Nathalie Ponzevera: An honest company culture
With passion for defining strategic issues and implementing solutions, Nathalie Ponzevera uses her extensive management experience to drive safety and performance by creating a culture that is open, honest, and celebrated.
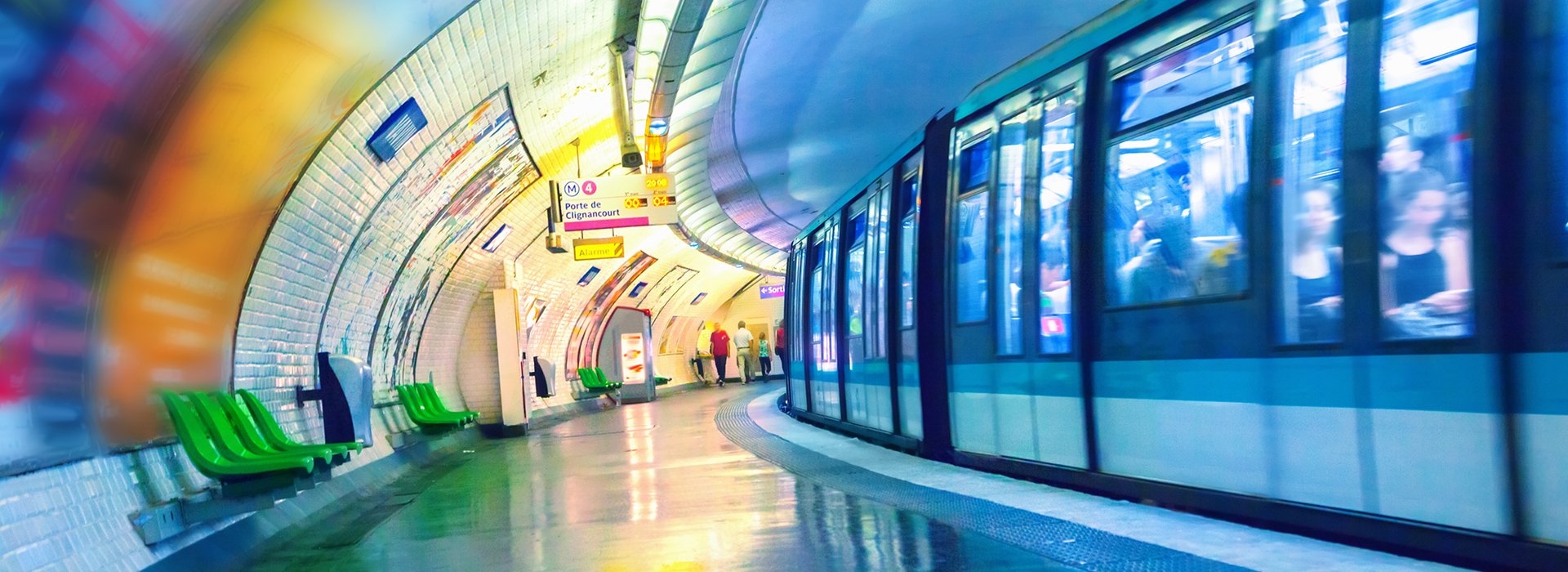
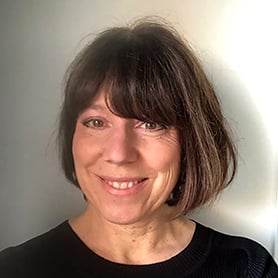
Nathalie Ponzevera
Director of Health and Safety, RATP Group
Q.
How has your career progressed and what skills do you think have shaped your journey into safety?
I studied management and logistics and spent many years working in this area including production, warranty, and inventory management roles. In my early career safety was not a subject I encountered, and it was only in 2011 when I moved to the position of production unit manager, at Air France Industries, that I really became aware of the issues related to safety at work. In my experience, there is nothing better than spending time in the field to get a feel for the risks and I often worked closely with the mechanics to improve risk prevention in the workshop. It really interested me, and I had always enjoyed finding solutions and working on projects that have an impact and there’s no greater impact than keeping people safe. So, I decided this was the direction I wanted my career to move into and trained in risk prevention. This gave me the skills to move to the role of Director of Health, Safety and Quality of Work Life at Air France. Now I am at the RATP Group where I oversee prevention and occupational health. I really enjoy working with people and teams, and supporting them. It’s about sharing, helping my team to progress, finding solutions together, looking at background and what we have achieved. The most exciting and interesting thing for me is to go on the ground and speak with operational teams, understand the risks, talk about them and make improvements. It is very rewarding to see the progress.
“Good leadership is a manager who knows they need to be with people to build a strong safety culture, speaking every day, being on the ground, helping people to find solutions.”
– Nathalie Ponzevera, Director of Health and Safety, RATP Group
Q.
Changing mindsets and behaviours are an important driver of safety excellence. In what way can company culture and good leadership make a difference when creating safety in the workplace?
If you are the only one talking about safety, there will always be accidents. Companies that want to have a good safety culture need to be addressing the subject to all employees from top management to the field. Allowing everyone to engage is key but what really makes the difference is the visibility of managers in the field, engaging with people, talking about safety, and showing they care. It’s very easy for managers to feel they are too busy, but this is simply a case of prioritising and meeting with teams on the ground to discuss safety and must be the priority for managers. A good manager is the one who knows they need to be with people to build a strong safety culture, speaking every day, being on the ground, helping people to find solutions. A visible leader who understands the problems of the work, listens and actions practical solutions can only come from having proximity to the team.
Q.
The last few years have seen a lot of disruptive events, how has this impacted your role in terms of the need to consider psychosocial risks and the consequences of this on mental health?
There’s no doubt that COVID 19 has undeniably strengthened the collaboration between occupational health and safety professionals, which is good news and has led to a closer working relationship to define occupational health and safety policy. In addition, since the pandemic there has been a shift from leaders to give more priority to actions that contribute to a better quality of life at work. I think it is much more widely recognised that the wellbeing of employees directly impacts performance, and this isn’t just physical health issues, but also mental health issues and we need to support both. I have certainly seen a greater understanding of this and consequently we have more means at our disposal to act and improve the wellbeing and working conditions of our employees. Quite rightly, health and safety are a priority, and this is increasingly seen in strategic plans.
“Since the pandemic there has been a shift from leaders to give more priority to actions that contribute to a better quality of life at work.”
– Nathalie Ponzevera, Director of Health and Safety, RATP Group
Q.
How do you think safety programmes can benefit from innovative and technological change and are there any challenges associated with this?
Innovations and technological developments are levers for improving daily workplace safety. For example, exoskeletons to limit the impact of heavy loads, robots for sanding activities, drones to inspect tasks at height. Each of these innovations makes it possible to limit or even eliminate certain risks. Networked integrated risk assessment information systems also make it possible to share risks and increase risk awareness. I also anticipate that in the future artificial intelligence will be able to use a simulated photos to propose prevention and protection action plans. But as with anything new, these changes bring new challenges. New technology not only takes a long time to develop but can also take time to implement. It requires acceptance from the team, and this shouldn’t be underestimated. It’s a big deal and sometimes you have to accept that even if the new technology may have a positive impact on day-to-day operations - if it’s not accepted by the employees, it may not be viable. Ultimately if there’s no engagement, it can be difficult to take it further and get the desired impact.
Q.
What impact do other practice areas such as sustainability, operational risk management and operational excellence have in helping to shape safety practices and build a business that can withstand industry volatility?
Other practice areas are strong levers for changing and shaping health and safety practices. Sustainability has become imperative for companies due to the increased focus on social and environmental responsibility, and occupational safety is one of the issues. A company that controls its safety risks is a responsible company Effective risk management reduces the likelihood of major disruptions, protects business reputation, and improves decision-making by anticipating potential threats. When we talk about optimising processes, improving efficiency, and maximising productivity within a company, the impact of process changes on safety risks is paramount.
“Thank people and let them know that there have been no serious incidents because they respect the processes, they follow the rules and look out for each other. It’s so important to communicate this message.”
–Nathalie Ponzevera, Director of Health and Safety, RATP Group
Q.
Based on your own experience, what would you say are the top best practices when building a safety programme in your industry?
Firstly, you have to make sure safety is spoken about every day. Keep it on the radar for everybody by showing a visible commitment, including managers leading by example with field visits and face to face safety discussions. It’s also about compliance with the Life Saving Rules with employees respecting safety procedures, for example wearing protective clothing. It’s the basics that need to be respected, as these basics have a big impact on safety performance and culture. It’s also important to encourage open discussions whereby people feel they can raise concerns and be open and honest about their mistakes. People need to feel that if they make a mistake, it’s better to speak about it because it helps the organisation to investigate and make improvements. Finally, communicate and celebrate the success of all this hard work – thank people and let them know that there have been no serious incidents because they respect the processes, they follow the rules and look out for each other. It’s so important to communicate this message.