Accelerating your ramp-up Safely, Reliably and Efficiently
Due to the COVID-19 pandemic, multiple organisations have had to shut down in a very abrupt manner. However, with restrictions easing up across the globe, they have been given an opportunity to either partially or fully restart their operations. Unfortunately, restarting operations can create certain risks that are new and different which can result in potential loss of life and catastrophic equipment damage. For this purpose, a structured risk-based approach using proven tools to secure operational readiness is now imperative, more than ever, to guarantee a safe, reliable and efficient ramp-up back to normal operations. Sufficient detailed operational readiness planning for your restart will result in both a decreased risk exposure and value erosion. As such, it is paramount that an organisation, aligned to its business and operational priorities, acts pre-emptively and efficiently in order to achieve sustained performance.
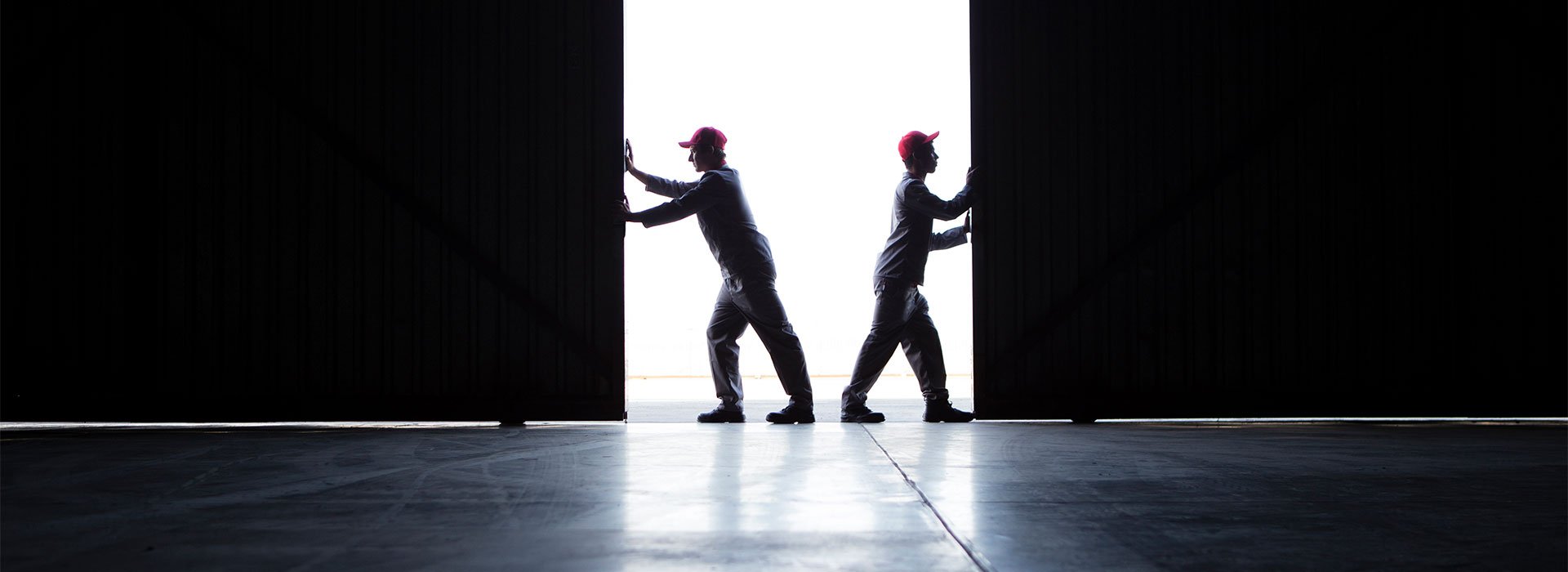
dss+ Operational Readiness Series
Common challenges observed across industries
With the escalation of the COVID-19 pandemic, the global economy is struggling to recover with a decrease in global production, an increase in global unemployment and an overall drop in GDP being felt around the world. These impacts are affecting a multitude of industries globally including aviation, automotive, hospitality and retail to name a few. Common challenges have emerged across many exposed sectors including:
Supply Chains – Changing local regulations, financial positions, fluctuating demand and supplier uncertainties are impacting supply chains. Domestic and international trade have flat-lined because of transportation restrictions and a decrease in placement of orders.
Employees – For safety and health reasons, most organisations have instructed all non-essential employees to socially distance themselves by working remotely or have special arrangements at site locations. Other companies have downsized their workforce to better EMPLOYEES manage cash flow. This results in stress, fatigue and general anxiety among employees.
Assets & Operations – Cash constraints and labour issues can subsequently lead to deferring maintenance activities on assets and placing capital projects on hold. This can cause inadequate risk and safety management on site.
Adopt an Operational Readiness mindset and skill set
With the infection curve flattening out and economies opening up, companies must adopt an Operational Readiness mindset, as well as corresponding skills and methodologies. The immediate priority with the onset of the pandemic has been to protect lives. However, it is now time for governments and industries to shift focus to rebuilding economies to ensure lives and livelihoods are protected. In fact, 23% of participants of a recent dss+ Operational Readiness webinar stated their companies are ready to resume operations and an additional 56% of companies have restarted and are focusing on ramping up operations over the next 6-18 months (Figure 1).
Which phase is your business currently operating in?
Poll Results (single answer requires):
Figure 1: Responses from June 9, 2020, dss+ webinar poll
To this day, there have been various discussions and opinions regarding the COVID response and business continuity, but what does it all mean from an operational standpoint? What does all of this mean to the average worker on the shop floor? And what do Operational Leaders need to know and do to ensure they can ramp up safely and reliably? Some of the new realities Operational Leaders are faced with include the following:
- How do we run our operations and maintain hygiene guidelines?
- How do we ensure our supply chain can support our ramp-up targets?
- What processes, procedures, and working arrangements will need to be modified and updated to reflect this new reality?
To ensure the new reality can be dealt with efficiently, Operational Readiness needs to become a core skill - quickly. The majority of the webinar audience (83%) have confirmed that their organisations have completed a detailed ramp-up plan, with 60% of the attendees recognizing the need to ramp-up immediately (Figure 2).
Which quadrant do you think your organisation is currently in relevant to COVID-19 impact on Ramp-up?
Poll Results (single answer requires):
Figure 2: Responses from June 9, 2020, dss+ webinar poll
So what does this all mean? From our experience in dss+, we look at a simple, practical approach and tool-kit which focuses on implementation. In this article, we want to share our experience in how to implement Operation Readiness in the field, while focusing on the highly impacted parts of your value chain and integrating that with your operational planning.
Insufficient planning results in increased risk exposure and eroded value
A poorly planned ramp-up will increase your level of risk exposure to incidents, and start-up following a period of inactivity has been known to bring about unexpected risks that are often missed. A study by the Center for Chemical Process Safety shows that process safety incidents are five (5) times more likely to occur during start-ups than in normal operations1. A similar study in the refining industry shows that 50 per cent of process safety incidents occur during start-ups, shutdowns, and other non-routine activities2. Accidents continue to happen as we struggle through the pandemic with a number of incidents coming to light with a variety of consequences.
Figure 3 shows how restarting operations without detailed readiness planning can lead to under performance relative to historical data. This can also result in increased operating costs, not having the capable personnel available at the right time and an interrupted supply chain. For example, it is important to focus on both the COVID-19 risks as well as the other key underlying operational risks, such as a shortage of staff on the floor compared to normal operations.
Therefore, investing in Operational Readiness planning and execution will reduce the likelihood that you will incur any opportunity costs and eroded value.
Figure 3: Poor Operational Readiness vs. Planned Performance value generation
Our Readiness to Operate (RTO) methodology helps ensure a safe, reliable & efficient ramp up
Restarting operations following the COVID-19 pandemic has added a layer of complexity due to the possibility of multiple waves of infection. Without proper planning and the regular evaluation of the resulting plan, a restart can pull organisational performance backwards. Through the implementation of a thoughtful, rational process, however, companies can successfully restart and ramp up operations while protecting employees.
Figure 4: 5 core areas of the dss+ Readiness-To-Operate methodology
Within dss+, we help our clients assess Readiness To Operate (RTO) through five key dimensions (Figure 4):
- Detailed and thorough planning for your physical assets including process flows and cleaning practices.
- Protecting the health of employees by complying to hygiene standards and managing people stress and fatigue.
- Ensuring a strong and resilient system by ensuring deployment of capabilities across the technical systems.
- Setting up for growth by integrating all aspects of the supply chain, incl. supply and demand.
- Finally, strong governance and open communication are essential to ensure the teams are aligned.
Proceed with a structured approach using proven tools The dss+ RTO framework ensures there is a focus on the key priorities to help ensure you put together a detailed ramp-up plan. But how do you operationalize this plan? Figure 5 shows the logic and key tools that can guide this process. Understanding where your key risks are, how to mitigate for them, and ensuring you resource the plan accurately will form the basis for the realisation of your ramp-up.
Figure 5: How to deliver a robust and integrated ramp-up plan
Finally, redeploy the required resources to achieve the readiness plan, as you cannot have this become part of the operation’s team day jobs. By having the right people dedicated and focused on the proper execution of these Operational Readiness activities, you will increase your potential for a successful ramp-up and sustained performance. You do not want to overload the operations team with these additional tasks, which can lead to safety and operational consequences. It is also important to have a sound governance and communication system established to keep the business aligned and working towards achieving the same goals.
SOURCES:
- CCPS. Guidelines for Safe Process Operations and Maintenance. 1995; p 113, citing Large Property Damage Losses in the Hydrocarbon-Chemical Industries. Marsh McLennan, 14th edition, New York, NY, 1992
- Otrowski, S.W.; Keim, K.K. Tame Your Transient Operations: Use a special method to identify and address potential hazards. [Online]. July 23, 2010