Assessing safety culture and setting foundation for continuous improvement at All4Labels
All4Labels is one of the world‘s top label manufacturers and a leading provider of digital printing solutions, focussing on home, personal care as well as food and beverage markets.
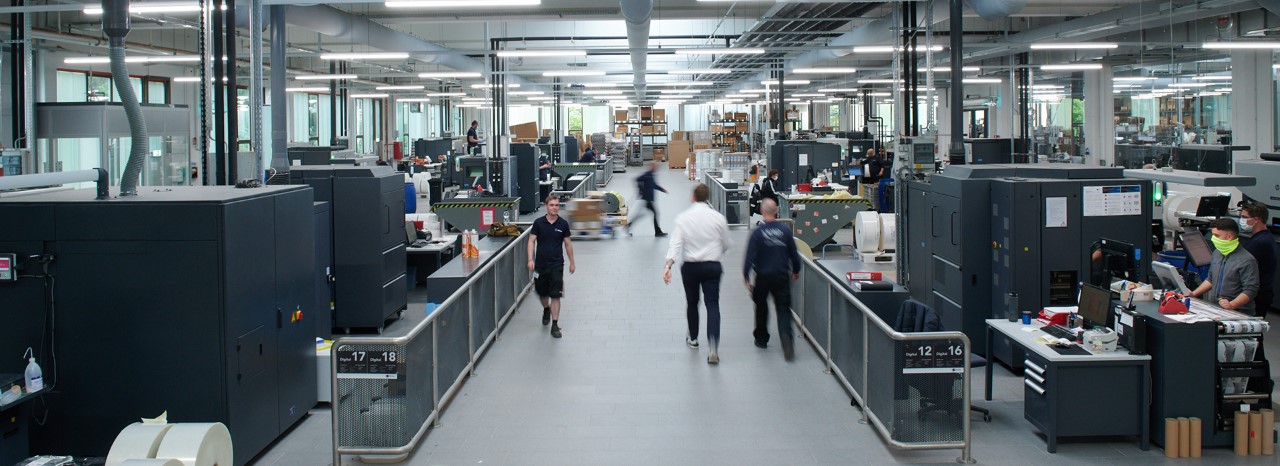
Background & challenge
All4Labels wanted to understand the maturity level of its safety culture to identify strengths and opportunities on a global scale. The company partnered with dss+ to understand cultural and regional differences in the maturity of the safety culture. All4Labels aims to utilise these insights to tailor new safety initiatives and programs, in order to continuously improve their safety performance and become a benchmark in the industry.
Systematic approach & sustainable solutions
dss+ and All4Labels deployed the dss+ Safety Perception Survey™ (SPS) in 10 local languages, across 30 sites. SPS and dss Bradley Curve™ identified how the global workforce perceived safety culture and benchmarked All4Labels in the industry. Results across global and regional sites helped to define the most prominent development areas and levers to take safety to the next level to pursue excellence. Results and next steps were defined during dedicated Safety Cluster Workshops, gaining leadership commitment on shared objectives and action plans. All4Labels now benefit from a firm ground to determine and address future development needs to further improve their global Behavioural-Based Safety program to make All4Lables the safest labeling and packaging company for the employees, and to have a positive impact across the communities, the environment and the industry.
“At All4Labels we always prioritise people’s health and wellbeing; therefore, we are placing a strong emphasis on behaviour-based safety and leadership. We want to be the pioneers in occupational health and safety in our industry, and we have deployed the dss+ Sustainable Safety Approach to tailor our global activities to respond even better to the needs of our colleagues.”
Fabian Grimm, Global Safety Coordinator,
All4Labels Project Lead