PhosAgro
PhosAgro Group is a Russian vertically integrated company and one of the world’s leading producers of phosphate-based fertilisers. Improving employees' quality of life and working conditions is a high priority issue on the company's social agenda. In 2014, targeted work was carried out in the field with experts from dss+ as part of an eight-month project to improve the company's health and safety management system and reduce the accident rate.
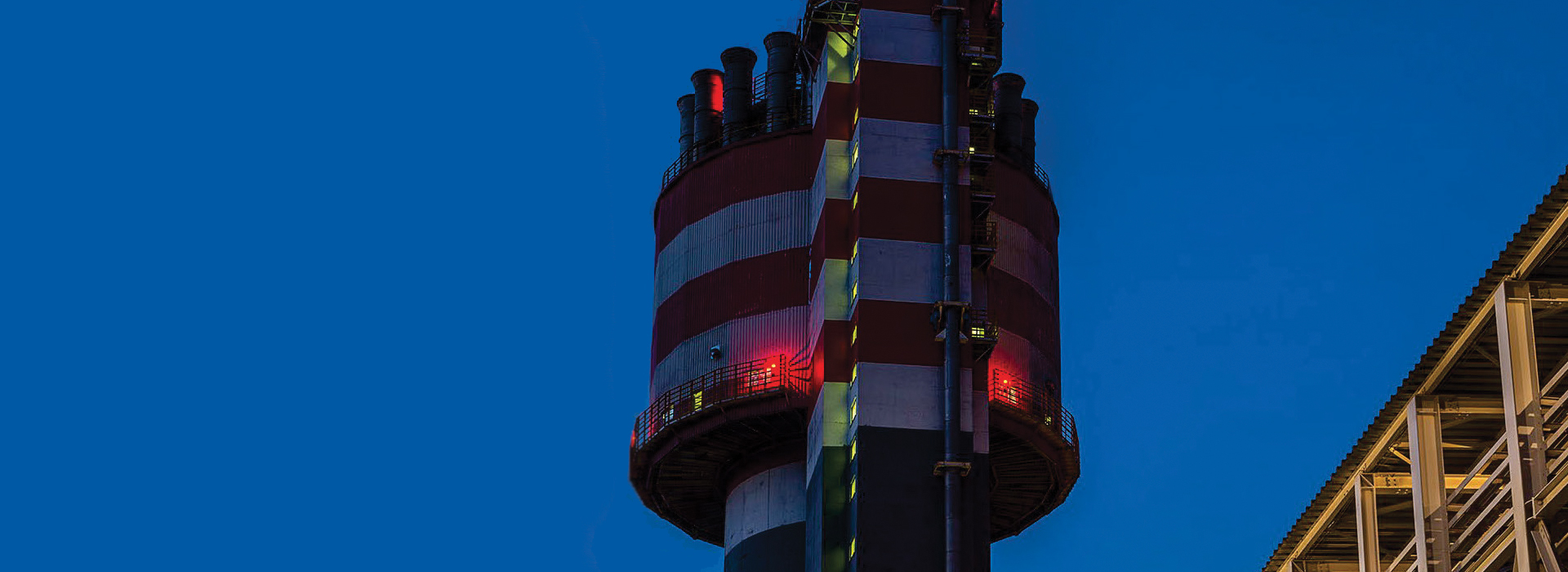
Improvement of the Corporate Health and Safety Management System at all PhosAgro Companies
In view of such a short time frame, the dss+ team faced rather ambitious tasks: developing the safety management capability and skills of personnel working in selected pilot divisions at each of the four PhosAgro Group companies; introducing advanced management tools aimed at injury and accident prevention; achieving “quick wins” related to the reduction of the injury rate by eliminating hazards and the root causes for accidents; as well as establishing an in-house trainer team to further expand the safety management competence in other divisions of PhosAgro Group companies.
Having conducted a thorough diagnostic of the existing safety management system, dss+ experts noted areas in which the company was clearly successful. Top management, consisting of professionals with personal production experience, was ready to solve open safety issues. That was of great value. Nevertheless, there were some areas where processes needed improving. One of them was related to the introduction or upgrading of such procedures as behavioural safety audits, accident investigation, establishment of an integrated safety management structure, development of communications in the field and, of course, training activities.
dss+ tailored the focus of its work to address exactly these aspects. Its experts developed standards along with a regulatory and procedural framework intended to help implement injury prevention practices. In doing so, the team relied on world best practices and its own experience at dss+. The consultants improved the existing personnel motivation system, conducted training for 1,000 employees under the specially set up programme and prepared 26 in-house trainers so they could later help to develop the safety management skills of line managers. The introduction of new standards at production sites was mainly based upon practical guidance/mentorship at the work place and on regular conformity checks.
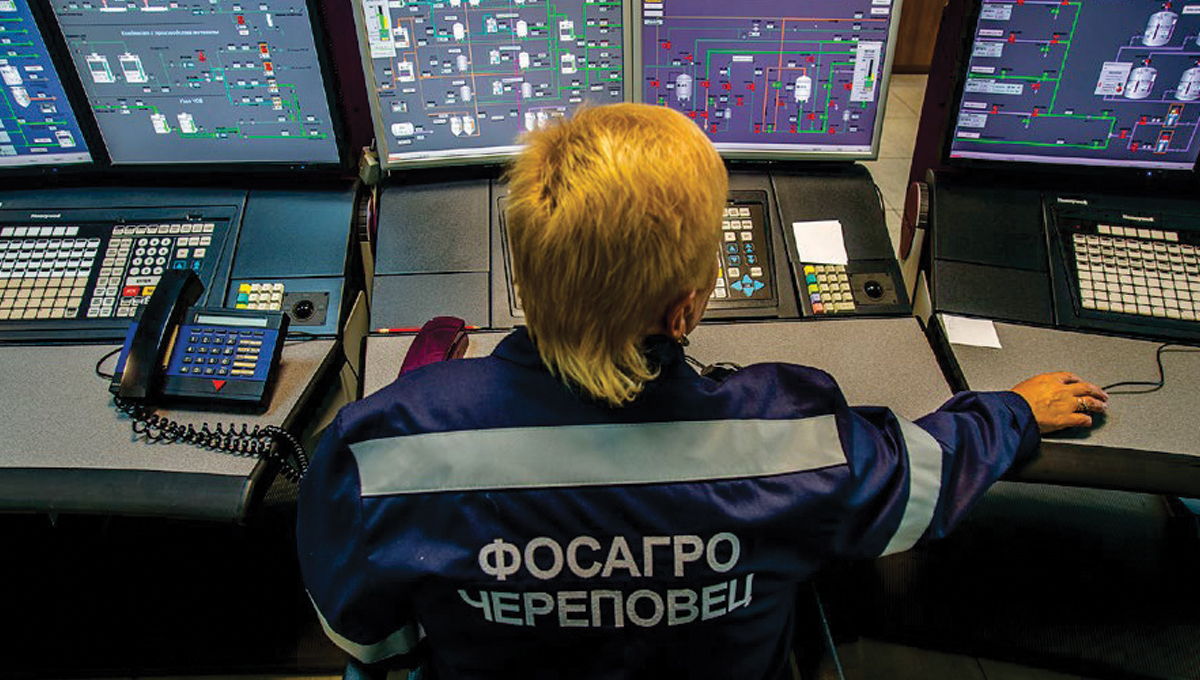
Fast results
The work carried out raised the employees’ awareness of the safety issues’ importance and enhanced their motivation and level of involvement into safety system improvement activities. As a result, the total number of unsafe behaviour cases and hazardous situations fell by 37 percent. The new system of behavioural safety audits helped to reveal and eliminate more than 1,000 hazardous situations and the planned reduction of the accident frequency rate was achieved by identifying root causes and introducing corrective measures based on investigation results. The activities carried out helped to bring the company’s safety culture level up by five percent, marking the first step towards the transformation of the company employees’ mind-set. As a consequence, in 2014 the accident frequency rate was cut by eight percent. Now, the company is putting in place the foundations for the final stages of implementing the safety improvement project started by dss+. This last step will be conducted by PhosAgro unassisted and will require wider involvement of the personnel at production sites along with efficient internal supervision in order to obtain a sustainable result in the future. But dss+ has coached PhosAgro staff to enable them to promote safety independently and the company looks forward to seeing further safety improvements over the coming months.