Harnessing Operational Strategies as Catalysts Towards Sustainability & ESG Goals
In a rapidly evolving global landscape, the integration of sustainability & ESG into business strategies and operations is now widely recognized and understood to be a pre-requisite for companies to survive, succeed, and thrive. Consequently, sustainability & ESG goals and targets have become a top priority in boardrooms across the world. Tackling sustainability through an operational improvement lens is an effective complement to capital-intensive approaches, often yielding more rapid results.
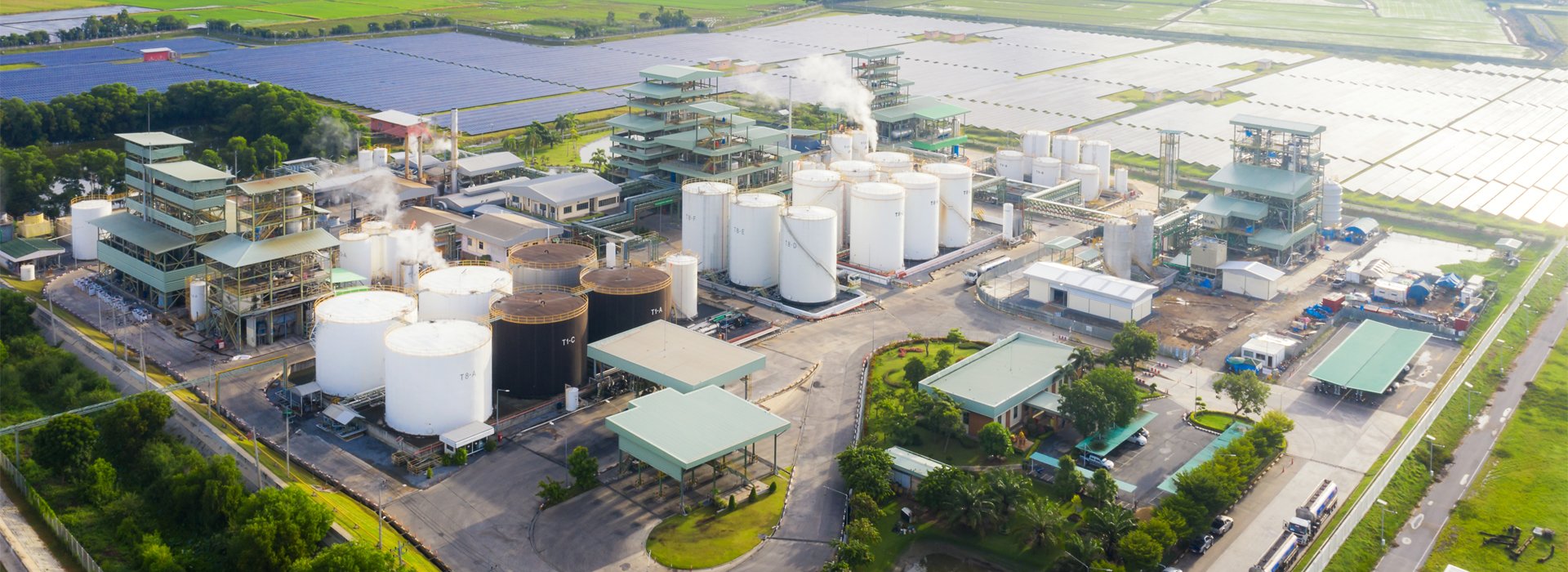
Operations should be treated as a crucial influencer of sustainability outcomes. One of the biggest challenges faced by CEOs and COOs is to convert their company’s Sustainability & ESG vision into a concrete, well-defined action plan and ensure their organisation, with its systems, processes, and personnel, is geared up to follow it.
By examining the intricate connections between sustainability and operations, leaders should aim to inspire their teams to adopt innovative approaches that align profitability and operational excellence with environmental stewardship and social wellbeing.
This approach will help companies improve their Sustainability performance without relying on capital-intensive solutions exclusively. Understanding these connections will also help foster a culture of Sustainability, whereby sustainability becomes an integral part of operations, rather than a standalone initiative - driving positive change for the long term.
Operational excellence – with its focus on improving business processes, resource efficiency, waste management, among others – has a direct impact on the Sustainability & ESG performance of a company.
George Serafeim, in his book ‘Purpose and Profit: How Business Can Lift Up The World’, highlighted it this way:
"It is not always necessary to fundamentally change what you do, if you are able to find ways to run your business more efficiently, especially when those new efficiencies coincide with the environmental and social shifts going on in society.1"
In other words, your current operational setup no doubt offers multiple opportunities to start realising your Sustainability objectives, which in turn leads to an improvement in your company’s value.
Non-capital improvement is the hallmark of resilient operations; those which deliver year on year performance improvement with existing assets.
Excellence in operations is key for leaders to shift their Sustainability & ESG goals into actions and outcomes
Understanding the interlinkages between operational improvements and sustainability performance
Leaders can leverage operational excellence interventions to drive their desired sustainability outcomes, based on their interlinkages, as illustrated in Figure 1 below.
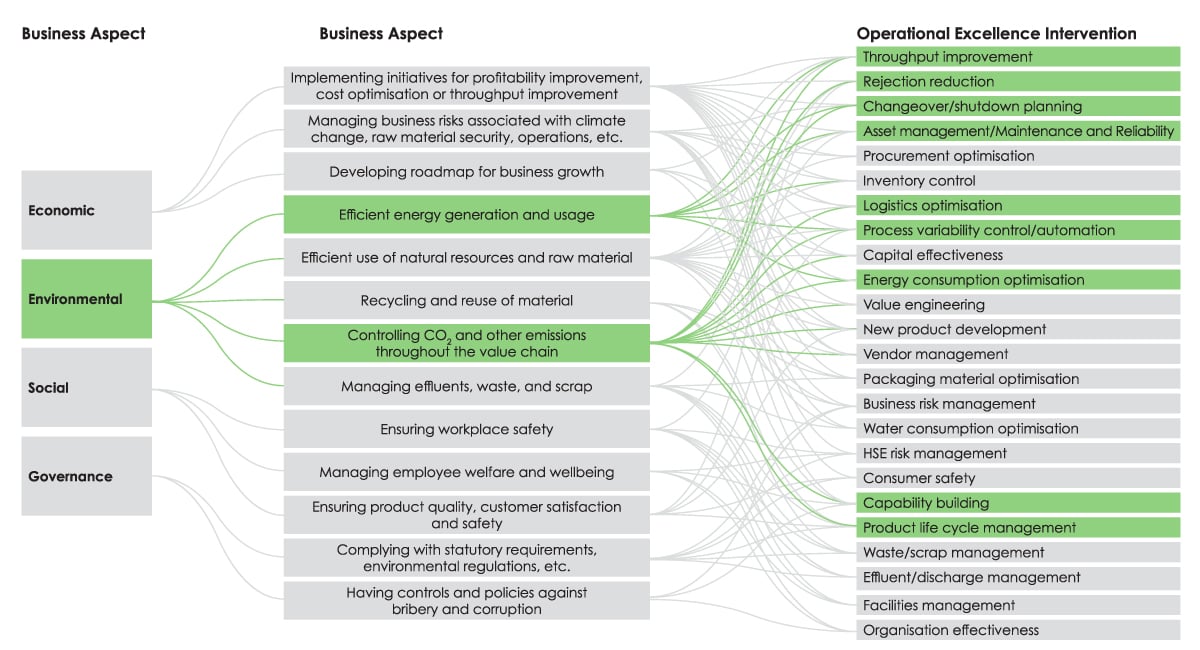
Figure 1: Mapping Sustainability & ESG components with Operational Excellence interventions (non-exhaustive)
The graphic illustrates how Sustainability outcomes can be realised through multiple combinations of operational excellence interventions. Consider the simple example of a leader wanting to reduce the environmental impact of their business. Several levers can help achieve this. Highlighted above are various operational levers that could be assessed to impact energy efficiency as well as emissions control throughout the value chain.
As a distinct example, if the focus were on raw material consumption, the more specific question to explore would become:
‘What operational changes are the most promising to reduce raw material consumption?’ Throughput improvement, rejection reduction, value engineering, etc. can all lead to optimised raw material consumption.
Identifying and tracing interlinkages reveals the multiple options across the operations value chain leaders can leverage to achieve a sustainability outcome through operational excellence, such as capital avoidance, cost reduction and throughput improvement to name just a few.
A proven approach
Numerous companies have achieved improved sustainability performance and realised it faster by using this approach. When done well, they will also lead to enhanced business performance.
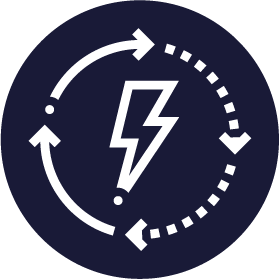
Optimising consumption
Optimising energy consumption (or optimising energy intensity) is one of the most common sustainability targets set by companies. Introducing new, energy efficient technology is a straightforward way to achieve this, but it is not feasible to continuously invest in the latest technologies. A more cost-effective way relies on common problem-solving tools and principles of continuous improvement, which will identify the energy intensive hotspots and optimise energy consumption through levers such as reducing process variability, reducing equipment downtime, better planning of shutdowns, stoppages, and changeovers, etc.
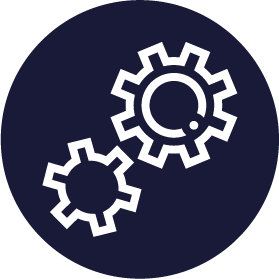
Maintaining assets
Maintenance & Reliability (M&R) is one of the most critical areas to keep the manufacturing processes running in asset-intensive industries. In process industries like chemicals, petrochemicals and oil & gas, unplanned downtime can lead to costly accidents, production loss, off-quality production due to interruption, increase in energy consumption and increase in maintenance and repair costs – all impacting the profitability and sustainability performance. The elimination of significant reliability issues can lead to immediate, tangible benefits. A 2022 report suggests the estimated cost of unplanned downtime for Fortune Global 500 companies is as high as $1.5 trillion per year (11% of their yearly turnover).5

Reducing emissions
Reducing greenhouse gas emissions is a major challenge taking a pragmatic approach will often bear quick results.
Tata Steel achieved nearly 4% reduction in specific power consumption in one of its mills by simply optimising the planned stoppages and mill pacing.2
Vedanta explored the possibility of stopping one out of the three gas turbine generators powering one of its offshore oil rigs. After enhancing the power system protection settings and load shedding logic, the company was able to save ~7,000 SCMD (standard cubic meters of gas per day) over 132 days during the winter of 2022-23.3
One of the 500+ sustainability improvement initiatives implemented by BASF in 2022 involved fully utilising the existing flash steam, at a plant in Kuantan site in Malaysia, through an optimised control system enabling over 1,500 metric tons per year of CO2 emissions reduction.4
In one case, by implementing Total Productive Management (TPM), a steel manufacturer was able to reduce its energy cost by up to 20% by ensuring better condition of equipment.6
Operations leaders thus need to understand these inter-linkages in the context of their companies and industry. By optimising processes, engaging stakeholders, and promoting recycling and circular economy concepts, companies can create a more sustainable and resilient value chain. Generally, the key areas of focus include resource optimisation, waste reduction, supply chain collaboration, green product design, employee engagement, performance measurement, and stakeholder engagement. By implementing these strategies, companies can achieve long-term sustainability objectives while enhancing operational performance and maintaining a competitive edge.
A well-defined asset management strategy can lead to:
|
The approach leaders can adopt to achieve their Sustainability & ESG targets
An effective Sustainability & ESG transformation journey starts with a strategy – a long-term vision. Generally, this is set by the top management or the board of the company. For example, more than one-third of the world’s largest firms are now committed to achieving net zero.7 The CEOs and COOs face the challenge of translating this strategy into operational targets.
Changing mindsets and culture underpins this approach
In the dss+ article, ‘From intent to impact: enabling the sustainability transformation through capabilities and culture,’ we cautioned such transformations entail significant operational and mindset challenges.10
Often, a change in the organisational mindset will be required to embrace operations and sustainability holistically. In this culture, employees from the top floor to the front line understand the importance of sustainability and are empowered to contribute to its implementation.
These challenges can be addressed through a combination of operational targets and mindset evolution.
Looking at the targets and the areas where most potential for improvement exists, leaders can address these opportunities through the interlinkages identified. For example, a leader can look at product life cycle management to drive sustainable product development, which can help end-of-life disposal issue and reduce raw material costs through better recycling.
Unilever has defined its sustainability vision in its Climate Transition Action Plan. This strategy has been divided into three principal targets of short-term emissions reduction, medium-term emissions reduction, and long-term net zero value chain. The plan outlines the steps the company will take to reduce emissions to zero within its own operations by 2030 (medium-term) and to net zero across its value chain by 2039 (long-term net zero).8
Decarbonisation, energy transition, and energy efficiency improvement initiatives are being leveraged to reduce emissions in Unilever’s operations.
In 2022, the operational energy consumption by Unilever factories was reduced by 4% as compared to 2021.9
Dow was able to chemically recycle polyurethane foam from end-of-life mattresses to create a raw material for producing polyurethane. This raw material contained about 40-45% recycled content and helped in reducing over 50% of CO2 equivalent emissions in comparison with the standard production process.11
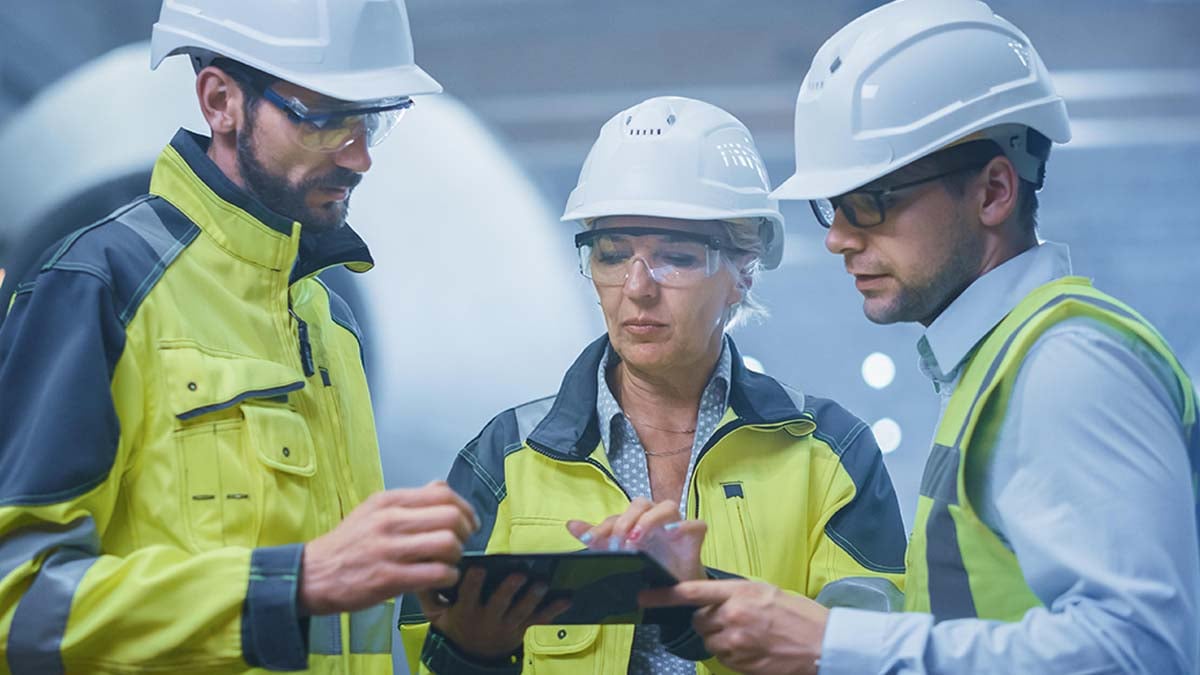
While target-setting has its merits, relying solely on it to drive cultural change may result in a biased focus on shortterm benefits rather than fostering a comprehensive shift towards long-term sustainability. Cultural transformation is not a linear progression but rather a dynamic process that demands holistic and adaptable strategies. Organisations seeking to cultivate a culture of sustainable operations must recognise change has to be cultivated, not commanded. This begins with education and awareness initiatives that communicate the intrinsic value of sustainable practices, not just in terms of environmental stewardship, but also in enhancing efficiency, resilience, and longterm profitability.
To deliver such a transformation, a combination of top-down leadership and grassroots innovation is essential. Leadership plays a pivotal role in setting the tone, aligning incentives, and showcasing commitment through actions, signalling this cultural shift is not an arbitrary initiative, but a strategic imperative. Significant cultural changes often sprout from the grassroots level. Empowering employees to voice their ideas, experiment, and contribute to the evolution of sustainable practices can harness the creativity and diversity within the organisation.
Operational excellence, fundamentally relies on a motivated and knowledgeable workforce. Companies can promote this, and Sustainability & ESG performance, by developing the workforce capability, focusing on environmental awareness, social responsibility, and ethical business practices. They can further align the workforce to the company’s vision by providing them clear operational targets and recognition for achieving them. Engaging employees in sustainability initiatives in this way, and recognising their contributions fosters a culture of sustainability within the organisation.
Companies must measure and track sustainability performance regularly to ensure progress towards their goals. Here too, operational excellence involves establishing key performance indicators (KPIs) to address Sustainability & ESG factors. Monitoring, improving and reporting on these metrics can enable companies to identify areas for further improvement, demonstrate transparency to stakeholders, and drive continuous sustainability progress towards resilient operations.
Operational excellence can thus help in integrating sustainability into operations, thereby enabling ‘sustainability transformation’.
A manufacturing client partnered with dss+ to review its approach to energy management. This partnership led to:
Engagement of front-line leaders gained to sustain this effort |
In summary
Sustainability & ESG will continue to be an area of priority for any organisation. Achieving better Sustainability & ESG performance does not necessarily have to be achieved through drastic changes, which incur high capital investment or by de-prioritising other initiatives. Changes stemming from operational improvement can help an organisation become a better Sustainability & ESG performer, with more resilient operations, whilst ensuring business goals are achieved.
By comprehending the inherent interdependencies between sustainability and operations, businesses can unlock new opportunities, reduce their environmental footprint, and contribute to the well-being of both present and future generations. This paper seeks to inspire and guide business leaders in their journey towards sustainable and resilient operations, fostering a harmonious relationship between profitability, operations and planetary stewardship.
CEOs and COOs have a very important role to play in prioritising the identification and implementation of these interlinkages with the most promise. They also need to ensure the workforce is tuned to this ambition. Only then sustainability can be truly Integrated in the operations in a seamless manner.
SOURCES:
- George Serafeim, 2022. Purpose and Profit: How Business Can Lift Up the World, HarperCollins Leadership
- Tata Steel Integrated Report & Annual Accounts 2018-19, Annexure 11
- Vedanta Integrated Report and Annual Accounts 2021-22
- BASF Report 2022
- The True Cost of Downtime 2022: How much do leading manufacturers lose through inefficient maintenance, Senseye.
- Ahuja I P S and Khamba J S 2007 An evaluation of TPM implementation initiatives in an Indian manufacturing enterprise J. Qual. Maint. Eng. 13 p. 338-52
- Strategic Focus: The Role Of Operations Managers In Implementing Net Zero Strategies
- Unilever Climate Transition Action Plan
- Unilever Climate Action
- From intent to impact: enabling the sustainability transformation through capabilities and culture
- Dow 2021 Environmental, Social & Governance Report
- Asset Performance Management: Blazing A Better Path to Operational Excellence, Aberdeen Group
Contributing to this paper were:
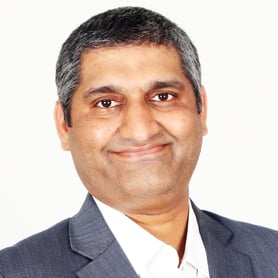
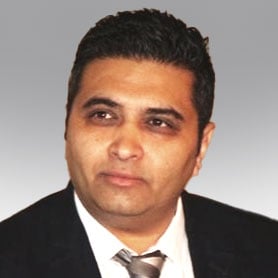
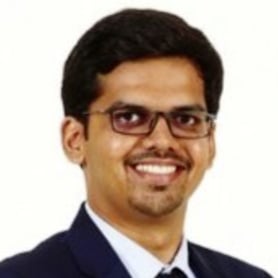
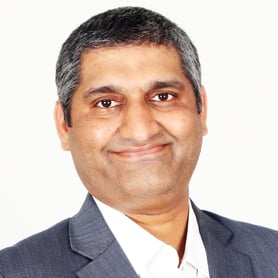
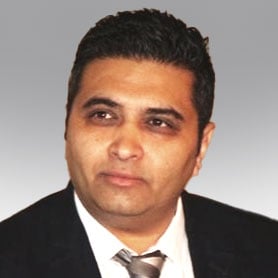
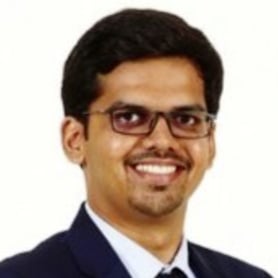