Emerson
The award-winning dss+ STOP® safety training observation program from dss+ provides a path to workplace safety excellence at Emerson’s Rosemount™ measurement and analytical technologies.
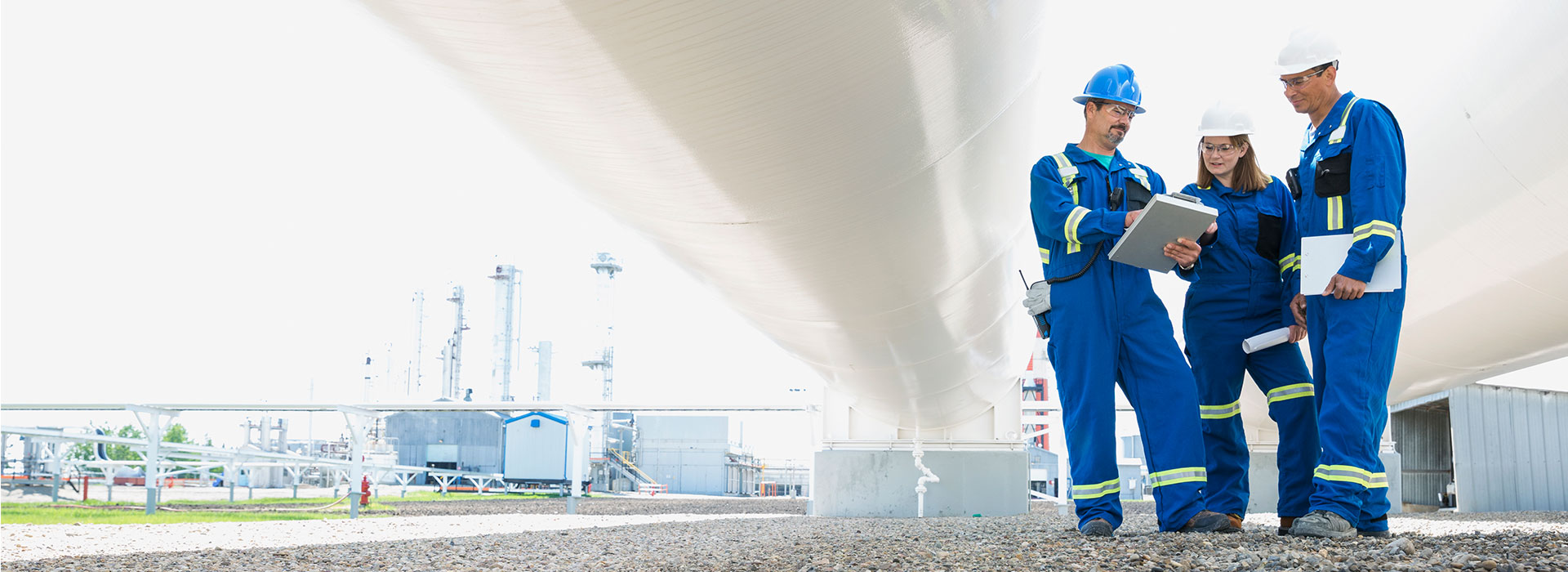
dss+ STOP® – Empowering Emerson Employees to make a difference in workplace safety behaviors.
Creating an environment where People can make a difference
Emerson was founded in 1890 in St. Louis, Missouri, as a manufacturer of electric motors and fans. Over the past 27 years, the company has grown from a regional manufacturer into a global technology solutions powerhouse. Today, Emerson brings technology and engineering together to create innovative solutions for the benefit of customers in industrial, commercial and consumer markets around the world.
Emerson's operating passion is "Consider it Solved" – applying employees' expertise, experience and creativity to develop innovative technology solutions for customers to carry out projects faster, more safely and more efficiently. The company proudly attributes its success to the skills, integrity and commitment of its employees around the world. That's why Emerson has created a workplace environment that encourages employees to excel with a customer-focused, results-driven culture where employee performance is recognized and rewarded.
Emerson is committed to creating a global workplace culture that supports and promotes diversity, embraces inclusion and cultivates respect for the individual, and creating an environment where people can make a difference. Their efforts and reputation have not gone unnoticed. Emerson has received recognition as one of Fortune magazine's World's Most Admired Companies, and Forbes magazine has ranked Emerson among America's Best Employers.
Safety and health – An Emerson core value
The safety and health of all Emerson employees is a core value within the company. The company expects all levels of management and employees to not only anticipate hazards, but also to address them and stop employees if they deem a work environment or task to be unsafe.
At Emerson, the goal to create and sustain a safe and healthy work environment for all of its employees has resulted in a corporate led effort in three critical areas:
- Implementing global safety and health standards that are based on some of the strongest regulations from around the world.
- Tracking global injury trends from first aid, medical treatment, restricted, and lost time injuries.
- Conducting safety and health audits of its operations around the globe.
Corporate safety efforts are led by a Corporate Safety Council, which meets quarterly. The Council sets expectations, provides oversight and tracks progress of the global safety program to drive continuous improvements, reinforce the safety culture and reduce injuries in Emerson's operations. All significant locations have a health and safety committee, which includes representation from members of the work force, to work pro actively in addressing health and safety concerns, and in improving the safety culture.
The next step in improving safety Culture - dss+ STOP®
Even after years of steady progress in improving safety performance the management team at Emerson's plant in Boulder, Colorado – which manufactures Rosemount differential pressure flow meters – decided to engage outside help to explore the next step in improving safety culture.
They turned to dss+ for assistance based on dss+ experience in behaviour-based safety management programs.
dss+ STOP®, an award-winning safety training observation program, is part of the dss+ portfolio of workplace safety training offerings. dss+ STOP® programs are based on tested principles that have been proven to help reduce incidents and injuries.
They use a combination of methods to give people the information, skills and willingness to work more safely, to maximize their learning and to apply what they learn to the real world culture of the facility.
At the Boulder site, dss+ worked with the management team to implement STOP® for Each Other to train the 110 employees – including supervisors, team leaders and plant workers – how to observe people as they work STOP® for Each Other is based on the idea that safety is the responsibility of everyone equally. It helps participants look at safety in a new way, so they can help themselves and their co-workers work safely. The program encourages a mindset where safety is a discussion that takes place every day, not just when completing a formal observation.

Measuring Success At The Plant Site
By implementing the STOP® for Each Other training program, almost 90% of employees at the Emerson Boulder site are now actively participating in the safety program and in improving the safety culture.
According to Katrina Schneible, Emerson Compliance Manager for the site, the dss+ STOP® training has helped maintain an improved level of injuries and incidents at the facility, and employees are also applying the training at home. The site is lowering incident and injury rates, and is empowering employees to talk about safety. Thanks to the dss+ STOP® training, employees are now thinking about others and thinking about what they are doing daily from a safety point of view.
STOP® for Each Other Focuses on:
- Everyday safety. Not just observations, but also communication skills are learned in the program.
- Safety of co-workers. STOP® for Each Other emphasizes how peers rely on each other to work safely in the workspace. It's not just about personal safety.
- Conditions as well as actions. STOP® for Each Other highlights how the interaction of people and conditions work together to produce safe or unsafe situations.
- Peer-to-peer communication. STOP® for Each Other encourages a mindset where safety is an everyday discussion not just completing a formal observation.
At the Boulder site, corporate audits have also been very successful. Schneible notes that "dss+ STOP is an important tool used in accomplishing our strategic goals for each year." Schneible added, "dss+ and dss+ STOP helped us show what we can do in working together to identifying hazards, holding one another accountable, and in communicating effectively to get everyone on the same page."
Each employee is encouraged to complete a dss+ STOP observation once a month. There was an immediate increase in identifying hazards, and management has implemented numerous changes due to the observations. Each employee has also been trained to "See Safety" and "Use their Mind's Eye" before performing a task or function. And there has been a reduction of near miss occurrences because of these increased observations. As a result, the site's safety culture has improved.
"Currently we are at 326 days without a recordable injury. Hopefully we stay on track and hit the year! That would be the record for us."
– Katrina Schneible, Emerson Compliance, Safety and Environmental Manager
Emerson's commitment to continual evaluation and improvement of its health and safety standards will help to keep these numbers on a downward trend. Based on audit results and continuing dss+ STOP observations, facility management now has the training and the tools in place to maintain safety compliance, and provide step-by-step plans to address any issues that are discovered.