Driving energy efficiency from the shopfloor: using the right information for lean operation
Today, any organisation, of any complexity, wants – and needs – to become “lean” by identifying and minimising losses to operate more competitively. For large operations, losses related to utilities like fuel, power and water have become increasingly valuable, as they strive to improve both their bottom-line and their environmental performance.
To achieve their “lean” objectives, process industries benefit from presenting operational data in ways that allow multiple levels in the organisation to recognise losses earlier and address them more effectively. By combining several innovative Operational Excellence (OpEx) tools and embedding new routines, our Production & Energy Loss Accounting (PELA) methodology strongly supports the lean journey.
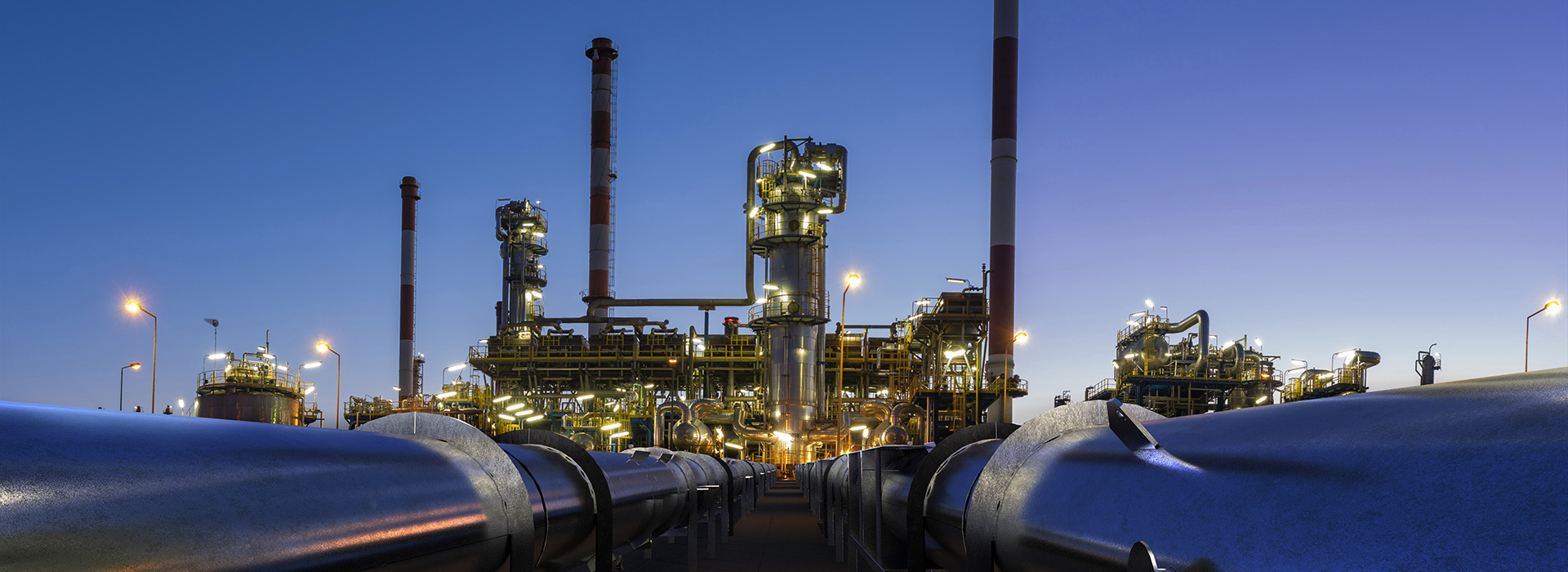
In this article, we'll introduce PELA with a focus on its application to minimise energy losses, sharing an example of an oil & gas client that we helped to generate an annualised pipeline of US$30 M in savings.
What is Production & Energy Loss Accounting?
As its name suggests, PELA can address both production and utility losses via the same approach. We developed it as a novel operating system for process industries, built on proven Lean/6-Sigma principles for reducing losses by making them visible and by short-interval control.
In any process industry, some losses may be easy to spot, like large steam leaks or abnormal flaring of waste gas, but others are less obvious and may be overlooked. Putting a realistic monetary value on any losses can also be challenging, depending on the complexity of the system and the number of factors involved.
Customised data visibility, at the core of PELA, makes it possible to explain, discuss, and then act to remedy operational losses.
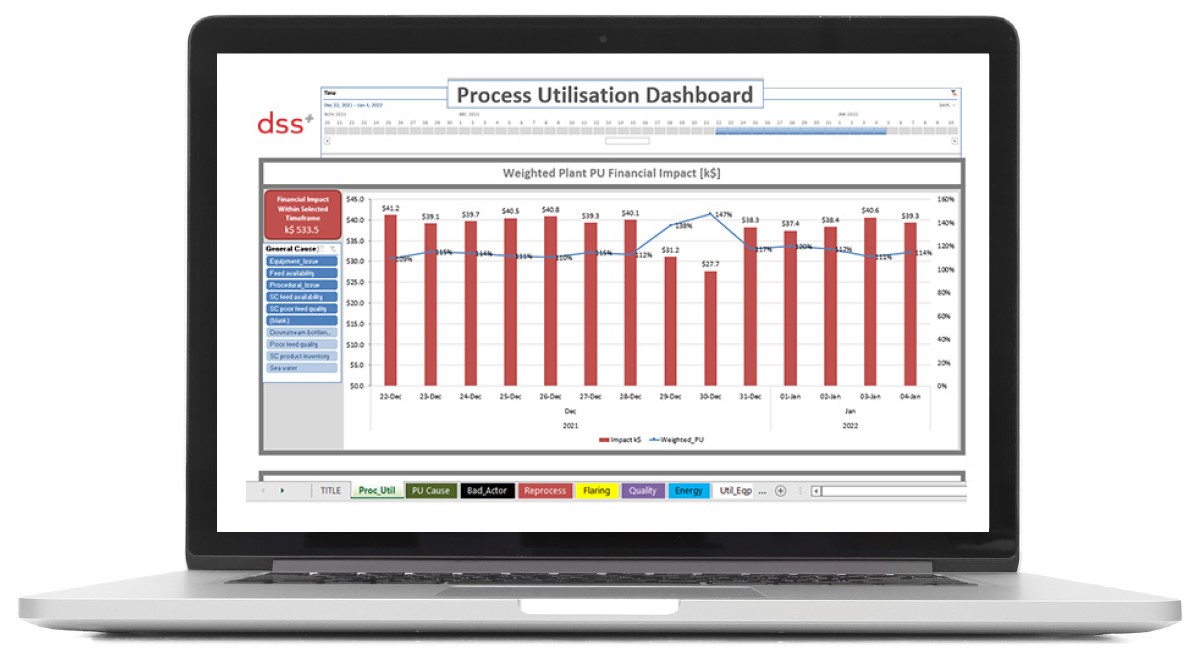
Figure 1: Example of a PELA dashboard showing KPI value, losses, and root causes within a timeframe
Storytelling through effective data presentation
Key to the effectiveness of PELA are its highly customised software tools to present loss information to three separate audiences:
- Shift operators in process plants.
PELA allows shift operators to get specific real-time information about production and energy losses for the main value drivers: asset utilisation, product quality, reprocessing, equipment efficiencies, flaring, etc. They may then take immediate action to investigate and reduce certain losses and are required to use their PELA tools to assign standardised “cause categories” to each loss for later aggregation and analysis. The PELA methodology relies heavily on this tailored categorisation of loss events by operations staff, which feeds into data-driven discussions and solutions. - Asset Managers.
Asset managers, in their daily Operations meetings, receive an overview of key losses in the last 24 hours to prompt ad-hoc discussion or escalation. - Interdisciplinary teams from operations, maintenance, process engineering and production planning.
Meeting on a weekly basis, interdisciplinary teams discuss the aggregated loss accounting data. The system employs a dedicated tool to combine, sort and display information to help teams recognise patterns, bad actors, value lost, etc. This then enables a focussed effort to agree on prioritised action plans.
Customised visualisation and valuation of losses turns operating data into actionable information and makes it possible to explain, discuss, prioritise and then remedy the losses. This fits with a clear “Plan, Do, Check, Act” (PDCA) cycle, as is also advocated by ISO 50001, the international standard for good energy management.
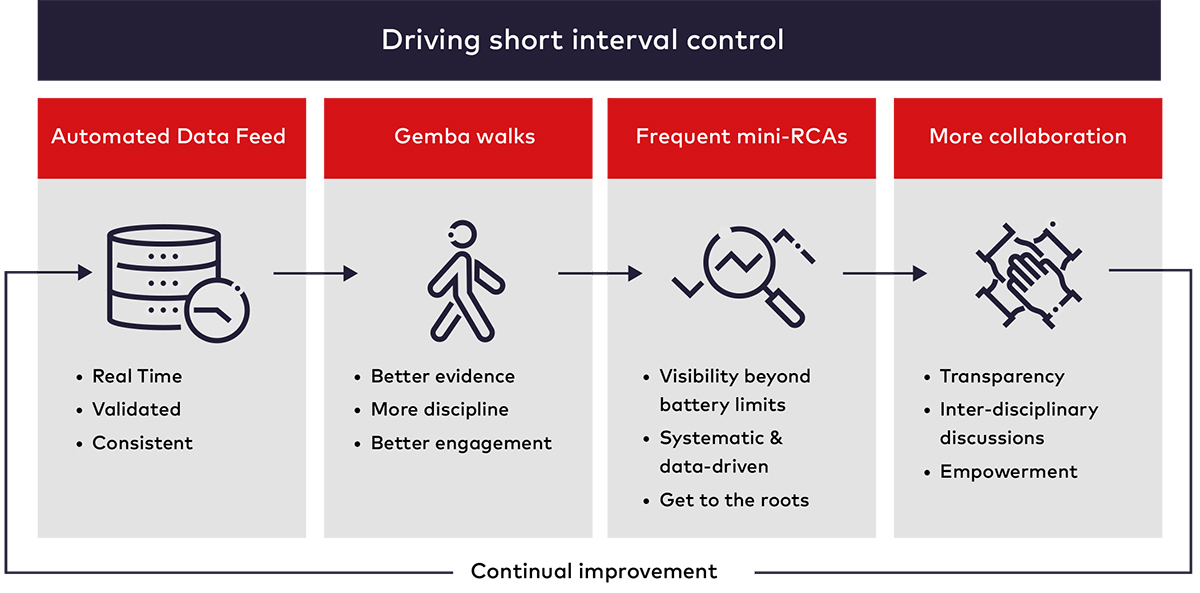
Figure 2: Driving short interval control through the PELA process
PELA considerations for the frontline
Since process operators are present 24/7, they are essential for tackling losses in real time. PELA helps them cut through large amounts of process data and focus on deviating performance. It enables shift staff to recognise and address certain problems early on. In this way, PELA supports the important continual improvement principle of Short Interval Control; a frontline process for minimising losses by quick intervention (figure 2).
PELA supports frontline teams, by:
- Alerting them timeously to relevant losses.
For this, it is important that the tools are customised with knowledge of operational processes, energy-related performance goals and time constraints and that information is presented in an accessible and user-friendly way. - Providing an intuitive and efficient way to record the cause of losses
The PELA frontline tool lets shift supervisors select cause categories via carefully designed drop-down lists that capture the location of the loss, its standardised causes, and equipment involved. Formal root-cause analysis is carried out at a later stage. - Embedding routines to update the PELA system multiple times every shift
The system’s benefits are clearly boosted by speedy reactions and cause categorisation. Incentives are provided to encourage timely checks and establish good routines. The system also tracks compliance to cause categorisation requirements.
Role of PELA in data-driven decision-making
Whereas frontline teams need instantaneous information and alerts, interdisciplinary engineering teams require trends and comparisons between different assets to identify serial poor performers, discuss potential improvements, and prioritise plans. They use the aggregated frontline data in regular PELA meetings to reduce losses over time.
PELA’s automated aggregation of frontline data and cause entries requires minimal effort and is essential for its effectiveness. The automation combines, orders, and presents data such that losses are not only visible, but put into context to facilitate discussions and clear action points.
Beyond operational excellence: PELA for business case definition
PELA serves as a vehicle for change by driving awareness of frontline staff and ensuring better cooperation between them and process engineers, maintenance, and production planning teams. The success of implementing PELA relies on lean skills, analytical capabilities, expertise in change management, and strong leadership within the line.
Our PELA approach is versatile and can be integrated into any production management system. With its ability to convey and record real-time financial losses, PELA supports frontline interventions, cross-departmental process improvements, and decision makers to drive key initiatives and capital projects, especially related to energy efficiency and environmental goals.
CASE STUDY: Implementation of PELA at an Oil & Gas client
Our client wanted to maximise the value of some of its key assets: three oil refineries, one petrochemical plant and two utility plants for power and steam generation. To start, we identified operations, maintenance and supply chain as three areas with notable addressable inefficiencies. Within operations, energy and utilities efficiency both showed significant performance gaps. Underperforming power and steam generation assets and inefficient energy-consuming equipment had created a gap worth US$ 30 million.
Developed by dss⁺ consultants, the PELA system was implemented to help shrink this gap. Using automatically derived real-time loss information, shift supervisors could check and comment on plant performance every three hours during their shift.
Underperforming power and steam generation assets and inefficient energy-consuming equipment had created a gap worth US$30 million.
For the client, the bespoke PELA implementation successfully covered 21 separate process areas. Across three sites, 100+ technical staff received training and a weekly meeting cadence was established for interdisciplinary teams to achieve maximum benefit from the initiative (Figure 3).
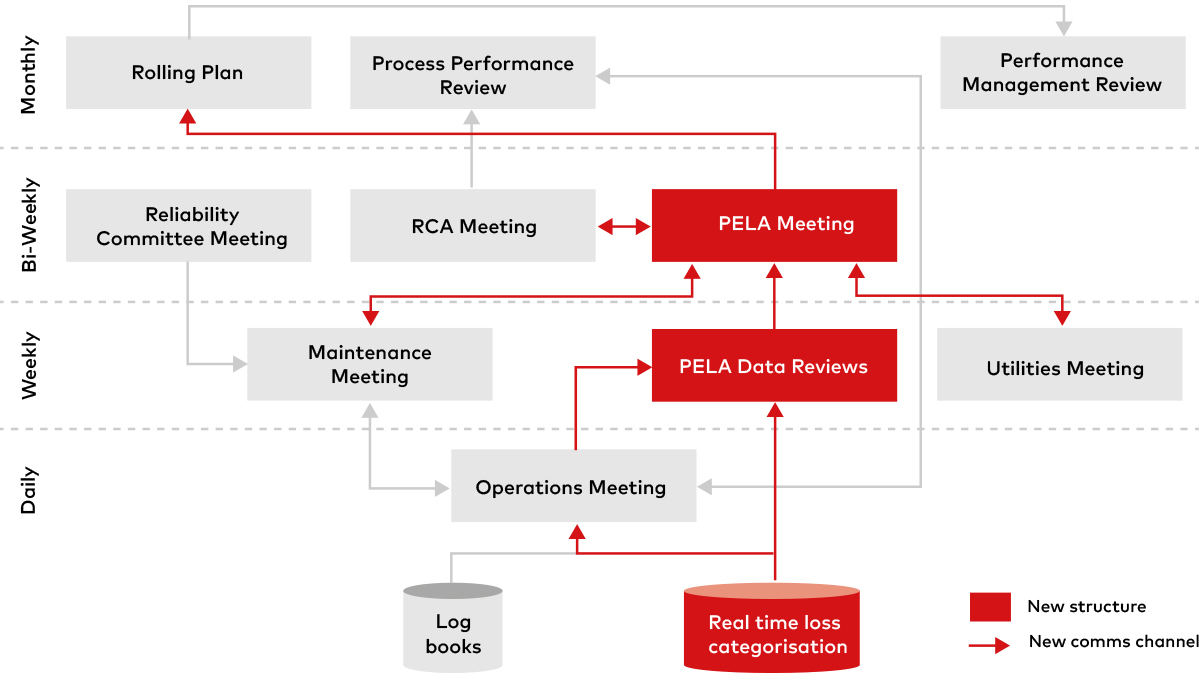
Figure 3: An example of a revised communications flow structure to embed PELA
The Energy module of the PELA tool tracks losses due to boiler efficiencies, various aspects of co-generation performance, cooling water losses, and flaring.
Shortly after implementation, PELA began to turn the dial on performance. With more staff engaged and empowered to make a difference, their voices became better heard and valued. The tailored software tools benefitted from their early feedback.
After only a few months of implementation, the system delivered notable qualitative benefits for this client, including:
- Improvements to process data quality, by addressing suspect metering;
- Attention to new types of losses and their associated monetary values;
- A better way to tackle losses through faster response times and important cross-departmental discussions;
- A structured process for managing operational excellence initiatives and for reducing energy consumption.
In numbers, the following results were achieved:
- 300+ production initiatives were identified thanks to the PELA process
- Energy costs were reduced by 5%
Since implementation, PELA continues to be used by the client to improve on their operational excellence and will be an essential part of driving further operational improvements and financial savings.