Developing Interlock Test Procedures to Reduce Risk
One of the largest mining companies in the world wanted to improve risk management by enhancing the reliability of safety controls at its operation sites. Doing so would elevate confidence in all key systems when faced with a potential emergency.
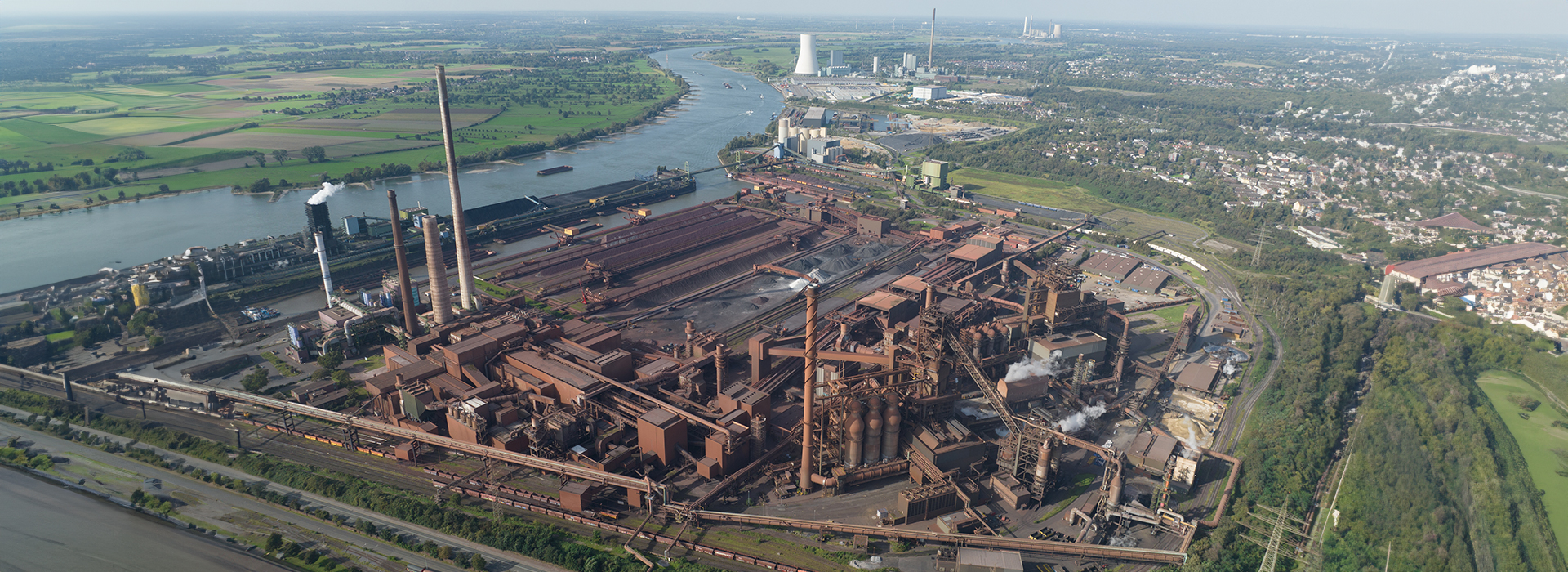
Challenge
One of the largest mining companies in the world wanted to improve risk management by improving the reliability of safety controls at its operation sites. The company had already identified key critical safety interlocks, or controls, at each site that would help prevent or mitigate a potential incident. The challenge is to be able to test the interlock on a regular basis without shutting down the operation, because any incident could lead to catastrophic loss and disruption. That means the need to develop test procedures for all critical interlocks, that could be completed within regular maintenance cycles. Doing so would elevate confidence in all key systems when faced with a potential emergency.
dss+ Approach
The dss+ team first created a database to capture information about the interlocks such as existing maintenance practices. Following that the team interviewed frontline workers and assessed the levels of risk awareness and maintenance reliability. Based on the information gathered at that point, the next step was the development of a functional test procedure. The client verified it could be performed with accuracy and completed within regular maintenance cycles. Revisions followed until the test procedures were finalized and secure.
The company gained functional test procedures for all key critical controls that were identified. This included testing conditions, safety requirements, and detailed instructions, all of which could be completed within regular maintenance cycles.
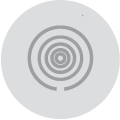
Assignment
To develop functional test procedures for all critical interlocks with minimal impact on the processes.
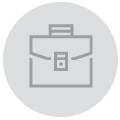
Offering
Operational Risk Management Consulting
Process Safety Management
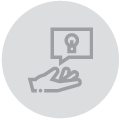
Impact
- The development and implementation of functional testing procedures have been developed for more than 25 key critical controls.