Successfully Managing a Changing Workforce
Many companies around the globe are faced with the difficult challenge of managing workforce change in a time when budgets are tight, pressures to decrease costs and improve productivity are high, and there is still an expectation to maintain safe operations. This is not a new challenge, but workforce changes are even more complex than in the past.
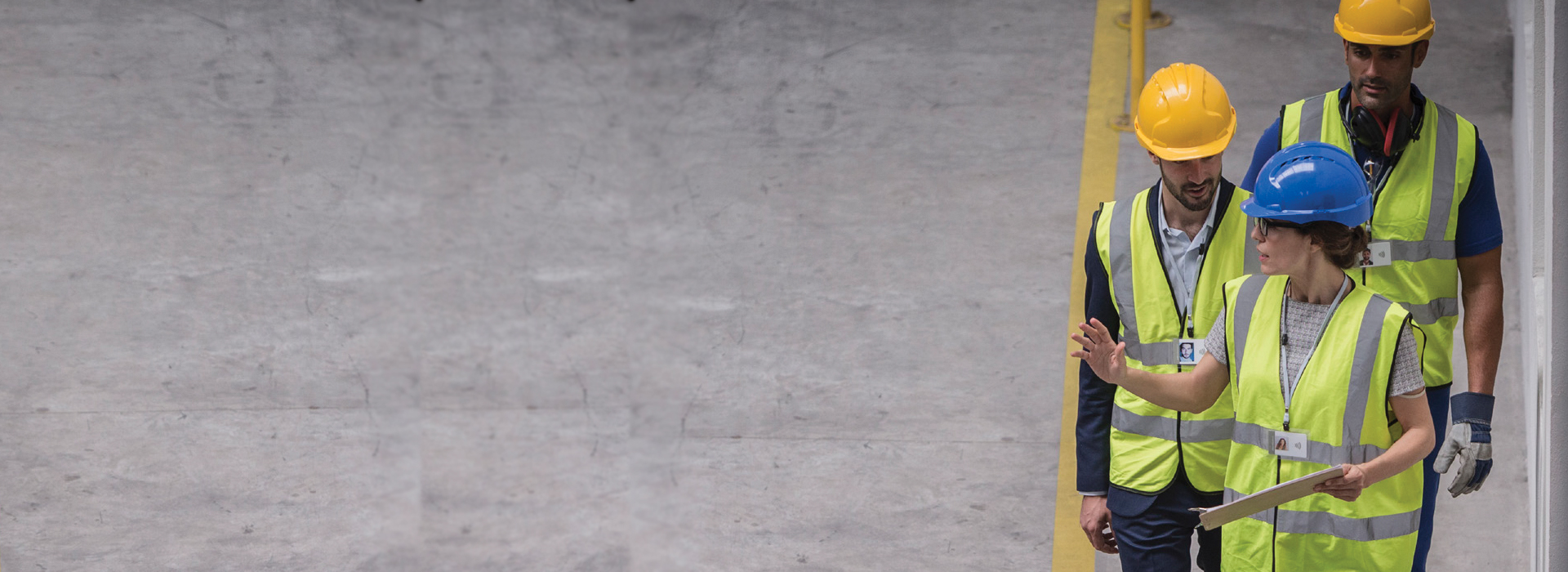
Successfully Managing a Changing Workforce– Application to Process Safety Management
Introduction
The Channel Industries Mutual Aid (CIMA) is a cooperative organization of over 100 emergency response agencies in the Texas counties of Harris, Chambers, and Brazoria and industrial fire departments from the petrochemical, chemical, and refining operations. They were formed in 1955 under the name of Ship Channel Industries Disaster Aid Organization. They have 60 years' worth of serious industrial accident records. The head of CIMA believes the single most significant factor in incident increases is when the workforce changes as a result of new processes and major shutdowns.
In today's environment, companies have much more sophisticated technologies and streamlined supply chains, and mistakes can have severe consequences. The problems are compounded by the fact that many companies have a large number of retirees, a large number of new employees entering the workforce for the first time, and few in the middle.
New engineers entering the workforce today have an extraordinarily broad range of skills. Successful companies will take advantage of what these new employees bring by changing work processes to be increasingly efficient and productive, while still utilizing the experiences of the more senior workforce.
dss+ has identified a multi-part process to help companies thrive in this time of workforce change. This paper will explore key characteristics of new employees entering the workforce today and will outline the steps developed at dss+ to meet the needs of this new type of employee. The goal of these changes is to ultimately provide a suitable working environment and improve employee retention which will have the added benefit of improving process safety performance.
Managing Highly Hazardous Operations
Successful safe operations in high hazards process industries require talented engineers with a broad range of skills and experience. This includes chemical, mechanical, instrument, and electrical engineers who are involved in conception, design, construction, and operations. They build and modify facilities, and keep the plants running efficiently and safely. They work on longer-range problems to implement safety, cost, and capacity improvements. Most operations run around the clock, 24/7, 365 days per year, occasionally interrupted by breakdowns in equipment. Because of this, engineers that support operations need to be available at all times to assist in the resolution of problems. Engineers plan and execute the maintenance and inspection programs. They are doing this today with fewer people, tighter budgets, and greater demands for production. Workforce changes, whether a result of retirements, transfers, leaving for better opportunities, or other reasons can put a great strain on the remaining workforce, and on the new people on the job.
Manufacturing operations have always required personnel with skills, experience, and the much more elusive and difficult to define characteristic, wisdom, which couples skill and experience with good judgement. Engineers learn their basic skills in college, refine and expand them in industry, and add new experiences along the way. Experience and wisdom can reside anywhere in the organization, in practising engineers, line management, and also in the operators and their supervision. Experience is gained not only from direct operational experience but also from incidents that have occurred in related companies and industries. People in the workforce who combine their experiences with a sense that hazardous events can happen in their operations bring sound judgement. They continuously seek to avoid events that can have bad consequences.
The role of immediate supervisor to new engineers is critical. Much has been made in recent years of the need to achieve a work-life balance. Many millennials, or generation Y (those born from the mid-1980s to the mid-1990s), achieve a work-life blend, where one is not entirely separate from the other. Technology allows employees to work anywhere, anytime. The impact of this is that people will need to be judged by performance, not presence.
Skills and Qualities of Engineers who have Recently Entered the Workforce
There is a lot of information on the generational traits of millennials. However, it is wise to not assume that all entering engineers have these qualities, as there are significant differences between individuals. With that caveat, let's look at some of the more important traits that can impact a millennial's process safety management (PSM) performance. Some of these may be considered positive aspects, and some negative.
General Traits of Millennials 1
Tech Savvy
Smartphones, tablets, email, text messaging, Twitter, Facebook, LinkedIn and whatever new comes along is candy for engineers. They use these devices and tools to stay in continuous communication with each other with little distinction between personal and work life. They prefer these forms of electronic communication versus phone calls and face-to-face. Printed materials are avoided wherever possible. While previous generations may feel something is lost with mostly electronic interaction, millennials have been educated using electronic tools and can use them while maintaining a personal touch. With these tools, they can work anywhere, anytime. For example, a parent needs to leave at 3 to pick a child up at daycare, but after 8, when children are in bed, the parent works until 11 and communicates with others who are connected electronically.
Family-Centric
"Generation Y have a different vision of workplace expectations and prioritize family over work." This can create some difficulties for an engineer in manufacturing operations. Shift cover for start-ups and other operating problems can greatly interfere with family life. Many married engineers from two-working-parent families or who are single parents demand flexible work schedules. Many companies have adjusted to this by incorporating core work hours, such as 9 to 3, where all employees are present. Achievement Oriented "Generation Y wants meaningful work and a solid learning curve." They want these good assignments to gain experience as well as a reputation for getting the job done. In particular, the first assignment is critical if a company hopes to retain talent. There is also an expectation of promotions.
Team Oriented
"They value teamwork and seek input and affirmation of others." They have been involved in team activities their whole lives, from sports to an educational process that involves working together to solve complex engineering problems.
Attention Craving
"Generation Y craves attention in the forms of feedback and guidance. They appreciate being kept in the loop and seek frequent praise and reassurance." This can be a problem for supervisors heading an organization with a very large number of engineers versus previous generations.
Some misconceptions about millennials are that they are spoiled, immature, and lazy. These are character traits of individuals, not a generation. Many millennials are highly motivated and expect to move up rapidly in an organization.
Generation Z
The millennials, or Generation Y, are generally thought of as being born between the mid-80s to the mid-90s. After the millennials comes Generation Z, those born after 1995. They are only now beginning to enter the workforce and will have some general characteristics that distinguish them from the millennials. Laura Montini (2) gave some characteristics of generation z. They prefer person-to-person interaction and they come to the workforce well prepared. Both generations Y and Z say honesty is the most important quality of a good leader.
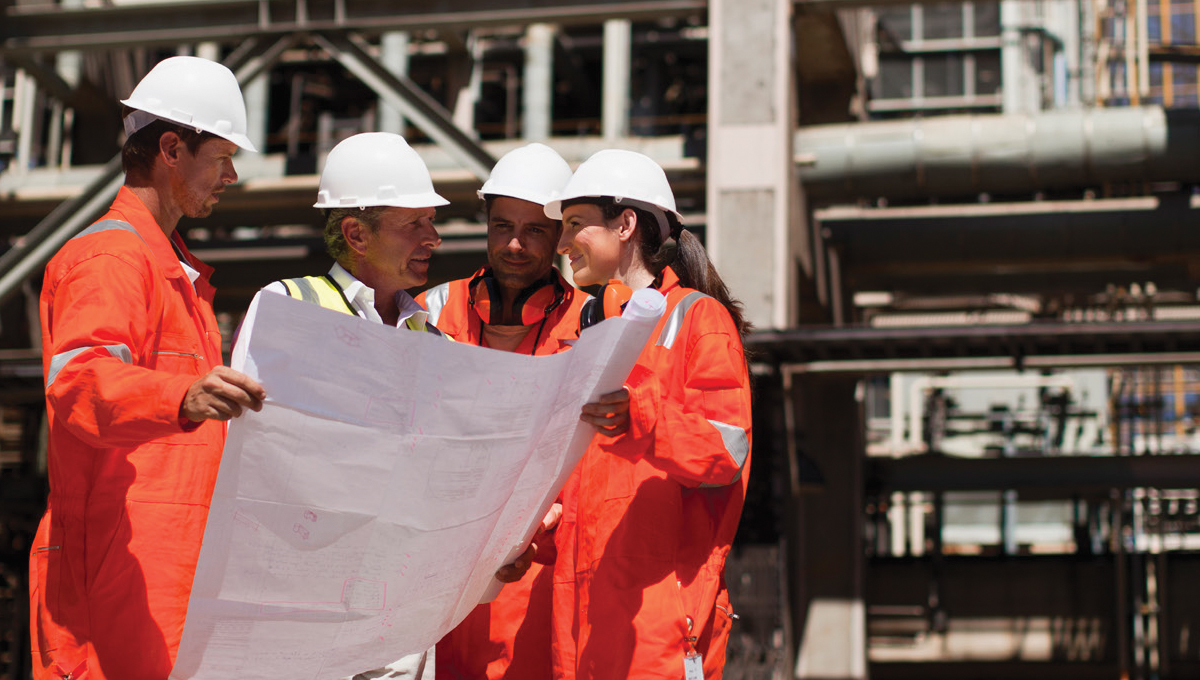
Integrating New Engineers into High Hazards Operations
The large number of new engineers entering the workforce makes it a challenge to continue safe operations. Faced with this challenge, a small cross-generational group in dss+ was identified with the purpose of defining the keys to the successful integration of new employees into high-hazard operations. The objective was to develop a process that could be used with minimal changes for engineers entering the workforce. The process starts with understanding what is important to the engineers and the company, then moves to identify action items, and finally developing and implementing plans.
A six-sigma process to identify key areas, and develop the CTQ (items critical to quality) and the CTXs (a factor that impacts the CTQ) was used. Initially, six key areas were identified and developed. This was later expanded to eight. Most of these areas were drawn from practices at dss+ sites
1. Critical functions and skills need to be identified
This step identifies not only the functions and skills for today, but seeks those required in the future to assure competitiveness. There is clarity in what is done internally, and what is outsourced. This also includes the identification of "Technology Guardians." Technology Guardians are senior technical employees who oversee a wide range of activities over a single or group of processes for a long period of time. They help assure continued safe operation. For example, this includes a review of all proposed changes within a given process. The career development of a guardian is critical. In some cases, this is accomplished by providing gradually expanding responsibilities to cover multiple facilities or additional processes.
2. Individual Competency Development Plans
These plans help assure the growth of all personnel but can go a long way in retaining individuals that are necessary for future success. It is important that development plans meet the need of the company as well as individuals.
3. Succession Planning for all Critical Positions
(note: identification of critical positions is the first step in the process to manage a changing workforce. For example, in PSM, a PHA leader would be a critical position.)
These are up to five-year projections of new hires, promotions, reassignments, and retirements. These plans need to be periodically reviewed with senior management.
4. Knowledge Transfer Management
Leveraging experienced personnel is necessary through assignment, coaching, and mentoring, along with the development of technical databases that can be easily accessed.
5. Use of Blended Learning Approaches
Individual training plans are developed, and personnel are encouraged to participate in internal and external opportunities. Modern training methods include less lecturing, and more doing.
6. Cultivate Learning Communities
Leadership is strong in driving the involvement of engineers in internal and external networks.
7. On-Boarding Process for New Employees
The onboarding process is critical to the success of new employees. Two key factors in this are assigning challenging and meaningful initial assignments and using a mentorship program.
8. Cultural Environment
This is a multi-faceted subject that can require a company to evolve to take advantage of the workforce skills and expectations of employees entering the workforce for the first time. Examples include an environment that is sensitive to the needs of women, promoting teamwork for problem-solving, and valuing speed in implementation. For instance, a company has an older phone system that doesn't pick up a woman's higher-pitched voice, or the company does not allow employees to work from home when needed, such as caring for a sick child. Maternity leave also continues to be an important subject.
Below is an example of some of the CTXs for the initial onboarding of a new employee. These are given in the form of questions that an organization can use to gain feedback from their new employees and their supervisor.
On-Boarding
Questions for the new employee:
- What are your thoughts on your first assignment? Is it an important assignment? Is having an important assignment necessary or critical to you?
- Have others in the organization been identified to help you with your assignments? Does this include both senior and junior people other than your direct supervision?
- Do you feel there is there a high probability of success?
Questions for the new employee:
- Will the new employee be given access to management to present findings?
- Will the first assignment give the opportunity to advance to more meaningful assignments?
- Will reward and recognition be provided?
Conclusions
With ongoing changes and the loss of process safety experience, organizations can be put under great stress. In particular, the direct supervisors of new employees will face the greatest challenges. Typically, start-ups of new facilities often require junior engineers to work shifts. This can range from a few days to weeks or even months, greatly disrupting the lives of engineers who may have more family obligations than previous generations. New engineers entering the workforce have less loyalty to an organization they hire as a result of company policy changes, the need for rapid promotion, and pay increases that may not meet their expectations. Increased span of control for a supervisor means less time with employees.
Sources
1. Generation Y. (2014, December 16). Retrieved from http://legalcareers.about.com/od/practicetips/a/GenerationY.htm
2. Montini, L. (2014, September 2) Generation Z: Meeting your future hires http://www.inc.com/lauramontini/meet-you-future-hires-5-characteristics-of-generation-z.html