measure and monitor safety performance in an effective, structured way, and in real time, which supported and empowered communication flow (horizontal and vertical) and decision making. This ensured one version of the truth whilst enabling short interval control on accurate and credible information.
1.2 Visible Felt Leadership (VFL):
Developed and rolled-out a Leadership Program to drive safety cultural transformation by equipping leaders to be role models in safety. Each leader and manager were effectively engaged to develop and launch an individual personal safety action plan to support routine actions and behaviours. This included several coaching sessions focusing on a set of core competencies needed to successfully drive effective safety improvement programs and establish sound safety culture within the organisation.
1.3 Integrated performance management:
dss+ enhanced and integrated the current process for managing and reviewing leading and lagging Key Performance Indicators (KPIs) to support the achievement of safety objectives through data-driven performance discussions to drive line management accountability.
1.4 Principles, Life Saving Rules, Rewards and Recognition:
dss+ supported the design and roll-out of Emirates Steel Arkan’s HSE Principles and Life Saving Rules, and enhanced the existing recognition and consequences practices. Emirates Steel Arkan was provided with a strategic guide on health and safety principles, a communications plan, and processes for dealing with violations of the health and safety rules (i.e. Progressive Discipline) and a training plan for individuals to fully understand the Life Saving Rules. Extensive induction and training sessions were conducted to set the clear organisational expectations for employees regarding either the consequences or rewards of safety practices to change behaviour and encourage operational discipline.
Phase 2:
Enhance key risk management practices and procedures
In order to develop risk-based capabilities across different levels of employees throughout the organisation and shift the focus from “quantity” to “quality” of execution, it was important to focus on implementing six management system elements considering international safety standards, steel-industry leading practices, and local regulatory requirements in the UAE (i.e. OSHAD).
2.1. Permit to Work (PtW):
The PtW system and capabilities in the organisation were reviewed. Stronger guidelines on how to safely execute high risk jobs were put in place. Key practitioners executing the PtW were trained and Process Flow Charts were created. Overall, dss+ upgraded the PtW protocol, procedures and requirements so that issuers could routinely visit the area, for which the work was issued, for effective risk management control.
2.2 Safety Observations & Inspections:
By introducing leading practices in Safety Observations and Inspections (i.e. dss+ Risk Containment Program), dss+ focused on developing capabilities of Emirates Steel Arkan personnel to identify, report, and contain workplace risks, unsafe acts and hazards. This included defining the different observation and inspection activities, ensuring central collection and monitoring using data analytics to understand key patterns, risks or behavioural challenges from these observations.
2.3 Risk assessment:
dss+ and Emirates Steel Arkan developed and implemented a comprehensive Risk Assessment process to enable proactive and systematic identification and assessment of risks. Specific activities included the development and implementation of Operations Hazards and Risks Registers, as well as Job Safety Analysis to ensure activity-based risks are identified and effectively mitigated. Key personnel were trained and coached on Risk Assessments to enhance their capabilities on the new Risk Assessment requirements.
2.4 Contractor Safety Management:
dss+ and Emirates Steel Arkan have developed and implemented a Contractor Safety Management (CSM) procedure, a 6-step process, including the governance required to effectively launch the procedure with a focus on collaboration with end users, the supply chain and health and safety departments to ensure the system was effectively implemented. dss+ utilised the dss+ CSM Process to strengthen the management of contractors’ safety.
Phase 3:
Address risks and build capabilities in a focused approach (area transformation)
Through the dss+ best practice, Area Transformation approach, Emirates Steel Arkan managed to make the health and safety management system ‘come to life’ by engaging Line Supervisors at shop-floor to enhance capabilities and operational discipline and linking it to the strategy and expectations of the ES leadership. This approach has led to a focused effort on mitigating hazards and risks on a daily basis, and improved overall health and safety performance through a consistent set of behaviours and rituals, aimed at management and shop-floor levels to discuss, monitor and sustain safety performance.
3.1 Front Line Supervisors Capability Building:
Front line personnel were identified as a key driver to deliver better safety results. The dss+ team built leadership competencies through training and coaching program focusing on key attributes of the line supervisors, in particular feedback, performance dialogues, focused improvement, difficult conversations, coaching and delegation. The program targeted line organisation (i.e. supervisors), and comprised class-room training and practical coaching in the field during regular day-to-day activities.
3.2 Visual Performance Management and Rituals:
dss+ implemented a visual performance management process to facilitate performance dialogues with the employees and identify improvement actions to ultimately change behaviours. This process has facilitated a continuous improvement cycle at shop-floor level. Daily discussions, monitoring and reporting of adequate KPI’s, both leading and lagging, took place, as well as operations and maintenance performance discussions. Visual boards were installed at departmental and area level(s) with a managing process in place to ensure daily updates and discussions which created open and respectful dialogue among the employees.
3.3 The management operating system (MOS):
The safety performance was measured and tracked through daily, weekly, and monthly performance review meetings which took place to identify areas of improvement and assign relevant actions. The MOS facilitated safety rituals and meetings, coached selected members on running and improving these rituals to ensure seamless communication (top-down and bottomup), presented information visually, analysed data and integrated various departmental interfaces, to action effective management and decision-making processes.
Digitalisation of processes and data
With the multiple ongoing initiatives within the AMAN program, and the increased reliance on data, the Emirates Steel Arkan Leadership team decided to continue its partnership with dss+ to implement an integrated Health and Safety System to manage HSE critical processes in a more efficient manner as well as to accelerate the transformation and further improve safety performance. After only two months from the launch of the new IT software, there was an increase in the quality of data captured which provided better analytics allowing for a more informed approach to HSE performance discussions.