Contractor Safety in FMCG
FMCG companies are facing multiple concurrent challenges. Against these varied socio-economic pressures, organisations should not ignore those business levers than can more easily regulate: contractor risk is one of them. Mismanaged, contractors could negatively impact your duty of care, your production schedule and outputs, your own company culture, as well as your brands. Read on for some advice on how to minimise contractor risk, for the safety of all involved on your sites.
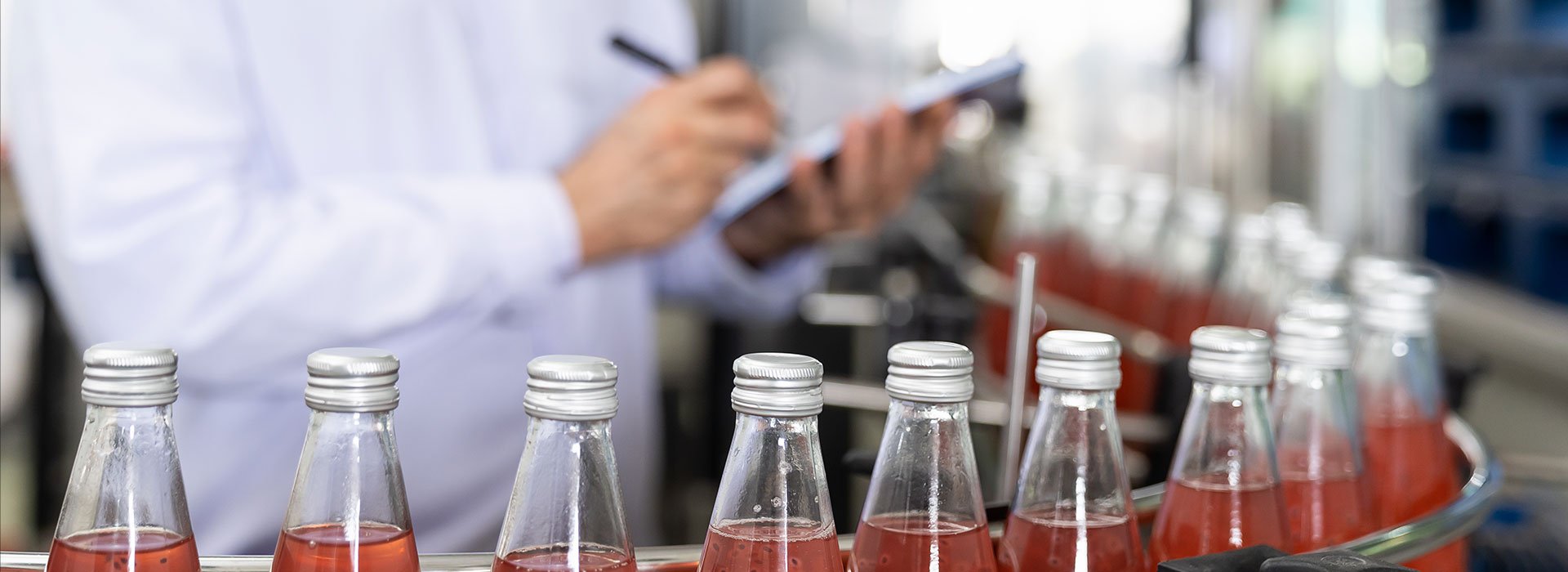
Contractors impact your company's safety
How to manage the associated risk
Against these societal and economy-wide pressures, organisations should not ignore those business levers they can more easily control.
Like many other industry sectors, FMCG companies rely on multiple contractors, for varied reasons - from the punctual such as filling in a temporary resourcing gap, to multi-year contracts that address a need outside of their core area of expertise.
By and large, these outsourcing arrangements are deemed successful if the technical task is performed to specification and within budget. Safety oversight tends to be minimal.
This raises multiple issues, as this approach compromises:
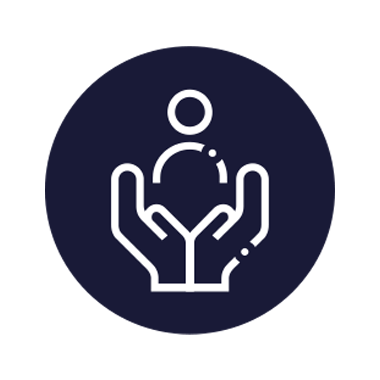
Your duty of care
By failing to keep active oversight of a contractor's safety practices, companies fail in their duty of care to those who operate on their site. In any case, even taking on a narrow view, an incident involving a contractor could very easily impact your own employee.
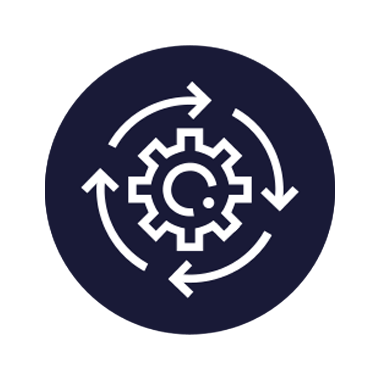
Your production schedule and outputs
In serious safety cases, it would not be unusual for a site to be closed, pending investigation and the introduction of corrective actions. The inherent cost to your company can be consequential.
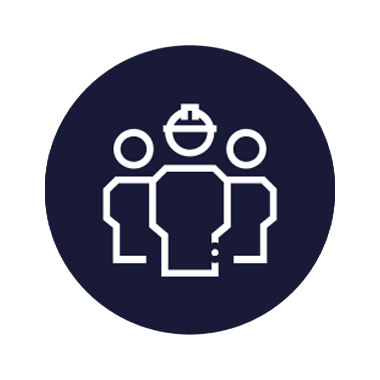
Your own company culture
When a contractor's employees are on your sites regularly, their practices and mindsets influence that of your own employees. If they see corners cut consistently without the third party being called on it, they will themselves start cutting corners. Your safety culture will slowly deteriorate, leading to increased numbers of near misses, or worse.
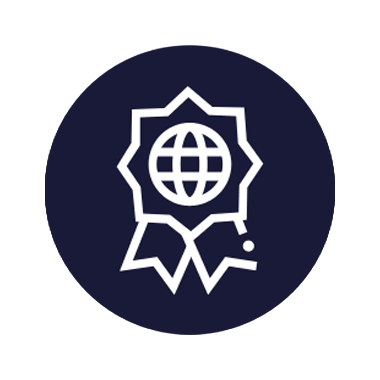
Your brand
When a serious incident or a fatality occurs, public commentary will link the event to your own high-profile brand, not to the contractor's.
Managing your contractors efficiently to decrease your safety risk
What can companies do to make sure safety expectations for contractors are consistently applied?
We recommend a proactive, ongoing approach which integrates the contractors - whether they be short or long term - as an integral partner to help you realise your Zero Harm objectives.
It is essential that Operations be involved in the definition of the scope as well as in the negotiations and agreement.
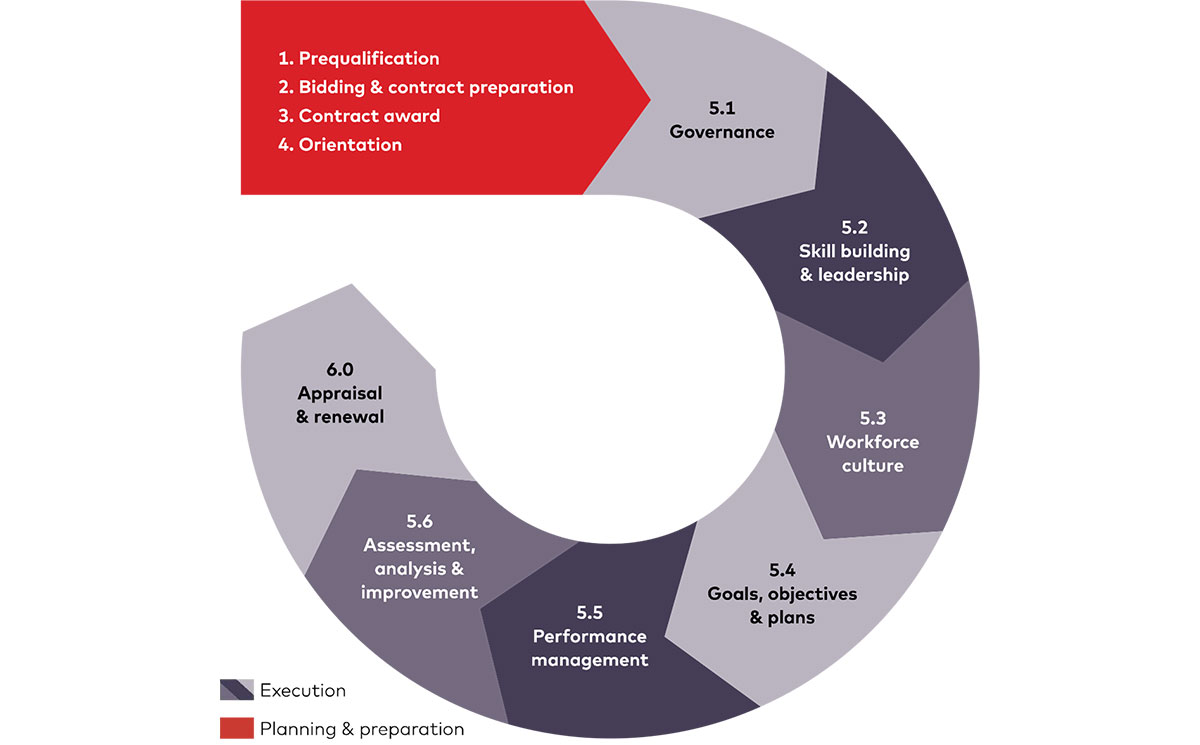
Effective selection process
Mitigating your safety risk starts with an effective contractor management system. This is critical for making informed decisions about which contractor to select for specific jobs.
The first stage of this system involves defining the task the contractor will be required to perform, and their associated risks. When developing requests for proposals, do not focus solely on technical outputs and financial considerations. Make sure to clearly lay out your safety expectations, and assess responses according to these criteria - with the understanding this will, and should, have an impact on the financial proposal. When a full request for proposal process is not feasible, proceed with a pre-screening to gain an insight into the contractor's levels of training, performance and safety.
If question marks remain with regards to the level of safety sophistication of an otherwise exemplary candidate, having this advance knowledge will allow for a proactive approach - early actions can be taken to mitigate and manage the risk. In addition, often procurement departments oversee the selection process with limited, punctual input from the department which will interact the most with the contractor. In extreme cases, the procurement department will not have visited the site where the contractor will be assigned, and scopes of work will not reflect the practical realities of the operations.
Contract initiation: make it clear safety is non-negotiable
Having clearly laid out during the proposal process that you view safety as a non-negotiable aspect of your company's operations, make sure to reiterate this message from the get-go; from the moment a contractor is appointed and every time a new member of the contractor's team starts on your site.
Of course, your commitment to safety will be demonstrated by your actions over time. This should start at onboarding. For a food and/or beverage manufacturing site for example, this could include a safety induction at the gate as well as a detailed introduction to the equipment the contractor will work on. In warehouses, the initial briefing will pay particular attention to movement with and around forklift trucks which are involved in multiple fatalities across the industry.
Being clear from the outset will go a long way towards establishing how the contractor embraces the safety protocols specific to your organisation, and contribute to an effective workplace where both employees and contractors do not fear being injured.
A strong safety culture is your strongest ally
Protocols alone are not enough, as safety cannot be a "bolt-on" to a contract. Whilst we don't deny that various numerical metrics will play a part in assessing each contractor's safety performance, ultimately, your culture will be the biggest driver of positive safety outcomes in your organisation.
Safety culture is a way of thinking, behaving and working, individually and as a group. It enhances risk awareness and reduces the chance of harmful and dangerous situations - and it should encompass your contractors.
The dss+ Bradley Curve™ illustrates our more than 50 year-research and experience in this field. It highlights that injury rates are higher if individuals are micro-managed and only told about rules to follow, whereas injury rates are lower when people feel genuinely cared for and listened to by their managers. In the latter case, they want to contribute positively.
This emphasis on cultural development works especially well with the long-term contractors who can be made to feel part of the team and included in idea generation and improvement activities. Whilst short-term contractors are different, they will still experience an active safety culture when they are on site.
In practical terms, it is about supporting contractors to be safe and work safely - which in turn will have a positive impact on your company's overall safety culture.
Your culture will be the biggest driver of positive safety outcomes, and it should encompass your contractors.
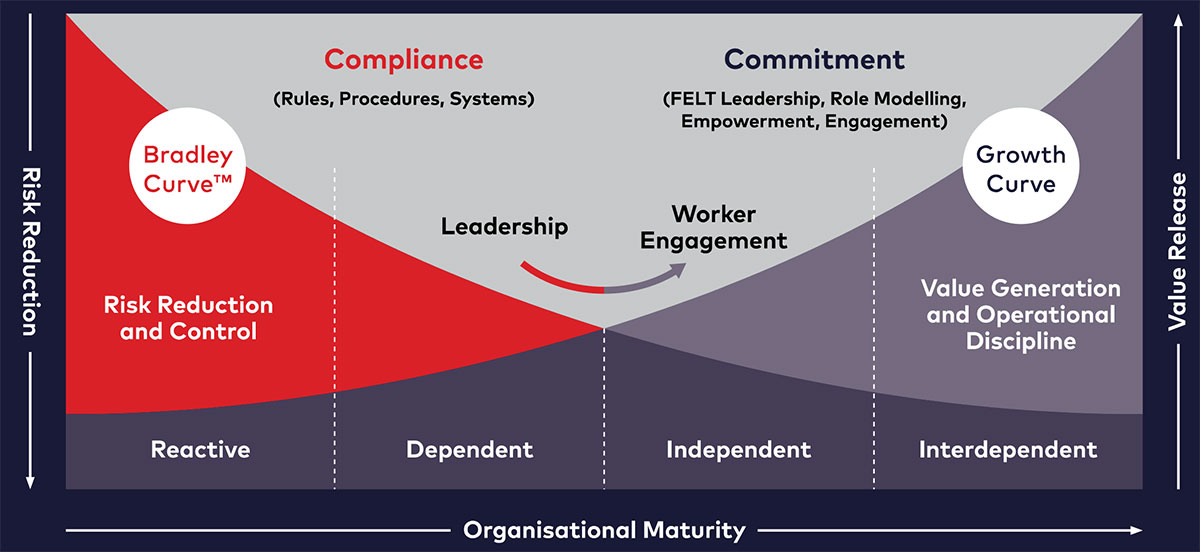
3 actions to minimise your contractor safety risk
Effectively communicate safety expectations to contractors during the contract award process.
Clearly state the contract safety requirements and reach an understanding on safety issues, including at shop floor level. Integrate safety as part of your RFP assessment process.
Engage contractors on safety culture.
Talk about the risks, have a discussion. Check they are well-equipped for the job and the conditions. Encourage an open line of discussion.
Evaluate to help manage future risks.
A contractor management system is only robust if it is used systematically. Post-contract evaluations are vital to provide the selection insights for future contracts.
Contributing to this paper were:
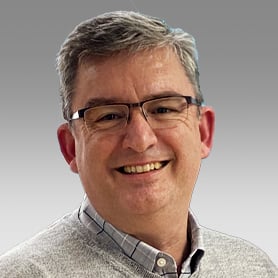
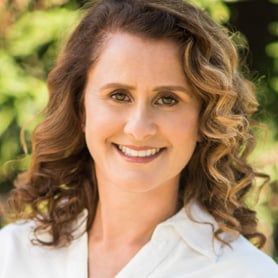
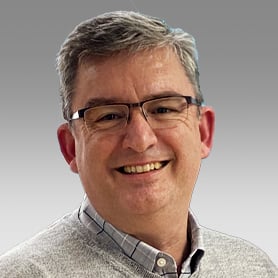
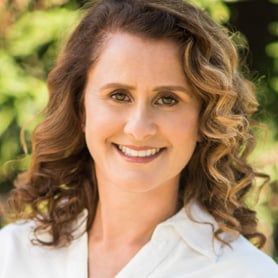